
Hutchinson的复合材料前轴悬架叶片示意图
作为材料配方公司以及面向汽车、轨道交通和航空工业的振动控制技术制造商,Hutchinson利用其经验设计了208 FE的车轴。Hutchinson将这些轴的结构复合材料核心称为是一种“多功能的悬架叶片”,因为其设计特点是:在一个部件中整合了4种重要功能——悬架、转向、抗振动/噪声以及防侧倾。在开发过程中,设计工程师们整合/消除了12个部件,包括:弹簧、弹簧座、防侧倾杆、防侧倾杆配件、防侧倾杆的连接杆以及叉臂(转向部分)元件等。
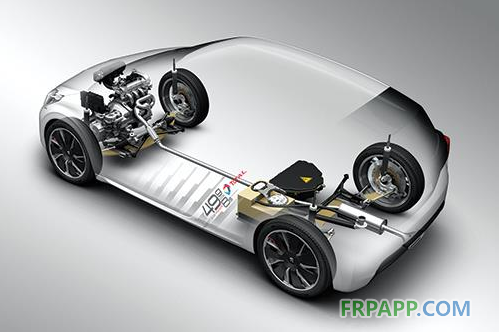
标致208 FE, 一款混合动力概念汽车, 配备了采用大约50%单向环氧/玻璃纤维制成的前、后轴(图片来自标致汽车公司)
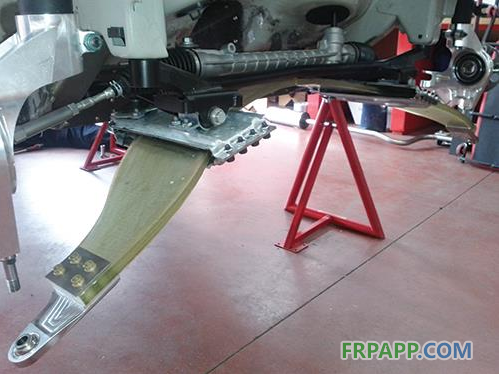
相比金属悬架,该复合材料的叶片设计降低了20.4 kg(约40%)的重量。在加工中,设计工程师们能够整合或消除12个部件(图片来自标致汽车公司)
这一全新的悬架实际上起源于Hutchinson在20年前为另一家欧洲汽车制造商生产的一个部件。Hutchinson复合材料技术中心(简称“CTeC”)的技术总监Bertrand Florentz回忆说,当时该部件已准备投入生产,但由于对传统的钢悬架的偏好,这一生产计划最终被取消。随着2020更严厉的排放标准即将落实,未达标的企业将面临处罚,从而使今天的汽车制造商们正面临着市场形势的巨大变化。与此同时,Hutchinson早期所积累的悬架应用经验,也使其快速地响应了标致208 FE新的、设计独特的发展要求。
在设计汽车悬架时,首先考虑的是,这一部件总成需要承受静载荷(汽车的固定重量)和动载荷(运行时产生),相当于分布到所有3个空间轴上的拉伸力、压缩力和剪切力,即纵向的、垂直的和横向的载荷。驾驶时,其承受的动载荷可以达到汽车静载荷的5倍大,因此,在该部件的关键结构尺寸和总体设计中,动载荷是重要的考虑因素。
针对这些多轴向载荷问题,Hutchinson初期的“宏伟”设计方案是,采用一种梁分布均匀的正交异性模型去模拟主悬架结构。这种梁正交异性模型作为一个底线,允许工程师们针对局部必要的刚性特征,来满足汽车基本的静载荷要求。
如果材料的力学性能和热性能在3个相互垂直的方向上是唯一而独立的,则属于正交各向异性材料。相比之下,各向同性材料的各种性能在所有的方向上都是相同的。此外,一种材料可以拥有同质的(均匀的)或非同质的(不均匀的)微结构。一种材料,如轧钢,是天然的正交各向异性和同质性(均匀性)。设计一种同质的正交各向异性的复合材料,关键是采用同样的“微结构”(即材料,在此是一种环氧树脂)和大多数的单向玻璃纤维、按改变厚度和方向的一种层合构成方式,构建一种层压结构。这样的一种结构将允许设计工程师们在采用有限元分析(FEA)对部件建模后,通过增加或减少特定区域的增强材料,来处理好3个独立轴中的各种变形和载荷问题。
因此,设计过程的第二步是在Hutchinson的研究中心对该悬架进行详细的有限元模拟。在此所做的模拟被用于模仿复合材料叶片的刚性,并提供详细的层合结构,包括织物的取向和局部厚度。结果,获得了一种拥有3个层合结构的叶片设计:层合结构一,在叶片的每一端,球接头在此与柱子(较厚,同时更加特别的是,凭借高度的纵向刚度而确保了轮导向)相接 ;层合结构二,是与安装在橡胶上的钢轴支架相连接的两面的中间部分;层合结构三,支架(较薄,而且尤为特别的是,确保了悬架的垂直刚度)之间的中间部分。
在有限元仿真中考虑的载荷类型是垂直载荷(对称的和不对称的)、纵向载荷、横向载荷、转角载荷、侧面冲击载荷和疲劳载荷。仿真输出的是所有方向上叶片的刚度、位移和运动学,以及树脂和纤维的局部应力和应变。然后将应力和应变与实验室获得的材料许用值相比较,包括必要的“材料失效”因素。
在一个并行开发过程中,研究人员采用层压试样和纯树脂对材料进行了综合表征。具体到材料和部件生产(如树脂传递模塑成型(RTM))的工艺参数、总的反应热、热膨胀和热收缩(在所有的3个轴方向)以及纤维集中度等,由通过差示扫描量热法(DSC)、接触角测量法和动态力学分析法(DMA)获得的测量值计算而出。这些数据被用于生成一个悬架叶片的黏弹性模型,然后将其导入到ABAQUS 有限元分析软件中(Dassault Systèmes,美国马萨诸塞州沃尔瑟姆)。热力学分析被用于确定成型过程中加热的“热点”,以及计算并预测在固化循环期间由加工引起的变形和残余应力,目的是当部件设计完成后优化加工条件,同时确保部件在正常生产的模具和设备上得到连续成型。
尽管Hutchinson为标致208 FE 设计了复合材料的前、后轴,但由于增加了转向元素而使前轴更为复杂。最终的悬架设计由一个弓形主结构的玻璃纤维增强叶片构成,其厚度范围在12~15 mm之间,纤维的体积含量超过50%。该叶片长约1.2m,名义宽度140mm,弓深大约315mm。在消除上述所有部件的过程中,该复合材料的轴/悬架设计整合了传统金属悬架的所有功能,如:该弓形的悬架叶片在组装过程中按其预压的形状被安装到汽车上,并横跨汽车前端宽度而作为一个单一的弹簧用于吸收路振。该复合材料叶片的每一面都由一对橡胶铰接(一个垂直的,一个纵向的)而与汽车的白车身(BIW)相连。当叶片为应对路振而发生弯曲或压缩时,在两对固定之间的横向轴中被拉长。为适应这种横向延伸,橡胶底座提供了必要的横向位移弹性,同时它们还可对路振和噪声进行额外的过滤。这些铰接被集成到一对包封了叶片每一面的钢底壳中。
每个叶尖与钢球关节相连。这些球关节转而与连接杆(拉杆)相连,这些连接杆通过吸振器而被装到汽车上。在这些连接点上,叶片承受最大的负载力,因此,在叶片设计中,对这一区域做了额外增强。通过取代防倾杆,该叶片本身就兼具了防侧倾的功能,这是由其固有的弯曲刚性和固定的对称性实现的。实际上,基于变形的对称性,当左轮向上移动时,右轮也向上移动,这实际上是一个防倾连接的定义。转向是传统的而且与叶片分离,一个连接车轮的转向架通过左、右连接杆而直接转动。
Florentz说,设计并制造一个复合材料的轴/悬架,在工程上付出的努力至少是设计同样的金属部件的5倍。但就某种意义而言,花费额外的时间是必要的,因为钢作为一种传统材料而拥有大量的测试数据和合格数据,但对于复合材料部件而言,材料的最终表征必须在经历逐层老化、模拟和后处理后而获得。假设在类似的应用中使用复合材料,可以确信的是,由于材料的认证、测试和模拟工作从一个项目传递给了另一个项目,因此大多数额外的工程开发时间可以消除。
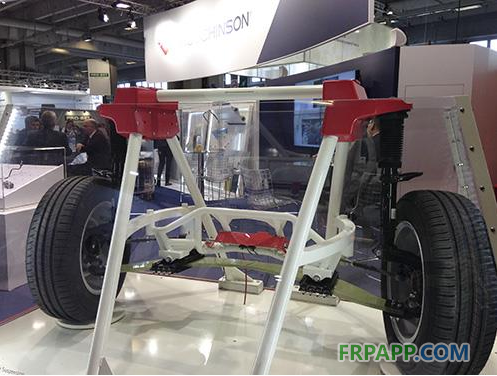
在于法国巴黎举行的JEC 2015展会中,该悬架叶片是Hutchinson公司展位的亮点

JEC 2015展会中,参观者们能够在展出的悬架系统上清晰地看到该悬架设计是如何将弹簧叶片结构从前悬架的转向功能中分离出来
虽然这项技术仍被认为是概念性的,但这项应用却值得关注且具有潜力。长期以来,复合材料一直被认为不适合商业化汽车的结构应用,为此,复合材料行业做了许多艰难的努力,来证明复合材料替代金属的潜力。凭借Hutchinson公司在此方面迈出的重要一步,相信汽车制造商和消费者们可以做出自己的判断。