而制动踏板,也就是人们俗称的“脚刹”,却因为与汽车的安全性有着更为密切的关系,对自身的强度、刚度、扭转载荷有着更高的要求,彼时尚未实现从金属向复合材料的转变。
来自德国的汽车一级供应商Boge Rubber & Plastics Group(以下简称Boge)宣称推出了世界上首个量产热塑性复合材料汽车制动踏板,满足了汽车厂对安全性和经济性的要求。
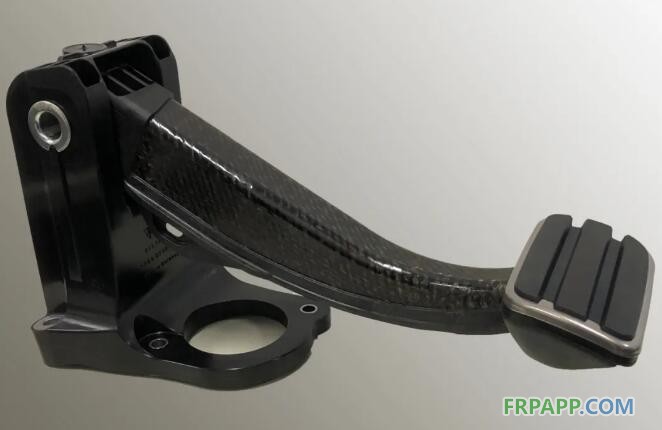
这款创新的制动踏板采用了独特的设计方案,混合使用了三种不同的复合材料,引入了与众不同的生产工艺。
Boge公司专业从事汽车减振、传动、底盘、轻量化模块以及踏板箱(包括制动、离合、油门)相关零部件的研发和生产。自2008年起,公司开始使用连续纤维有机板和短切玻纤,利用复合模塑工艺(overmoulding)生产汽车零部件。2018年,又引入了热塑性单向带,并通过工艺的创新缩短了生产周期、降低了成本、扩大了业务量。
“2015年的某一天,老板跟我说,这些创新都很不错,但是如果能寻找到更大的应用市场,把用量提升上去就更好了。”Boge公司全球创新中心总经理Daniel Häffelin博士工程师表示,“于是,我们的工程师团队一起做了头脑风暴,最后把目光聚焦到汽车制动踏板这一细分产品上了。”
想要说服汽车制造商采用新的产品,必须充分证明它的经济性。“我们认为现有工艺已经把生产周期压得够短了,进一步下调的空间有限,所以唯一的出路就是通过提高纤维的使用效率来降低成本。”
然而,简单地减少用量,把制动踏板做得更小、更薄显然行不通,因为制动踏板对形状和尺寸有严格的要求,更不用说对它关系着汽车的整体安全性能。因此,研究的方向锁定在如何对纤维取向进行精准的控制,从而减少部件的壁厚和非关键区域的纤维用量上。
“想要减少纤维用量,还要保持足够的强度和刚度,在运动和医疗市场上的通常做法是引入拾-放设备(Pick-and-Place),但是那样做太贵了。”Boge公司首席执行官Torsten Bremer博士表示,“于是,我们不得不尝试寻找新的工艺路径。”
“当时我们已经开始和一些汽车厂家合作研发全复合材料制动踏板。”Boge公司执行副总裁Burkhard Tiemann回忆说,“我们在2015年向他们做出了承诺,3年后我们做出了第一批产品。”
三种材料的混合使用
Boge公司针对制动踏板的不同位置分别使用了三种不同的材料。
1. 壳结构是踏板的主要承重结构,需耐受最高3000牛顿的压力,同时还需要保证它足够轻薄、性价比足够高。为此,Boge公司选用了德国朗盛公司生产的连续玻纤有机板。
2. 对于有机板上需要局部增强的部分,Boge公司使用了美国塞拉尼斯公司提供的单向玻纤带,并遵照汽车厂商对特定温湿度条件下材料应变曲线的要求,通过有限元分析的方法计算出铺放的路径。
3. 另外,为实现踏板中的功能性几何形状,Boge公司使用了由多个供应商提供的短切玻纤,利用复合模塑工艺形成加强筋和其他辅助结构。
与上述3种增强材料配合使用的基体材料,是已在汽车行业中广泛采用的黑色尼龙6。如果汽车厂商另有要求,Boge公司亦可在复合模塑工艺过程中使用尼龙6,6作为替代。
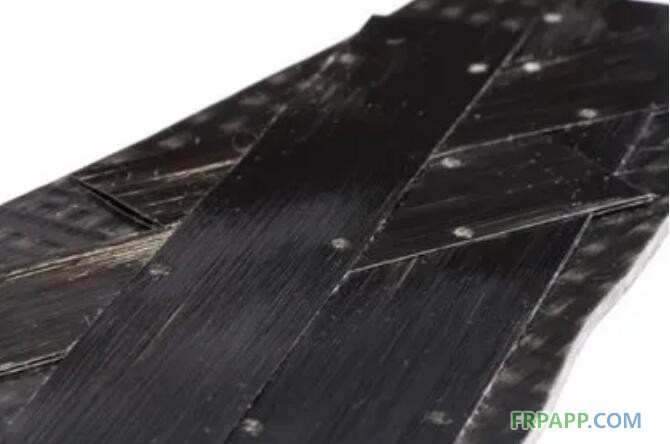
通过混合使用三种不同形态的玻纤增强材料,Boge公司实现了对纤维取向的精确控制,既满足了制动踏板的性能要求,又避免了材料的浪费、减少了壁厚、缩短了生产周期、降低了部件成本。
工艺流程
通过与德国自动化生产线制造商M.A.i. GmbH & Co. KG的合作,Boge公司为这款全热塑性复合材料制动踏板设计了一套三步走的工艺路线,实现了1)1分钟快速成型;2)高度自动化;3)个性订制化。
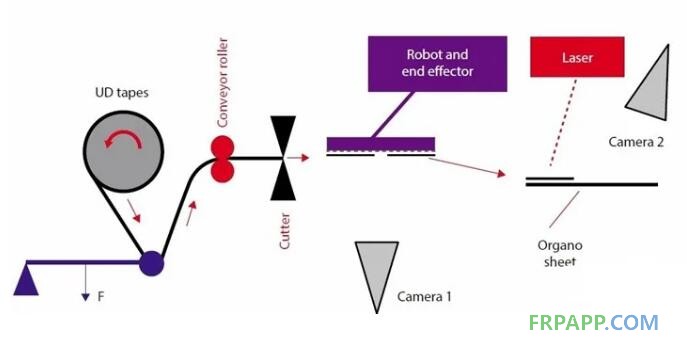
生产开始前,工作车间里先备好两堆经过预成型的有机板和四卷单向玻纤带。
1. 生产开始时,机器人拾取一片有机板,将其移至工作台上;同时,将单向玻纤带裁至所需长度,置于传送带之上。接着,轮转式拾放设备(Pick-and-Place)依次拾取四条单向带,在此过程中由监控摄像头检查每条单向带的质量、尺寸和位置是否符合要求。然后,设备按照程序中写入的位置依次将单向带贴到有机板表面,并用激光进行多点焊接,防止单向带发生位移。
此过程不间断,直至设计方案中所有单向带全部贴至有机板上的正确位置。整个过程完全通过数控技术实现,客户的个性化需求可以通过调整程序充分满足。所有环节都在摄像头及传感器的监控下完成,确保生产过程与设计方案完全一致。
2. 而后,为保证生产效率,经过局部增强的有机板被送入红外加热炉进行预加热。在此过程中,单向带和有机板中的特殊抗氧化成分会保护树脂系统免于热损伤。进而,完成预热的有机板被快速送入预成型腔,在高压条件下弯折成U型,并保证较高的表面质量。同样地,这个过程也全程受到质量监控。
3. 最后,温热的预制件被转入注塑模具,与短切玻纤增强尼龙复合材料进行复合模塑,生成包括加强筋在内的辅助几何结构。完成脱模后,进行快速的修剪和检查,但无需喷漆或表面处理。
未来市场
该全热塑性复合材料制动踏板,尺寸为350 × 90 × 60毫米。与早先的设计方案相比,有机板用量减少了33%,名义壁厚从3毫米降至2毫米。
它的重量约为金属踏板的一半,强度与后者相近,甚至高于后者,有助于提升驾驶者的驾驶体验;它的生产成本与铝制踏板近似、略高于钢制踏板。
另外,每个踏板都拥有自己的专属身份二维码,便于日后溯源。
2018年,这款全热塑性复合材料汽车制动踏板进入量产阶段,单个部件的生产周期约为1分钟,现有生产线的年产量可达到100万件。
“随着汽车行业逐渐向电动方向发展,制动踏板的设计也将因为电气化集成的要求变得更加复杂,这将赋予复合材料更大的竞争力。” Häffelin博士表示。