RTM是在低压下成型,模具刚度相对要求低,可以使用多种材料来制造模具。常用的模具类型有玻璃钢模具,电铸镍模具、铝模具、铸铁模具和钢模。表6-8列出了各种类型模具的比较。
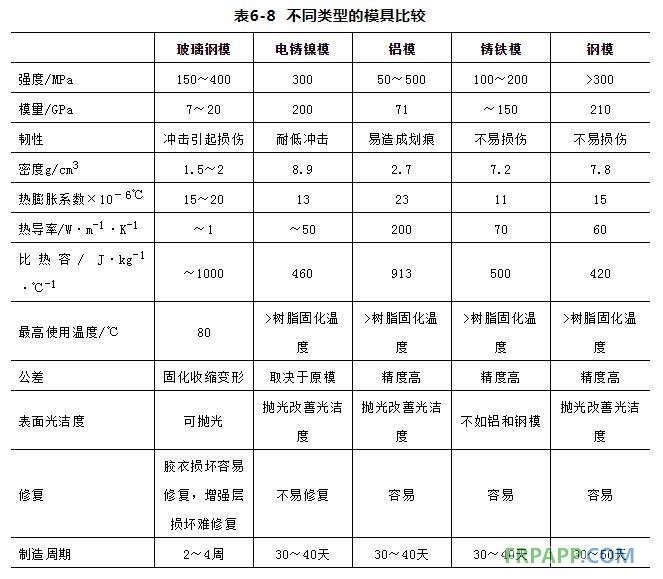
2.模具结构设计
RTM模具的结构设计包括产品结构分型;嵌模、组合模、预埋结构、夹芯结构等模具结构形式;专用锁紧机构、脱模机构、专用密封结构;真空结构形式;模具层合结构、刚度结构形式、模具加热形式等。
模具结构设计主要遵循以下原则:
(1)尽量简化脱模部件:在制造模具时应考虑产品脱模,覆盖件两边缘要留有一定的脱模角度,各部分的连接处平滑过渡。
(2)尽量方便浇注系统的布置。
(3)便于气体排除:为了有利于气体的排出,分型面尽可能与树脂流动的末端重合。
(4)模具密封和真空辅助成型:模具采用双密封结构并且利用真空在浸渍前对模腔抽真空,这样有利于降低模具变形、降低孔隙率、提高生产效率、减少修整工序。
(5)便于活块的安放:当分型面开启后,要有一定的空间便于活块的安放,并保证活块安放稳固,覆盖件模具的活块采用真空吸附,利于定位和稳固。
(6)模具制造的难易性:模具总体结构简化,尽量减少分型面的数目,采用平直分型面。
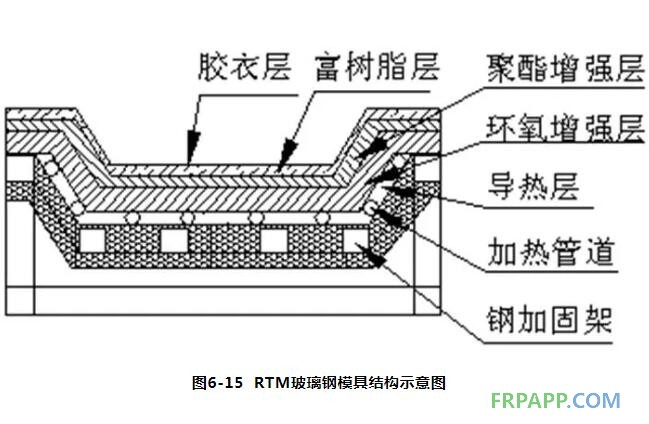
3.注射口和排气口的设计
注射口在模具上有三种情况:
(1)、中心位置:注射口选择在产品的几何形心,保证树脂在模腔中的流动距离最短。
(2)、边缘位置:注射口设计在模具的一端,同时在模具上设有分配流道,树脂从边缘流道注射,排气口对称地设计在模具另一端。
(3)、外围周边:树脂通过外围周边分配流道注射,排气口选择在中心或中心附近的位置。虽然外围周边注射的流道也在边缘,但它是闭合的,排气口在模具的中心处。
无论怎样选择注射口的位置,目的都是保证树脂能够流动均匀,浸透纤维。在模具上设有多个注射口可以提高注射效率,但是要保证不同注射口在流动边缘到达下一注射口时,该注射口能够及时开启,上一注射口及时关闭,避免出现断流或紊流造成的流动死角。
排气口通常设计在模具的最高点和充模流动的末端,以利于空气的排出和纤维的充份浸润。借助流动流动模拟软件可以比较好地确定理想的注口和排气口。
4.模具密封结构
模具的密封通常采用不同结构形式的密封条来实现,所用到的密封条结构有O型、矩形和异型密封条,材质使用硅橡胶比较好。为了保证模具的有效密封和模腔内抽真空的需要,经常会用到双密封结构。
5.RTM模具的加热方法
在RTM工艺中对模内树脂的加热方法有两大类:一是直接加热法。如美国RP/CMachinery 公司将射频电能直接通到型腔内的树脂中使树脂固化,该方法较先进,热效率最高,但难度大,目前还不成熟;二是间接加热法:热能由介质(气、水、油、蒸汽)携带,经模具背衬、型壳、型面传导到树脂中,使树脂固化。间接加热法分为三种。
(1)背衬管路法。模具背衬里铺设热介质的管路(循环管路),由于管路离型面有一定距离,而复合材料属热的不良导体,热传导较困难,因此加热速度慢,加热循环较长。应用此方法要求改善模具材料的导热性,且选择较平坦的产品类型,以便铺设管路方便易施。
(2)型壳管路(或电热丝布)法。型壳里贴近型面铺设热介质循环管路 (或电热丝布)、热介质流的控制与压机、模具周边夹紧的操作相协调。1个供热系统可同时供多个模具,加热、冷却的速度最快,但每个模具的成本最高。
(3) 整模加热法,物料充模后,将整个模具置于固化炉(或高压釜)内加热,热能经过模具传导到型腔内的树脂,致使树脂固化, 要求模具材料的导热性好,固化炉内能容纳整个模具,如果固化炉尺寸较大,可同时加热多个模具,本法加热效率低、固化周期长。
另外美国Sterling Heights公司研制高速RTM工艺,采用钢模具、模内有管路、管内通140℃左右的蒸汽,45秒树脂固化、再配以其他“高速技术”,如预混合、预催化、特殊单一树脂、快速投料、快速注射等,模塑周期约1分钟。
6.玻璃钢RTM模具的制造
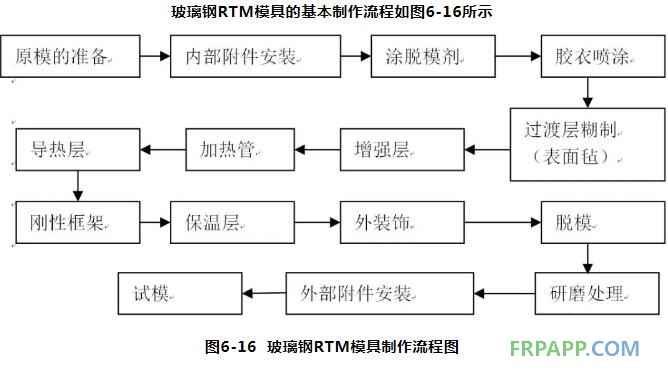
原模的准备工作中最重要的一项是检验工作。复合材料的成型是不可逆的,所以每做一工序都需要检验验证其正确合格方可进行下一道工序的施工,这也是保证模具制作出现问题时及时调整,把损失降到最低的最有效的方法。
内部附件包括注入口嵌件,排气口嵌件,密封条,辅助模内顶出件,模内导向定位件以及产品预埋件定位机构等等。
胶衣层是保证模具表面的基础,厚度宜在0.5~1.0mm,可分2~3次喷涂,固化时间以手触判断,触觉粘而指尖未带有胶衣为宜。过渡层可用30-50g/m2表面毡糊制,糊制过程中保证不能有气泡存在,固化后开始糊制增强层,糊制过程中最主要控制铺层的均匀程度及含胶量均匀程度。
对于形状简单、面积较大平板类型的模具,可以在增强层采用毡布交替的铺层设计方式,此方法可以进一步提高板壳强度,而曲面较多,形状复杂的模具直接由短切毡铺层糊制即可。但根据不同的模具质量要求慎重选择布类增强,因其强度和含量存在方向性,容易导致模具出现因收缩不均而引起的翅曲变形。
另外,根据不同的树脂体系和不同的模具要求及糊制制度进行操作,一般情况下,每固化一次糊制的层数越少,模具尺寸精确度较高,模具强度低,模具变形机率较小;相反每固化一次糊制的层数越多,整体强度较大,收缩变形机率也较大。
有加热层设计的模具,增强层的制作厚度应为6~8mm,既保证表面强度,其隔热作作也不至过于突出。加热层由加热管路和导热介质构成,加热管路采用铜管制成,并贴附于增强层的表面,先局部固定后,再用导热材料浇铸成型。
模具的加固要使用金属等刚性材料,按板壳理论设计结果确定平板单元区域大小并进行网格式加固,框架焊接完成后必须进行去应力处理,糊在模具背后使其与模具粘接成为一体。有加热层的模具还要在最后制作保温层,根据保温材料的不同,保温层厚度一般为50~100mm,浇铸成型。