模具是复合材料构件制造用的主要工艺装备,用以确定制件形状、结构关系、控制外缘和获得良好的表面质量, 在模具上完成复合材料聚合固化,有时还在成形模上进行预浸料的铺叠, 复合材料模具的设计制造对复合材料构件的产品质量影响较大, 要求模具的设计合理 。国内外学者对普通的机械零件成型模具CAD/ CAM 技术进行了深入的研究 , 而未见对复合材料构件成型模具的CAD/CAM 技术的研究。复合材料构件成型模具根据其材料可分为金属模和复合材料模, 因其特殊的结构及工艺, 本文结合企业的实际需求, 以典型的复合材料构件成型模具结构为研究对象, 研究了现有模具设计过程中存在的问题, 提出了改进的设计方法, 将复合材料构件成型模具设计分为3 个阶段进行: 成型曲面的检测, 模具体的设计, 模具支架的参数化设计, 并开发了相应的设计系统。
1 典型复合材料构件模具结构分析
复合材料构件成型模具的结构随着工艺方法的变化而变化, 比较有代表性的是真空袋( 热压灌成形方法的模具) , 如图1 所示为薄板框架式模具的结构示意图, 包括用于铺帖复合材料成型模具的过渡模, 其结构设计包含的基本内容有以下几个方面: 模具型面要具有较高的精度, 这是复合材料构件成型的基本依据; 如果模具体是金属模, 其型面需采用数控加工, 在设计过程中应满足加工的具体要求, 如果是用复合材料( 通常使用纤维增强树脂)来做模具体, 在国内大都采用人工铺帖成型的方式
进行制造, 型板架大都是金属管材或角材组成的框架, 其通过数控加工的方式制造的, 在设计过程中要考虑到铺帖成型的模具体要在允许的误差范围内, 才能保证成型模具体与型板架成功装配, 保证模具体的精度。此外, 型架板结构主要考虑保证在加温时模具体不易变形, 而且使得空气流在模具体上下表面任意流动。
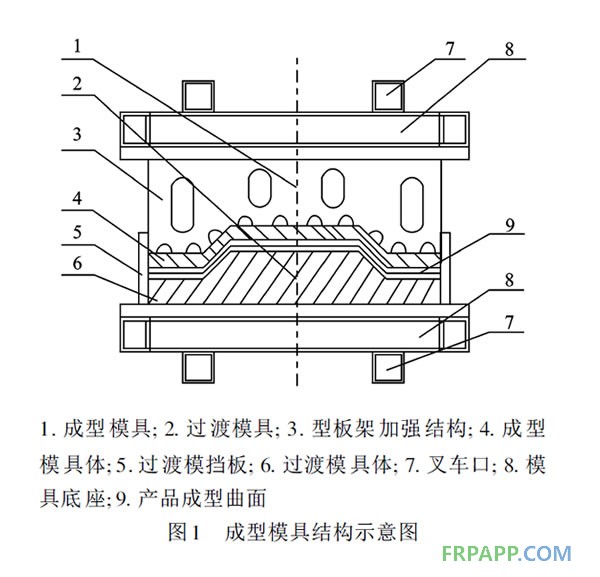
2 现有设计存在的问题
在以数字量传递的设计中, 复合材料构件模具的设计原始依据是飞机构件的外形曲面, 模具的设计过程受上游数据的影响较大。现有的设计中, 设计者没有对上游曲面数据进行客观的评价, 往往只有在制造的过程中才能发现产品数据的不足, 出现加工迭代的现象, 造成资源浪费。本文结合并行工程及可制造性的设计思想, 在设计阶段能根据现有的资源条件等, 对接收的产品曲面数据进行综合评价, 辅助设计者合理地作出判断, 对产品数据的不足及时地进行修改, 满足要求。
复合材料构件模具体设计的主要工作是对成型曲面的偏置, 成型曲面是大量的曲面片拼接而成的, 其特征非常复杂, 在对复合材料构件模具体设计过程中, 对成型曲面进行偏置时, 存在局部因曲率过大而无法整体偏置的问题, 使得设计人员不得不将原始曲面进行拆分, 而分别对曲面片进行单独偏置, 然后将所得的偏置曲面按要求进行拼接。这样不仅改变了原始的设计数据, 使得设计结果有较大的偏差, 往往需要设计员进行无数次的反复尝试, 才能得到合理的解, 而且对曲面的处理, 本身就是很复杂的过程, 依靠人工的手段, 质量得不到保证, 而且降低了设计效率。本文在满足误差的前提下, 提出了基于误差约束的复杂曲面整体偏置方法。
型架板结构的设计过程中, 设计者对每一个结构的设计都从草图进行, 设计步骤烦琐, 设计效率低下, 依赖设计人员所掌握的知识和经验, 不同背景的设计人员所设计的产品模型差异很大, 不能满足产品规范性的要求。通过对大量复合材料构件模具的总结, 发现其型架板结构大同小异, 本文利用参数化设计手段对其进行标准化, 建立其参数化设计模型, 设计者只需对给定的几组参数进行赋值,便可以生成满足条件的型架板结构, 减少设计者的大量而烦琐的重复绘图工作, 提高设计效率。
3 成型曲面的检测方法
复合材料构件因其特殊的结构, 其成型表面是通过大量的曲面片拼接而成的, 表面质量较差, 因此进行模具设计, 特别是以数控加工方式加工的产品时, 必须要对成型面进行可加工性检测, 判断成型面在企业现有的加工资源条件下能否高效加工出合格的产品。本文考虑影响成型面可制造性的因素包括: 加工难度、加工设备、刀具、装夹方式等, 并将这些因素映射为成型面的几何特征属性, 使设计者在设计过程中能根据几何特征合理判断其可加工性。作者在文献[ 6] 中详细论述了成型曲面的检测方法, 本文简述如下。
3. 1 成型曲面几何特征属性的提取
影响模具可加工性的属性可分为产品属性层、过渡属性层和用户属性层。产品属性层指影响其可加工性的总体属性, 用A 表示。过渡属性层指由产品属性向用户属性过渡的中间属性集合, 其可分为成型曲面的几何形状属性G, 现有的制造资源属性S 以及模具几何属性P。根据成型曲面特征对加工工艺性的影响的不同, 将成型曲面的几何形状属性可进一步分为局部特征属性Q( 如曲面上某点的曲率、曲面的凹凸性等) , 和整体特征属性Z ( 如曲面是否为单值曲面等) 。制造资源属性可进一步分为加工设备属性E , 刀具属性C, 装夹属性F 等。模具的几何属性主要是指模具几何特征对成型曲面的加工工艺性产生影响的属性, 如在数控加工, 是否以模具上的某特征作为加工成型曲面的定位基准, 将会影响成型曲面的加工工艺性。本文主要考虑在设计模具时, 将加工成型曲面的装夹定位的基准设计为模具的局部特征, 即将设计基准和定位基准定义为同一基准, 简化模具的设计步骤和装夹的工艺, 称为模具的基准属性B。它们之间的层次映射关系为A = {G , S , P } = {Q, Z, E, C, F, B} , 各属性的层次化树状结构如图2 所示, 用户最终只需关注用户属性层的属性, 简化后续的设计与计算。
在以数字量传递的设计中, 复合材料构件模具的设计原始依据是飞机构件的外形曲面, 模具的设计过程受上游数据的影响较大。现有的设计中, 设计者没有对上游曲面数据进行客观的评价, 往往只有在制造的过程中才能发现产品数据的不足, 出现加工迭代的现象, 造成资源浪费。本文结合并行工程及可制造性的设计思想, 在设计阶段能根据现有的资源条件等, 对接收的产品曲面数据进行综合评价, 辅助设计者合理地作出判断, 对产品数据的不足及时地进行修改, 满足要求。
复合材料构件模具体设计的主要工作是对成型曲面的偏置, 成型曲面是大量的曲面片拼接而成的, 其特征非常复杂, 在对复合材料构件模具体设计过程中, 对成型曲面进行偏置时, 存在局部因曲率过大而无法整体偏置的问题, 使得设计人员不得不将原始曲面进行拆分, 而分别对曲面片进行单独偏置, 然后将所得的偏置曲面按要求进行拼接。这样不仅改变了原始的设计数据, 使得设计结果有较大的偏差, 往往需要设计员进行无数次的反复尝试, 才能得到合理的解, 而且对曲面的处理, 本身就是很复杂的过程, 依靠人工的手段, 质量得不到保证, 而且降低了设计效率。本文在满足误差的前提下, 提出了基于误差约束的复杂曲面整体偏置方法。
型架板结构的设计过程中, 设计者对每一个结构的设计都从草图进行, 设计步骤烦琐, 设计效率低下, 依赖设计人员所掌握的知识和经验, 不同背景的设计人员所设计的产品模型差异很大, 不能满足产品规范性的要求。通过对大量复合材料构件模具的总结, 发现其型架板结构大同小异, 本文利用参数化设计手段对其进行标准化, 建立其参数化设计模型, 设计者只需对给定的几组参数进行赋值,便可以生成满足条件的型架板结构, 减少设计者的大量而烦琐的重复绘图工作, 提高设计效率。
3 成型曲面的检测方法
复合材料构件因其特殊的结构, 其成型表面是通过大量的曲面片拼接而成的, 表面质量较差, 因此进行模具设计, 特别是以数控加工方式加工的产品时, 必须要对成型面进行可加工性检测, 判断成型面在企业现有的加工资源条件下能否高效加工出合格的产品。本文考虑影响成型面可制造性的因素包括: 加工难度、加工设备、刀具、装夹方式等, 并将这些因素映射为成型面的几何特征属性, 使设计者在设计过程中能根据几何特征合理判断其可加工性。作者在文献[ 6] 中详细论述了成型曲面的检测方法, 本文简述如下。
3. 1 成型曲面几何特征属性的提取
影响模具可加工性的属性可分为产品属性层、过渡属性层和用户属性层。产品属性层指影响其可加工性的总体属性, 用A 表示。过渡属性层指由产品属性向用户属性过渡的中间属性集合, 其可分为成型曲面的几何形状属性G, 现有的制造资源属性S 以及模具几何属性P。根据成型曲面特征对加工工艺性的影响的不同, 将成型曲面的几何形状属性可进一步分为局部特征属性Q( 如曲面上某点的曲率、曲面的凹凸性等) , 和整体特征属性Z ( 如曲面是否为单值曲面等) 。制造资源属性可进一步分为加工设备属性E , 刀具属性C, 装夹属性F 等。模具的几何属性主要是指模具几何特征对成型曲面的加工工艺性产生影响的属性, 如在数控加工, 是否以模具上的某特征作为加工成型曲面的定位基准, 将会影响成型曲面的加工工艺性。本文主要考虑在设计模具时, 将加工成型曲面的装夹定位的基准设计为模具的局部特征, 即将设计基准和定位基准定义为同一基准, 简化模具的设计步骤和装夹的工艺, 称为模具的基准属性B。它们之间的层次映射关系为A = {G , S , P } = {Q, Z, E, C, F, B} , 各属性的层次化树状结构如图2 所示, 用户最终只需关注用户属性层的属性, 简化后续的设计与计算。
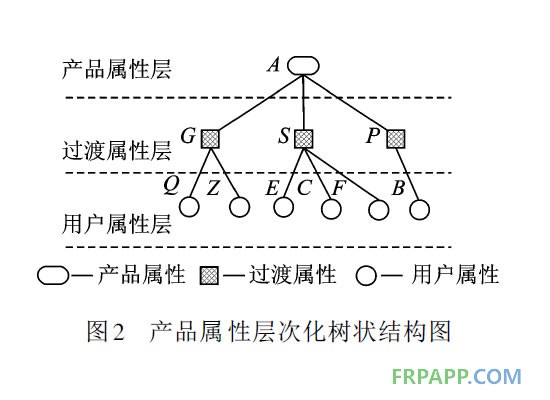