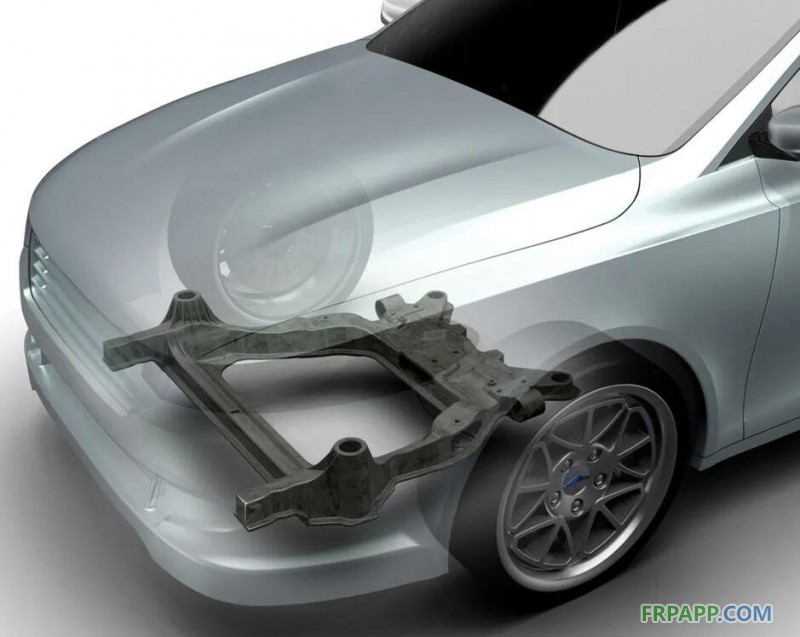
大批量生产的CFRP前副车架:福特与麦格纳国际合作,探索出了一条为满足一款高产量(20万辆/年)汽车需求而尽可能多地使用碳纤维复合材料大批量生产轻质汽车前副车架的技术路线,并揭示了其中的限制条件、挑战和采取的技术解决方案(图片来自麦格纳国际)
通过对短切纤维SMC与无卷曲织物SMC进行共模塑,福特与麦格纳探索了大批量制造汽车底盘前副车架的生产方式。
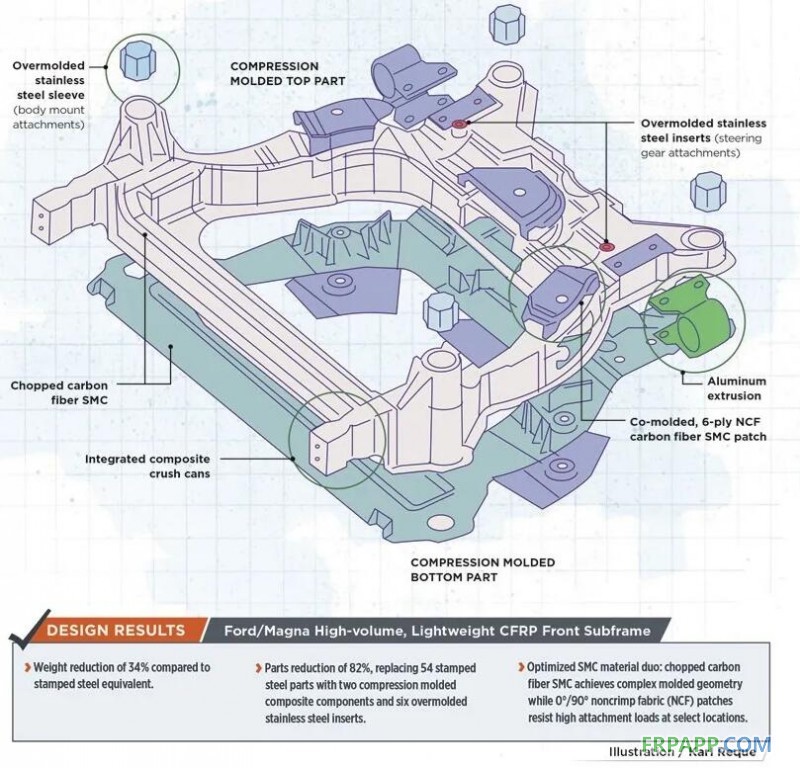
前副车架设计图
几十年来,碳纤维增强塑料(CFRP)的车身框架/底盘部件一直被用于高端跑车和赛车上。
近年来,CFRP的性能和轻量化特征,使其扩展应用到了更高产量的车型中,包括宝马的i3、i8 和7 系,以及奥迪的R8和A8豪华轿车。
然而,这其中的大多数部件,包括车顶轨和横梁、下侧门槛、B柱和后壁,采用的都是连续纤维。
在一个联合研究项目中,福特汽车公司与麦格纳国际通过对连续纤维SMC和短切纤维SMC的组合应用,开发了一种由SMC制成的碳纤维复合材料副车架。
这项应用极具新意,因为该副车架位于汽车前端,用于支撑发动机和底盘部件,包括转向器和用于固定车轮的下控制臂,因而需要承受很高的载荷。
“参与该项目的工程师有几十名。”麦格纳外饰全球创新总监Brian Krull介绍说,“我们有结构工程师、制造工程师、测试工程师、产品工程师和计算机辅助工程(CAE)专家,并有来自我们的客户——福特各个部门的支持,包括车辆建模与仿真。”此外,位于多伦多的麦格纳复合材料卓越中心也为此项目提供了支持。“就像我们在Cosma的车身和底盘团队所做的那样。”Cosma国际研发全球总监Gabriel Cordoba补充道。
“我们想要探索在高产量的汽车上使用CFRP部件所面临的挑战。”福特汽车公司技术主管David Wagner回忆说,“我们的目标是,尽可能多地使用结构CFRP,同时采用能够适应大批量生产(20万辆/年)要求的制造方法,看看能减轻多少重量,以及其中的限制条件和挑战是什么。”
从初步讨论到完成设计,该项目历时一年多。2017年底,原型副车架被交付给福特,并于2018年进入测试阶段。
重新定义设计框架
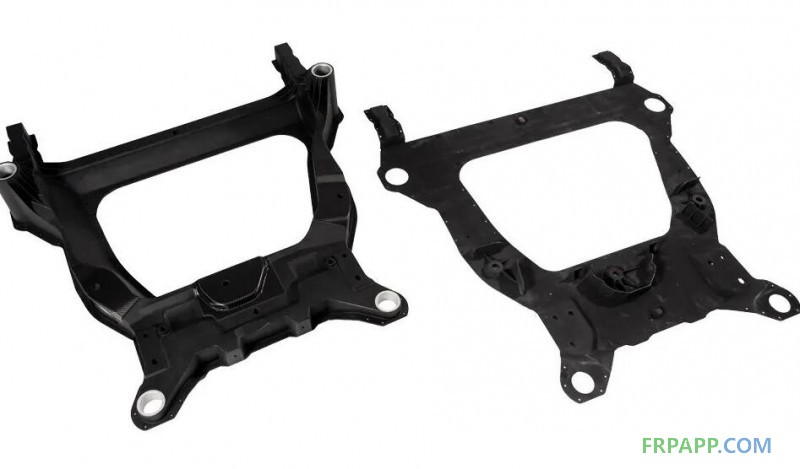
成型的箱形截面上下两个部分:通过拓扑优化的空心箱形截面设计,确保了采用最少的材料提供副车架所需的刚性。上、下两个部分单独成型,然后由粘合剂和铆钉将它们连接起来(图片来自麦格纳国际)
以福特Fusion车型的冲压钢副车架作为基准。“福特为该项目提供了设计空间——车辆级的设计输入,并每周举行一次设计会议。”Wagner说道。
Cordoba解释说:“然后,Cosma采用了那个包容空间,并开始探索可以达到的减重效果。我们如何更改设计以适应那个空间,同时还能满足刚性、强度和耐久性要求呢?”
刚性与对应的包容空间是早期的挑战。“当由钢转向复合材料时,通常会降低模量。”Wagner介绍说,“与基准尺寸相比,我们对新的设计可以改变多少作了定义,并与麦格纳分享了初始的拓扑优化。”
拓扑优化(TO)是一种CAE 分析,可在给定设计空间内优化材料的放置,包括载荷、边界条件和约束条件,并以性能最大化和重量最小化为目标。
“我们从我们自己的拓扑优化开始,去理解临界荷载路径。”Cordoba介绍说,涉及副车架连接点处的载荷包括:控制臂和发动机负载、道路负载、发动机扭矩扭曲和碰撞要求。
“我们必须看看与钢相比我们的刚度有何不同,以及我们想要的性能。”Krull回忆道。由于复合材料提供了树脂、纤维和纤维取向的多样化选择,因此可以特殊订制其性能。“但与仅向钢性能中插入属性相比,这要复杂得多。”他指出。
“插入属性(Plugging in properties)”是指将材料数据输入到软件工具中。
“我们使用了所有的标准软件,包括用于静态分析的Nastran(MSC Software,美国加利福尼亚州Newport Beach)、用于非线性静态分析的Abaqus (Dassault Systèmes,美国马萨诸塞州Waltham)、用于叠层覆盖仿真的Fibersim (Siemens PLC,美国马萨诸塞州Waltham)和用于拓扑优化的HyperWorks(Altair Engineering,美国密歇根州特洛伊),以生成用于分析不同负载情况的有限元模型。”Cordoba说道。
针对不同的载荷、边界条件和材料进行的多次迭代分析,改进了副车架模型。Krull表示,他们对许多复合材料进行了评估。“我们开始将模压成型看作是一种可实现大批量生产的工艺。”他补充道,“SMC很适合做这个部件,而且我们内部已经开发了碳纤维SMC。”
“拓扑优化产生了一种作为最佳解决方案的箱型断面。” Cordoba回忆说,“当我们研究SMC模压成型工艺时,出现的设计是采用两个部件来做到这一点。”因此,该车架包含单独成型的上半部分和下半部分,它们由聚氨酯结构粘合剂和铆钉连接在一起。
共模塑成型两种SMC
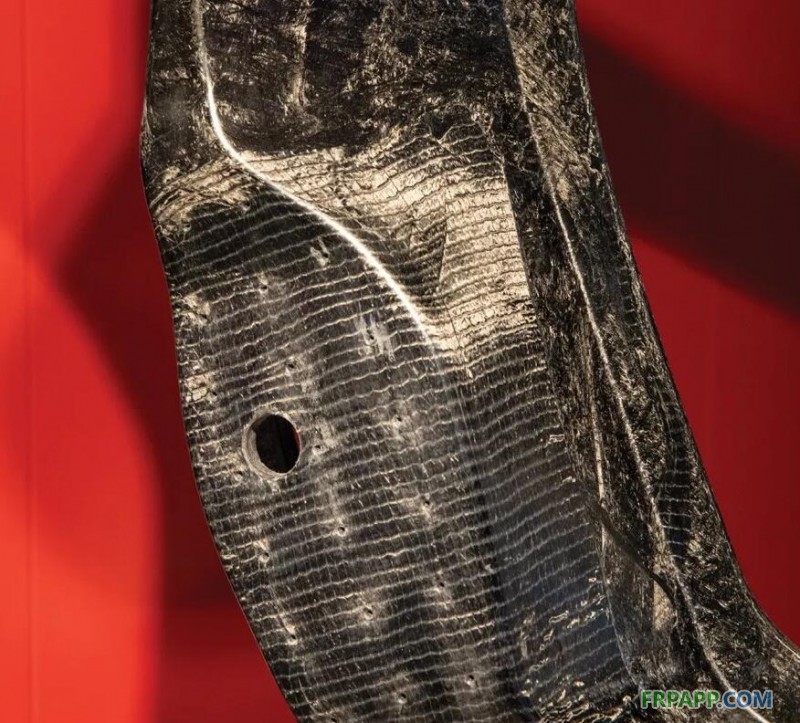
为抵抗高载荷区(如上、下两个部分铆接和粘接在一起的地方)的高载荷,对无卷曲织物SMC补片的共模塑成型也至关重要(图片来自麦格纳国际)
麦格纳利用其玻璃纤维SMC的开发经验及其收购的一条试生产线,研制了碳纤维SMC。
“我们为处理这种SMC用碳纤维而开发了专有技术,而且发现,我们还能用这条生产线生产无卷曲织物(NCF)。”Krull解释道。这种材料与预浸料相似,都是在成型前得到浸润,但独特之处在于,这是在这条SMC生产线上采用同样的树脂生产的,因此而称之为NCF SMC。“当我们在改进副车架的设计分析时,我们使用了这些材料的性能测试结果。”
采用卓尔泰克(Zoltek)的50K 丝束短切碳纤维和亚什兰内部改性的乙烯基酯树脂,麦格纳配制了EpicBlend SMC。
这种乙烯基酯树脂对碳纤维具有很好的粘接力并能很好地润湿它。
这将被用于局部增强并与按0°/90°铺放的6层NCF SMC 共模塑成型。
该NCF SMC也由麦格纳制成,它采用了同样的乙烯基酯树脂和卓尔泰克(Zoltek)提供的NCF织物,成型前被裁切成小的补片。
对短纤维SMC和长纤维SMC的组合使用是设计的关键,但也是真正的挑战。
短纤维SMC可实现复杂形状的成型以及对钢嵌件的包覆成型,以用于发动机和转向支架,而NCF补片能够承受发动机和下控制臂固定处的高负荷。
与冲压钢副车架相比,这两种SMC材料的组合使用减轻了9.3 kg的重量。
“开发这种用于共模塑的0°/90°SMC 补片花费了不少功夫。”Krull回忆说,并指出了在成型过程中实现这种短切纤维SMC的流动以确保无干点或者无其他质量问题地集成NCF补片所需要注意的问题。
螺栓连接
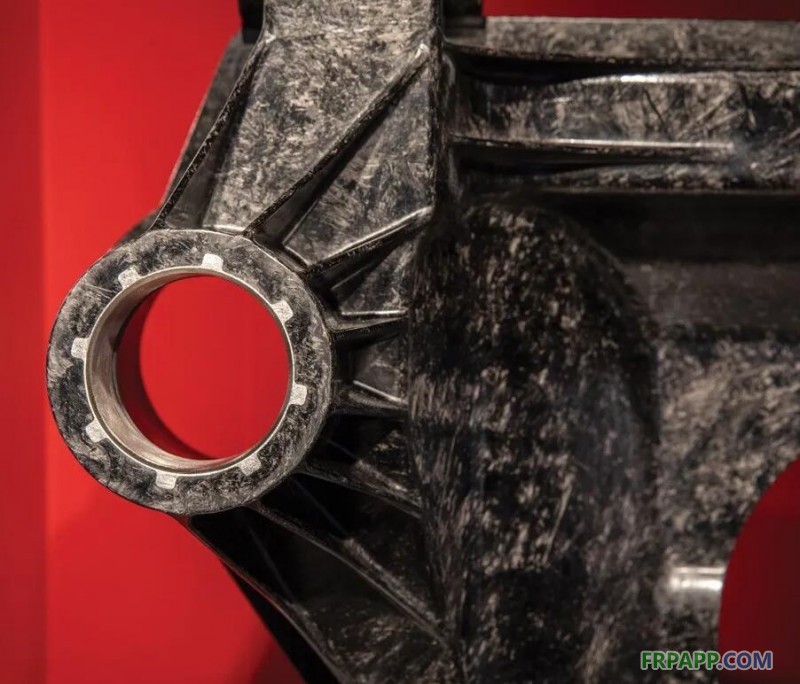
将不锈钢套筒包覆成型到SMC副车架中,实现了4个车身安装连接和两个转向支座连接(图片来自麦格纳国际)
螺栓连接也是一个问题。“在用螺栓将控制臂和转向器固定到副车架上的地方,复合材料承受的点载荷很高,达到80~100kN。”Wagner说。在4个车身安装连接和两个转向支架连接的地方,需要将不锈钢套筒包覆成型到复合材料部件中。“为了固定,要将每个车身安装衬套压入套筒中以实现过盈配合。”Krull解释道,“应力通过套筒圆周被带入成型部件中。我们观察了插入衬套时的力,并将这些输入计算机设计模型中。我们还在力学试验中寻找复合材料中产生的裂缝,但什么也没看到。”
Wagner介绍说,使用的螺栓很大,通常是M12和更大的,而且必须拥有紧的位置公差、直径公差和角度公差。一旦成型并装配好副车架,就需要进行必要的后加工。
测试与团队合作
2018年,原型副车架得到了测试。
福特完成了部件级别和整车级别的一系列腐蚀性测试,以探索各种缓蚀措施。部件和整车级别的耐久性试验包括石击试验、螺栓载荷保持试验和高温循环试验。对部件的试验包括高周疲劳试验、接头过载试验、振动和安全试验。
“我们自己测试了原型副车架。”Krull说,“这是由SMC 制成的非常大而复杂的部件,由共模塑成型工艺制成。为了了解我们还有可能在哪里使用这些材料,我们正在研究如何改变设计、成型中的SMC流动以及纤维排列。”
“我们想要了解这类大量使用CFRP的部件的成本动因是什么。”Wagner说,“二次加工是最重要的成本之一。我们需要更富有创造性的思考,以消除部件成型后的加工。”他还表示,最大的挑战之一是为设计而开发成型部件的绝对材料特性。“我们花费大量时间对材料进行表征以用于设计分析。”他解释说。
Cordoba说,最大的成就是团队合作。“不仅与我们的客户福特之间的合作,还包括全球团队的合作。”
Wagner赞同说:“这是我们如何推动我们的供应商和我们自己去使用先进的轻量化材料的最好例子。”