一、成型温度
在拉挤成型过程中,材料在穿越模具时发生的变化是最关键的,也是研究拉挤工艺的重点。直到目前为止,虽然有许多研究方法,如数学模型的应用、计算机的模拟,和可供利用的工具如压力传感器等等,但是至今研究者们依然不明白模具中到底发生了什么,只是依据实验及理论研究提出了一系列的推测与假设。
一般来讲,认为玻璃纤维浸胶后通过加热的金属模具,按其在模具中的不同状态,把模具分为三部分,如图所示。
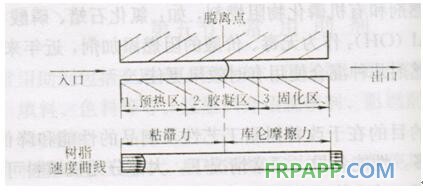
图9-47 拉挤模具内树脂的速度曲线和不同区域的粘滞力和摩擦力示意图
图9-47表示了材料穿过模具时的主要特征。尽管增强材料必须以同样的速度穿过模具,但在某些区域内,树脂和纤维有相对流动。图中绘出了模具入口和出口附近区域的树脂速度分布图,在模具入口区,树脂的行为像牛顿流体,壁面速度的边界条件意味着为零。离模具壁面一小段距离处,树脂的流动速度增加到与增强材料相当的水平。在模具内壁表面上,树脂产生粘滞阻力。
在三段式模具中,人为的把这一连续拉挤过程分为预热区、胶凝区和固化区。在模具上使用3对加热板来加热,并用计算机来控制温度。脱离点是指树脂脱离模具的点。树脂在加热过程中,温度逐渐升高,粘度降低。通过预热区后,树脂体系开始胶凝、固化,这时产品和模具界面处的粘滞阻力增加,壁面上零速度的边界条件被打破,在脱离点处树脂出现速度突变,树脂和增强材料一起以相同的速度均匀移动,在固化区内产品受热继续固化,以保证出模时有足够的固化度。
1.温度的确定
模具的加热条件是根据树脂体系来确定的。以聚酯树脂配方为例,首先对树脂体系进行差动扫描式热量计(DSC)动态扫描,得到放热峰曲线。一般来讲,模具温度应大于树脂的放热峰值,温度上限为树脂的降解温度。同时作树脂的胶凝实验,温度、胶凝时间、拉速应当匹配。预热区温度可以较低,胶凝区与固化区温度相似。温度分布应使产品固化放热峰出现在模具中部靠后,胶凝固化分离点应控制在模具中部。一般三段温差控制在20~30℃左右,温度梯度不宜过大。
2. 最佳模具温度分布及分析
以前分析拉挤型材内热能传递和型材固化时都是假定模具温度是已知的。其实一个完整、科学的拉挤工艺模型必须包括型材内的和模具内的热能传递。浸渍树脂的纤维一旦进入模具里,它的热量就从模具壁上向型材内传递,贴近模具的树脂比型材中心的树脂先被加热,产生胶凝;固化后,反应放热会引起中心温度高于模具壁的温度。固化后由于体积收缩,树脂会因收缩而脱离模具壁。在几个假定条件下,对型材内热能传递建立模型,有关学者对此做了深入的研究。因为拉挤模具为金属模,为良导热体,模具的热能在模具的纵向和横向上都会损失。建立模具温度模型有助于我们了解模具温度分布规律。
加热器的配置对型芯内的温度和模具温度影响很大。一般在某些约定条件下,固化峰的位置随加热器的移动而移动,而加热带与型芯温度峰值处的距离基本不变。这种放热位置的移动是正常的,来自加热器的热通量是有限的,并且在这些条件下,固化是受加热器控制的,当热能传递受“动力学”控制时,受线速度和预热温度的制约,型芯内温度峰值对加热器的位置并不敏感。
在模具周围保温和降低空气的热能传递系数的影响是相同的。当热传递系数降低时,模具后半部分温度升高,整个模具的热量分布更均匀。因为大多数树脂固化发生在靠近加热器的位置,保温对型芯温度的影响较小,当放热峰远离加热带时,模具最好选择保温。
利用模具温度模型对拉挤工艺进行分析,由计算机辅助设计拉挤工艺参数,是当前既合理又简便、高效的设计工具。
二、拉挤速度的确定
拉挤模具的长度一般为0.6~1.2m由树脂体系的固化放热曲线确定模具温度,该温度还必须充分考虑使产品在模具中部胶凝固脂,也即脱离点在中部并尽量靠前。如果拉挤速度过快、制品固化不良或者不能固化,直接影响到产品质量,产品表层会有稠状、富树脂层;如果拉挤速度过慢,型材在模中停留时间过长,制品固化过度,并且影响降低生产效率。
一般的实验拉挤速度为300mm/min左右。拉挤工艺开始时,速度应放慢、然后渐提高到正常拉挤速度。一般拉挤速度在300~500mm/min,现代拉挤技术的发展方向之一就是高速化,目前最快的拉挤速度可达15m/min。
三、牵引力
牵引力是保证制品顺利出模的关键,牵引力的大小由产品与模具之间的界面上的剪切应力来确定。通过测量浸渍树脂的增强纤维被牵引穿过模具的一段短距离的牵引力就可测量上述界面上的剪切应力,并绘出其特性曲线。
图9-48表示了三种不同牵引速度通过模具时平均剪切应力的变化。这些结果虽然不是十分精确,但是作为定性的分析已经足够了。
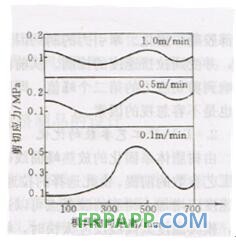
图9-48 牵引速度与剪切应力
从图9-48中可以看到在模具中剪切力曲线是随拉速的变化而变化的。暂时忽略拉速的影响,可以发现在模具不同位置,剪切力是不同的。整个模具中曲线出现3个峰,下面分别加以讨论。
模具入口处的剪切应力峰,此峰值与模具壁附近树脂的粘滞阻力相一致。通过升温,在模具预热区内,树脂粘度随温度升高而降低,剪切应力也开始下降。初始峰值的变化由树脂粘性流体的性质决定。另外,填料含量和模具入口温度也对初始剪切力影响很大。
由于树脂固化反应,它的粘度增加而产生第2个剪切应力峰。该值对应于树脂与模具壁面的脱离点,并与拉速关系很大,当牵引速度增加时,这个点的剪应力大大减小。
最后,第三区域也即模具出口处,出现连续的剪切应力,这是由于产品在固化区中与模具壁摩擦引起的,这个摩擦力较小。
牵引力在工艺控制中很重要。成型中若想使制品表面光洁,要求产品在脱离点的剪切应力较小,并且尽早脱离模具。牵引力的变化反映了产品在模具中的反应状态,它与许多因素,如:纤维含量、制品的几何形状与尺寸、脱模剂、温度、拉速等有关系。
四、各拉挤工艺变量的相关性
1. 热参数、拉挤速度、牵引力三者的关系
热参数、拉速、牵引力三个工艺参数中,热参数是由树脂系统的特性来确定的,是拉挤工艺中应当解决的首要因素。通过树脂固化体系的DSC曲线的峰值和有关条件,确定模具加热的各段温度值。拉挤速度确定的原则是在给定的模内温度下的胶凝时间,保证制品在模具中部胶凝、固化。牵引力的制约因素较多,如:它与模具温度关系很大,并受到拉挤速度的控制。从前面的分析可看到:拉速的增加直接影响到剪切应力的第二个峰值,即脱离点处的剪切应力;脱模剂的影响也是不容忽视的因素。
2. T-V-F工艺参数的优化
由树脂体系固化的放热峰曲线确定的模具温度分布是我们确定其他工艺参数的前提。由此选择的拉速必须与温度匹配,模具温度高,牵引速度应增加。树脂的胶凝点可以通过调整模具温度和牵引速度来确定,模具温度太高或反应太快时,将引起产品热开裂。因此,利用分区加热模具,把加热区分为预热区、胶凝区和固化反应区可以优化拉挤工艺,减少产品热开裂。
为了提高生产效率,一般尽可能提高拉速。这样可提高模具剪切应力,以及制品表面质量。对于较厚的制品,应选择较低拉速或使用较长的模具,增加模具温度,其目的在于使产品能较好地固化,从而提高制品的性能。
为了降低牵引力,使产品顺利脱模,采用良好的脱模剂是十分必要的,有时这在成型工艺中起到决定性的作用。
五、树脂预热与制品后固化
树脂进入模具前进行预热对工艺是非常有益。这样可能降低树脂固化反应温度,使产品表面优良。射频(RF)预热效果很好。预热使树脂温度提高,粘度下降,增加了纤维的浸润效果,并且为提高拉速创造了条件。许多树脂系统中,如环氧树脂等,都需要预热。
预热的效果还表现在使浸胶的纤维束内外温度梯度减小。因为在进入模具后,由模具传递给产品的热量从产品表面到产品中心部分呈梯状分布,产品中心线的温度低于产品表面的温度。同理,产品中心的固化滞后于产品表面的固化。如果提高拉挤速度,那么制品中心线和表面之间的温度和固化度的滞后量都会增加。接着,该滞后量又会相反地随着固化放热的增加而减小,最后甚至制品的中心温度高于表面温度。要想实现产品内外均匀固化,减少热应力,树脂应该预热。
制品出模后的固化度达不到要求时需进行后固化处理。一般来讲,制品出模后在空气中自然冷却。在这段过程中,固化反应继续进行。一般的后固化处理是:将切割好的制品放到恒温箱中搁置一段时间,使制品达到所要求的固化度。
关注本公众号
微信号:cnfrtp
技术·产品·会展·宣传