HP-RTM(High Pressure Resin Transfer Molding)是高压树脂传递模塑成型工艺的简称。它是指利用高压压力将树脂对冲混合并注入到预先铺设有纤维增强材料和预置嵌件的真空密闭模具内,经树脂流动充模、浸渍、固化和脱模,获得复合材料制品的成型工艺。工艺过程如图1所示:
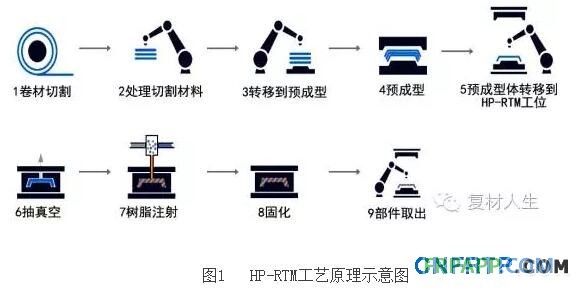
2、 HP-RTM工艺衍变过程
RTM(Resin Transfer Molding)工艺最早起源于1940年的MARCO法。Macro法相当简单,对模腔抽真空以驱动树脂浸渍过程,美国海军承包商用这种方法开发出了大型玻璃钢增强塑料船体。在20世纪50年代称为RTM工艺,该工艺可以生产双面光滑的产品,树脂的注射压力适中,比手糊工艺优越,所以得到了发展。20世纪50年代至70年代,由于最初的RTM虽然成本低但技术要求高,特别是对原材料及模具要求高,所以发展缓慢。直到1985年,以缩短成型周期、提高表面平滑性和质量稳定性为目标的第二代RTM加工法得以公开,才使得RTM不论是在原材料方面还是制品强度等各方面都有明显的优势。90年代RTM成型工艺及其理论研究达到高潮,欧美很多公司投入巨资用于开发RTM工艺,还开设专科学校培训RTM专业人才。进入21世纪,随着我国化学工业和机械制造水平的提升,以及市场应用技术水平的提升,我国复合材料的RTM工艺技术也迎来了全新的发展期,不仅在技术水平上,而且在生产规模、自动化程度上都取得了巨大的进步。
相比较而言,RTM工艺技术优势明显,其特点主要体现在:模具制造和材料选择灵活性强;能制造具有良好表面质量,尺寸精度高的部件特别是大型部件;易实现局部增强,嵌入件可以预先安置;纤维含量最高可达60%,在树脂中可以加入填料,以降低成本改善性能;闭模成型,苯乙烯排放量少,有利于环境保护;低压注射,一般≤0.4MPa,可用玻璃钢模、铝模等,模具成本较低;制品孔隙率较低,一般小于1%。局限性:适合一定批量的产品,经济规模产品在500~2000件;模具的设计和制造有一定的难度;树脂流动和浸渍控制困难,导致工艺复杂性和不可控性增大。
复合材料RTM成型工艺技术相比较其它成型工艺有明显的高性能和低成本优势,尤其是面对当前高速发展的潜力巨大的汽车复合材料市场需求,如何改进复合材料成型技术以便更好地适应市场需求,成为研究者所关注的焦点之一。国内外研究者也开展了大量颇有成效的研究,使得RTM技术更趋成熟,并形成一个完整的材料、工艺和理论体系。并在RTM工艺技术的技术上开发了一系列新的RTM成型技术。主要有:VARTM(Vacuum Assisted Resin Transfer Molding)、Light-RTM(Light-Resin Transfer Molding)、SCRIMP(Seemann Composites Resin Infusion Manufacturing Process)、MI-RTM(Multiple Insert Tooling Resin Transfer Molding)、HP-RTM(High Pressure Resin Transfer Molding)、HP-CRTM(High Pressure Compression Resin Transfer Molding)等。
与常规的RTM工艺相比,VARTM工艺技术以真空压力作为动力,采用单面刚性模具和真空袋复合构成制件的模腔,使模具更加轻便;真空的作用有助于树脂对纤维的浸渍,使纤维浸渍更充分;同时真空还起到排除纤维束内的空气的作用,从而减少了微观空隙的形成,得到空隙率更低的制品;真空的作用使制品纤维含量更高,生产的构件机械性能更好。
Light-RTM工艺在VARTM工艺技术的基础上,采用半刚性模具和刚性模具配合构成制件型腔,并采用真空密封技术,成型模具的可以反复使用,大大降低了模具成本及制件制造成本;同时采用类环形通道从模具四周注胶,以及收集杯集料技术,大改善了树脂的流动充模,提高了生产效率。
SCRIMP工艺则采用精心设置的树脂分配系统,使树脂胶液先迅速在长度方向上充分流动填充,然后在真空压力下在厚度方向缓慢浸润,大大改善了浸渍效果,减少了缺陷发生,使模塑部件具有很好的一致性和重复性。而且也克服了VARTM在生产大型平面、曲面的层合结构以及加筋异型构件等制品时,纤维浸渍速度慢、成形周期长等不足。尤其是在大型制品生产领域,该技术具有得天独厚的技术优势。
MI-RTM工艺技术由多个托入式衬模和衬模模腔支撑系统构成。主要是将传统RTM工艺中原本集中在模腔中完成的多项工序进行分解并移出模腔外来完成,这样大幅度减少了成型时间并充分地利用了RTM装备的功效,从而降低了模具制造成本,为大批量制造RTM制品提供了低风险、低造价的方法。近几年出现的多工位中高压RTM成型工艺技术也是基于这一理念,在成型周期相对耗时纤维铺层环节,设置多个纤维铺设工位,并依次或交替与单一固定模配合注射成型制品,大幅缩短纤维铺设时间,提高生产效率和设备利用率,已经降低了制件成本。
HP-RTM是近年来推出的一种应对大批量生产高性能热固性复合材料零件的新型RTM工艺技术。它采用预成型件、钢模,真空辅助排气,高压混合注射和在高压下完成树脂对纤维的浸渍和固化的工艺,实现低成本、短周期(大批量)、高质量生产。 相比较传统RTM,HP-RTM工艺具有以下几个优点:第一,充模快、浸润效果好,显著减少了气泡,降低了孔隙率;第二,使用高活性树脂,缩短了生产周期,工艺稳定性和可重复性高;第三,使用内脱模剂和自清洁系统,制件表面效果优秀,厚度和形状偏差小。可实现低成本、短周期(大批量)、高质量生产。
HP-CRTM工艺技术则是在HP-RTM工艺技术的树脂注胶前,增大了密封模腔间隙,使树脂注入通道增加,注胶结束后再将模具在高压下完全闭合,树脂体系随闭合压力流动充模,成型压力相对较低,避免了纤维的冲动,提高了树脂的渗透率与流动距离,提高了纤维的浸渍速度,有效避免了干纤维的产生,缩短了制件成型周期。
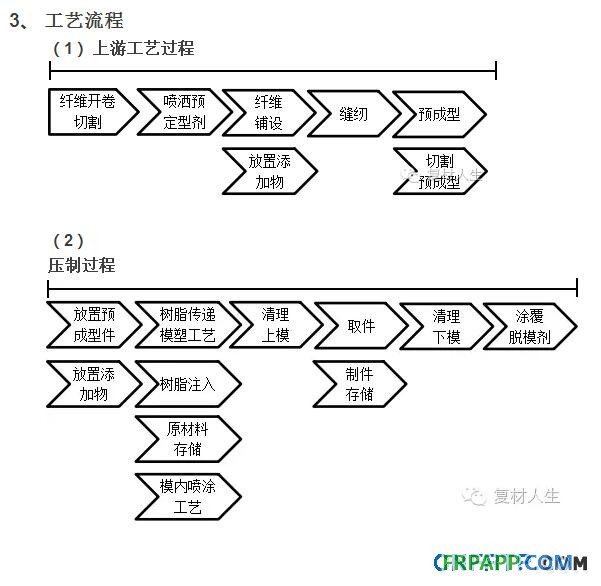
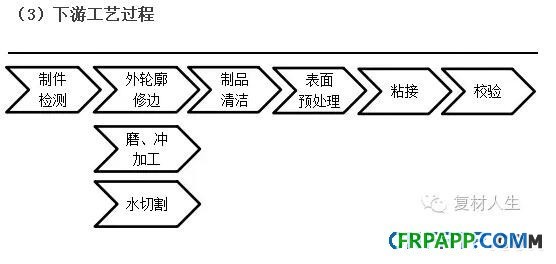
4、工艺过程解析
以德国迪芬巴赫公司(Dieffenbacher)和克劳斯玛菲公司(KraussMaffei)共同开发的高压树脂传递模塑成型工艺(HP-RTM)自动化生产线(如图2所示)为实例介绍HP-RTM工艺技术。具体过程如下:
由图2的HP-RTM自动化生产线可知,HP-RTM自动化生产线主要由预成型体加工中心、预成型体处理、RTM注射系统、计量控制系统、制件机加工中心等构成。纤维预成型加工中心如图3所示。
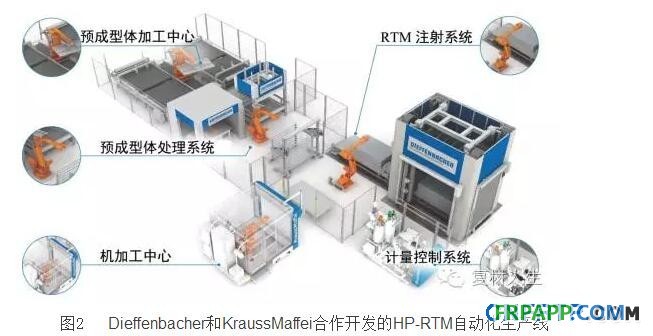
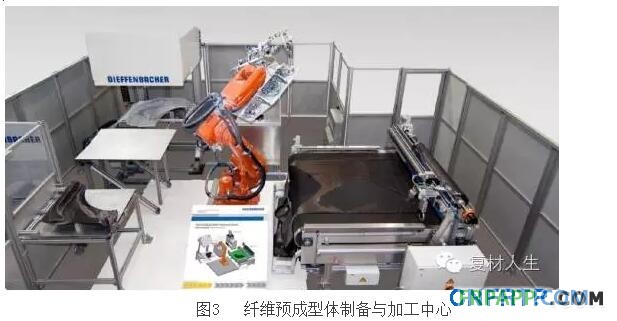
(1)上游工艺过程
① 纤维开卷切割
首先将碳纤维织物的卷筒固定在自动裁剪机的旋转轴上,并将预成型裁剪图样输入自动裁剪,并对裁剪图样进行优化排列;展开碳纤维织物卷筒,开动裁剪机,进行预成型体铺层图样的自动裁剪,如图4所示。并利用机械臂的吸盘将裁剪后的纤维铺层吸起,并转移到下一工序设备上,如图5、6所示。
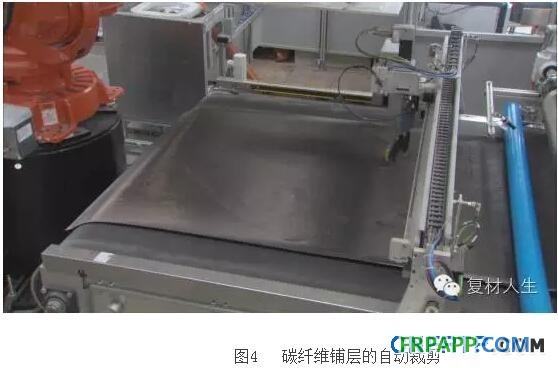
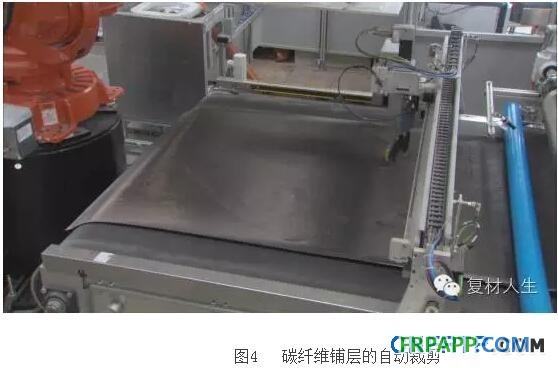
图5 机械臂吸附并转移裁剪纤维织物
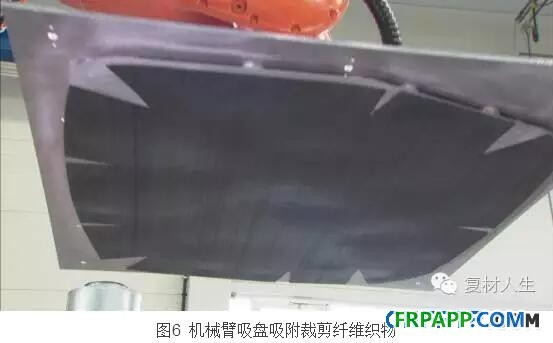
②喷洒预定型剂
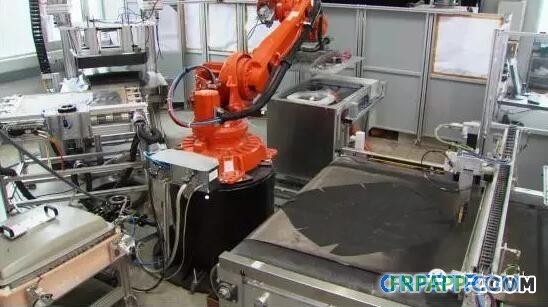
图7纤维织物预定型剂的喷涂
将裁剪所得的纤维织物转移到预定型剂喷涂设备,开动喷涂设备将预定型粘接剂均匀喷涂在纤维织物表面,喷涂时需移动纤维织物,以便预定型剂均匀喷涂在纤维织物表面,如图7所示。
③纤维层定位与叠合
将涂覆有纤维预定型剂的碳纤维织物转移到织物叠合设备,并按所设计的制件纤维铺层结构将纤维织物依次进行定位、叠合,并平铺在织物铺叠输送带上。如图8所示。
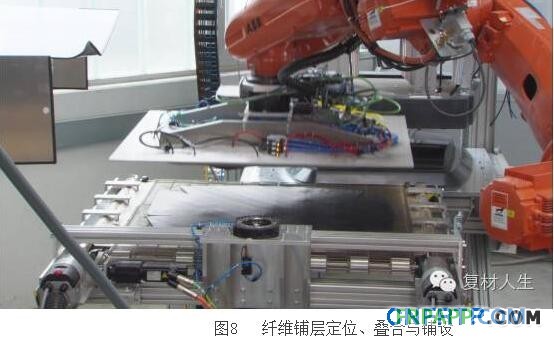
④ 纤维铺设
利用织物叠合输送设备将叠合好的纤维织物转移到纤维预成型设备上,如图9所示;纤维织物转移时,需精确控制输送带的移到速度和位置,防止纤维织物铺放过程中发生移动或错位,影响制件性能。
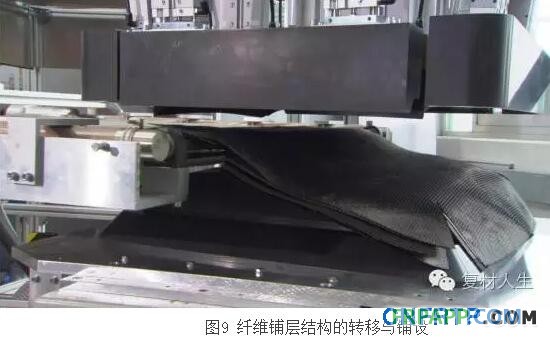
⑤纤维织物预定型
将纤维织物铺层均匀铺入预成型模具中,首先将预成型体中心的加压压头下压,压紧纤维铺层结构,并将预成型模具的加压压头由中心向外辐射顺序下压,下压时尽可能的减少纤维的皱缩,以影响制品性能。如图10 所示。在预成型模具的热、压作用下,使纤维预成型体定型。
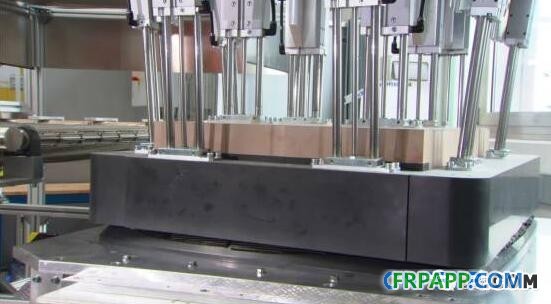
图10 纤维预成型体的热压预定型
⑥ 预成型体的剪裁
将经过预热预压定型的碳纤维增强体转入预成型体剪裁模具,并用裁剪样模覆盖,以裁剪样模为依据,利用机械手臂将裁刀沿样模边缘进行剪裁,切除多余的碳纤维,并获得与注射模腔尺寸相对应的纤维预成型体。剪裁过程如图11、12 所示。
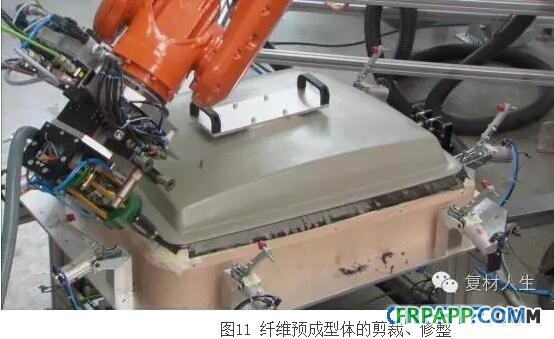
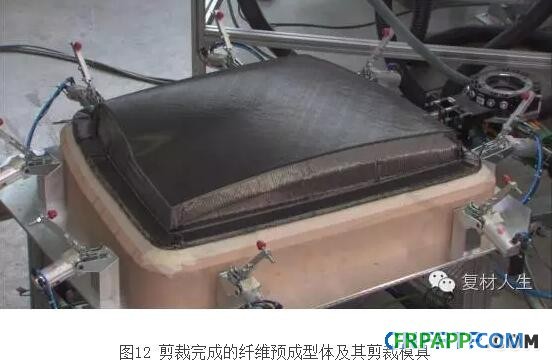
(2)压制过程
① 预成型体的放置
将放置预成型体的托架依次叠放整齐,并利用带吸盘的机械手臂将纤维预成型体吸起。将预成型体转移至开启的RTM成型模具中,并将RTM注射模具闭合,并利用锁紧机构将RTM成型模具锁紧。如图13、14、15所示。
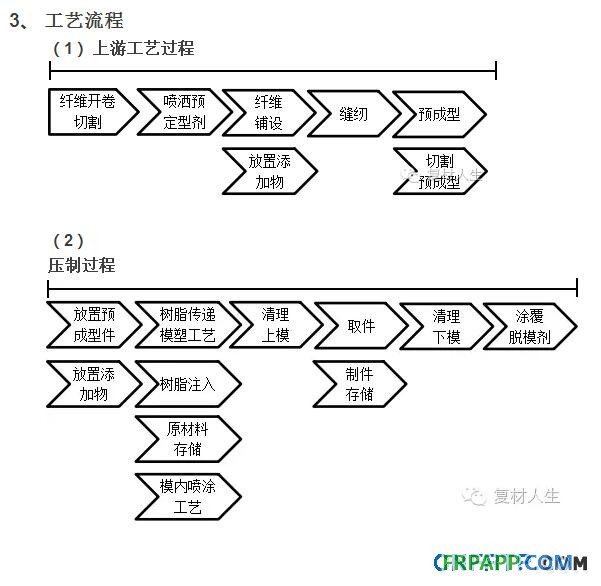
图13 纤维预成型体固定托架及机械臂、吸盘
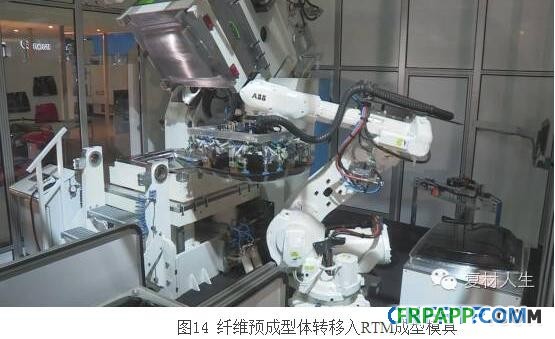
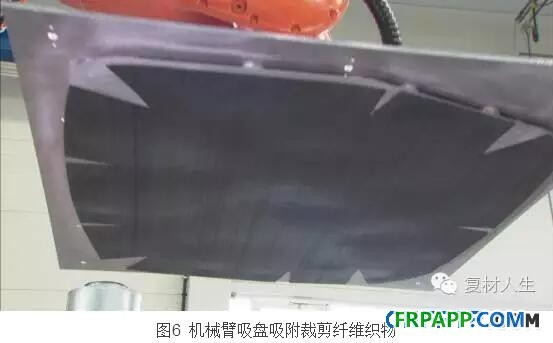
② 树脂传递注射工艺
在保证注射模型腔始终保持密封的条件下,对模具抽真空,并利用双橡胶密封圈的回弹性能,增大模具的合模间隙,如图 所示;并将液态低黏度树脂在高压注射机的作用下由模具底部中心注入高温(模具温度≥150℃)密封注射模具内。
利用高精度的高温注射机精确计量并控制树脂体系中各组分材料(主体树脂、固化剂、内脱模剂等)的比例,并在高压计量泵的作用下,进入注射机的混合头,并在混合头中高压对冲混合,并将混合均匀的树脂迅速注入高温模腔。
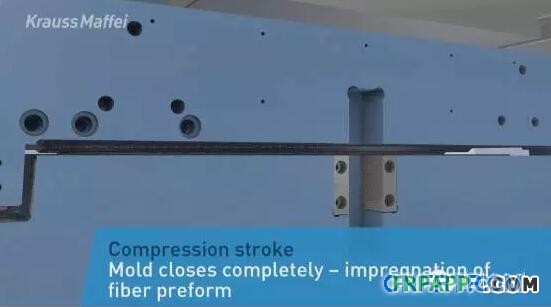
图16 HP-RTM主体树脂注射过程模具的闭合间隙
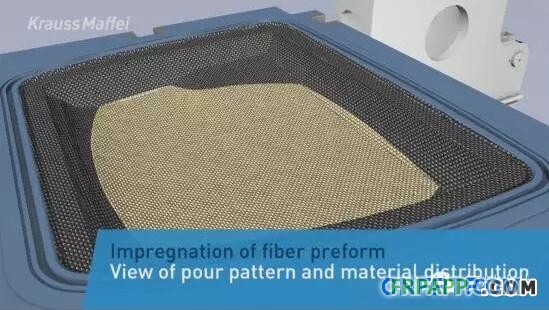
图17 HP-RTM树脂真空注射过程
注胶结束后将模具完全闭合,闭合过程中模具进一步挤压注射树脂,使其充满并浸润碳纤维增强材料,并在高温高压作用下快速固化。
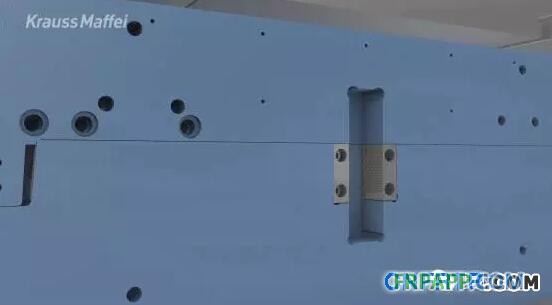
图18 注射结束时闭合模具并挤压树脂
③ 模内喷涂技术
待HP-RTM树脂固化结束,再次控制模具的合模间隙,并由预留的侧孔及流道中注入低黏度的模具表面树脂,并再次将模具完全闭合,挤压胶衣树脂使其尽可能的充模模具,并在制品表层喷涂一层均匀的树脂膜。
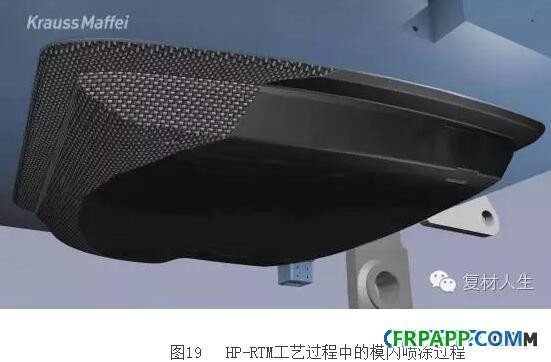
④ 脱模及模具清理
待胶衣树脂固化结束,由慢到快打开液压机,使并利用机械手臂及其吸附装置将制件吸附固定,开启顶出机构将制件顶出,并使顶出后的制件紧紧吸附在机械手臂的吸盘上。同时清理模具中残留的树脂飞边等。
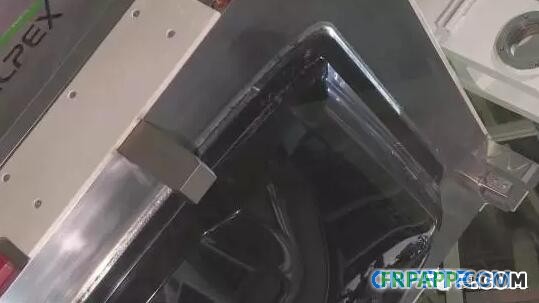
图20 模具开启时包覆在上模的制件
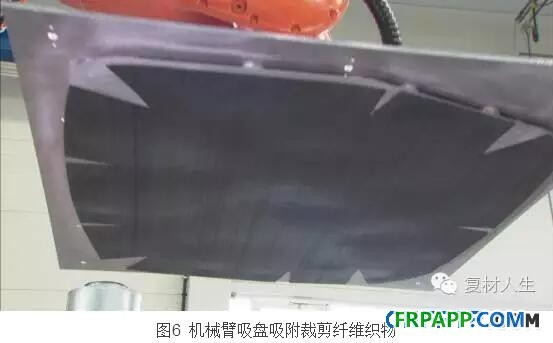
⑤制件的冷却定型
脱模后,利用机械臂及吸盘将仍处于高温状态的成型制件,转移到冷却定型工装上,并将利用真空将制件紧紧吸附在冷却定型工装,并通过冷却定型工装使制件快速冷却至室温。
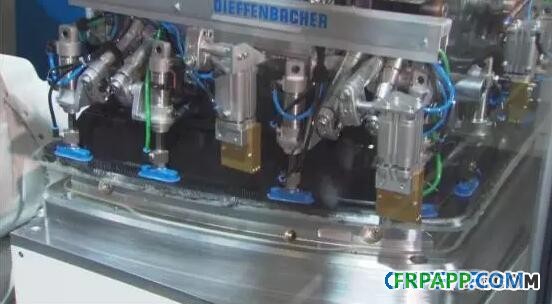
图22 制件转移至冷却定型工装
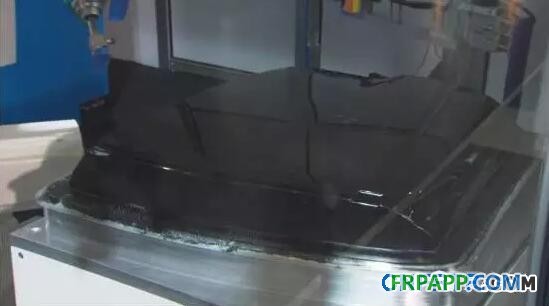
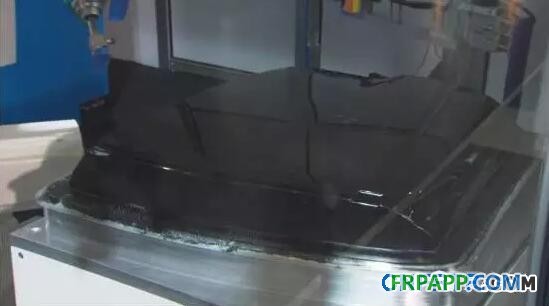
图23 冷却定型工装及成型制件
⑥ 涂脱模剂
制件脱模后,利用刷子、气泵、气嘴等清理模具,去除模具中残留的树脂及纤维等,并将模具擦拭干净。并在模具表层均匀涂覆脱模剂,并准备下一循环的生产。
(3)下游工艺过程
① 制件外形轮廓修边
将冷却定型的复合材料样件转移至机加工中心,为保证制件机加工精度,将制件直接移至机加工工装上,并利用机械手以及机加工刀具,裁剪制件边缘多余的飞边、工艺边等。
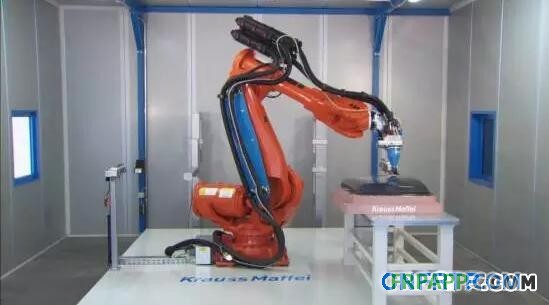
图24 复合材料制件机加工中心
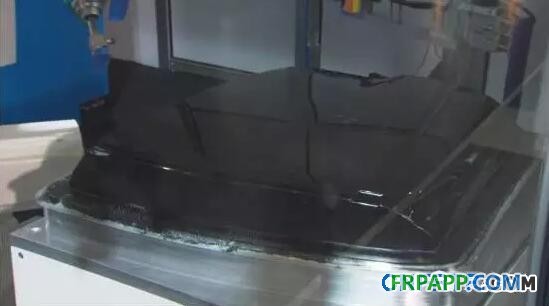
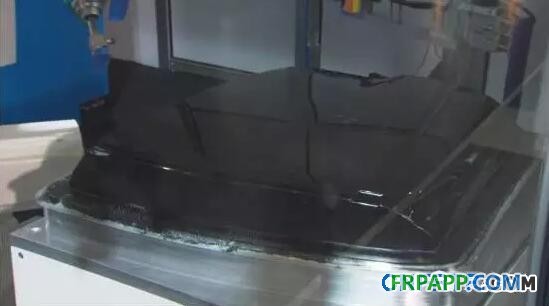
图25 复合材料机加工刀具以及刀具架
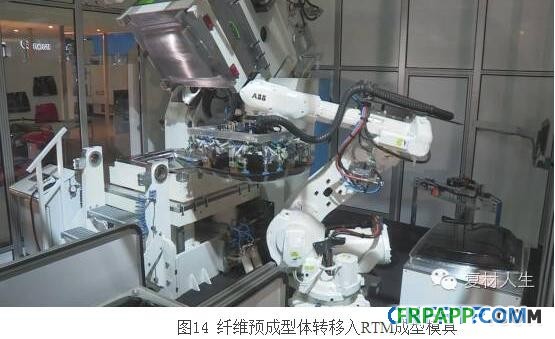
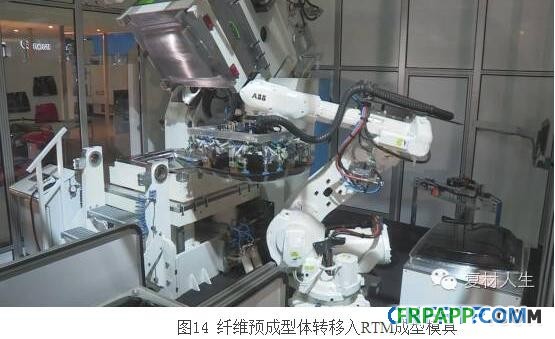
图26 复合材料制件的机加工修边处理
② 制件连接结构的加工以尺寸检查
裁边加工结束后,还需对制件的连接和配合结构,如定位孔、配合面平面度等的机加工,加工过程中需要根据情况更换裁剪刀具,以保证制件加工精度。机加工结束后,还需要更换检查工具,对制件进行尺寸公差检查,检查结束即得到满足使用要求的复合材料制件。如图27、28所示。
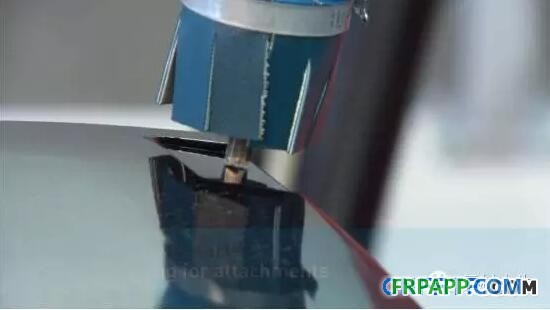
图27 复合材料制件连接孔的机加工
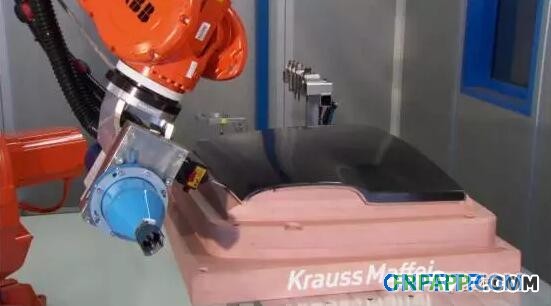
图28 复合材料制件的尺寸精度检查
"2016年复合材料闭模成型工艺技术研讨和企业现场演示交流会"11月16-18日在江苏·常州举办,报名电话/微信:18953485858 0534-2317661
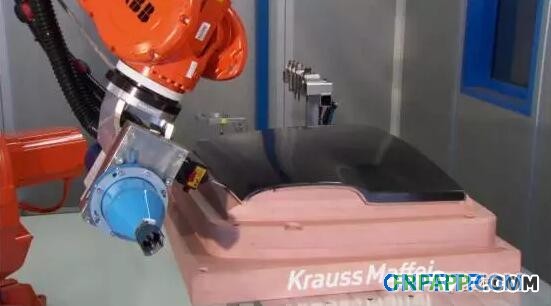
图28 复合材料制件的尺寸精度检查
"2016年复合材料闭模成型工艺技术研讨和企业现场演示交流会"11月16-18日在江苏·常州举办,报名电话/微信:18953485858 0534-2317661
5、 工艺特点
HP-RTM包括预成型加工、树脂注射、压制过程以及修整工艺。相比于传统的RTM工艺,HP-RTM工艺增加了注射后的压制过程,降低了树脂注射充填难度,提高了预制件的浸渍质量,并缩短了成型周期。具体工艺特点如下:
① 树脂快速充满模腔。较大的合模间隙和较高的注射压力(1.0-15.0MPa),以及低黏度的树脂,极大地提升了树脂的注射速度,缩短了成型工艺周期(3-5min)。
② 提高了树脂固化反应速率,缩短了树脂的固化周期。采用高活性快速固化树脂体系,并采用高效高压混合、注胶设备,使树脂基体混合均匀性更好,同时成型时需要高温环境,大大提高了树脂的固化反应速率。
③ 使用内脱模剂和自清洁系统。使用了注射混合头的自清洁技术,并在原材料中添加了内脱模剂组分,有效地提高了设备的清洁效率。
④ 降低了制件中孔隙含量,提高了制件制品性能。使用了模内快速抽真空技术有效降低了制件中孔隙含量,提高了纤维的浸渍效率,改善了纤维和树脂的界面结合能力,提升了制品的质量。
⑤ 降低了制件的工艺难度,改善了树脂浸渍增强材料的质量。采用抽真空与注射后的压缩模塑工艺相结合的方式,降低了RTM工艺注胶口和排气口设计难度,提高了树脂的流动充填能力,以及树脂对纤维的浸渍质量。
⑥ 产品的厚度和三维形状尺寸偏差低。为保证模具密封效果,采用双刚面闭合模具,同时采用大吨位液压机加压,提高了成型过程的锁模力,有效地降低了制件的厚度和形状偏差。
⑦ 产品具有卓越的表面性能和质量。采用模内喷涂技术以及高光洁度模具,使制件在很短的时间内即可获得高精度的表观质量。
⑧ 具有很高的工艺稳定性和重复性。采用间隙注胶和注胶后压缩技术,极大地提高了树脂的充模流动能力,有效降低了工艺缺陷产生的几率,具有很高的工艺重复性。
6、 关键工艺技术
(1)纤维增强材料的预定型技术
纤维预定型技术主要包括:纺织、针织和编织预成型体;缝编预成型体;短切纤维喷射预成型体;热压预成型体等。其中热压定型技术应用最广泛,该技术中定型剂是基础保证,纤维预成型模具及压制工艺技术是纤维定型的关键所在。
针对HP-RTM工艺,制件结构相对简单,因此,定型模具也相对简单,关键在于,如何通过设计并控制程序,控制定型模具和加压工装有效、有序加压定型。
(2)高精度树脂计量、混合及注射技术
HP-RTM工艺树脂的混合和注射主要包括:树脂主材和模内喷涂树脂两种体系,其控制的关键在于高精度树脂计量系统、快速均匀混合技术及混合设备自清洁技术。
HP-RTM工艺树脂主材需要在高温、高压下精确计量,则需要高精度的计量泵设备。树脂均匀混合及自清洁则需要设计有高效的、自清洁、多次混合头。
(3)成型模具温度场均匀性和密封性设计
HP-RTM工艺过程中,成型模具温度场的均匀性不仅决定和影响模腔中树脂的流动充填性能,而且对纤维的浸润性能,以及对复合材料整体性能及制品内应力都有较大的影响。因此,需要采用介质加热的方式结合高效、合理的循环油路设计。
成型模具的密封性,直接决定了树脂流动充模特征,以及成型过程的排空能力,是影响制品性能优劣的关键一环。需要根据产品设计密封圈布置位置、方式以及数量,同时需要解决模具配合间隙、顶出系统、抽真空系统等位置的密封难题,确保树脂充填过程不发生漏气现象,以保证制件性能。
(4)高精度液压机及其控制技术
HP-RTM工艺过程中,树脂的充填过程的合模间隙控制,以及压制环节的压力控制等都需要高效、高精度的液压机系统保证。同时需要根据注胶工艺、压制工艺的需要,提供适时控制技术,以保证成型过程的连续性。
7、 国内外研究开发现状及发展趋势
随着碳纤维制备加工技术的进步,使碳纤维价格大幅度下降,对碳纤维抱有期望的汽车行业看到了希望。德国宝马纯电动汽车I3和I8的问世,更是把复合材料研究的目光吸引到了在I3和I8中大量使用HP-RTM工艺技术上,据宝马公司的报道显示,如图29所示,在i3汽车车身Life模块结构的34块碳纤维复合材料制件中,其中有13件采用HP-RTM工艺制造,2件采用泡沫夹芯RTM工艺制造,其余19件采用模压工艺制造。在I8汽车上也有14件采用RTM工艺制造,如图30所示。宝马公司最新的7系列轿车,车身16件复合材料技术中共采用了4种复合材料成型工艺技术,如图31所示。
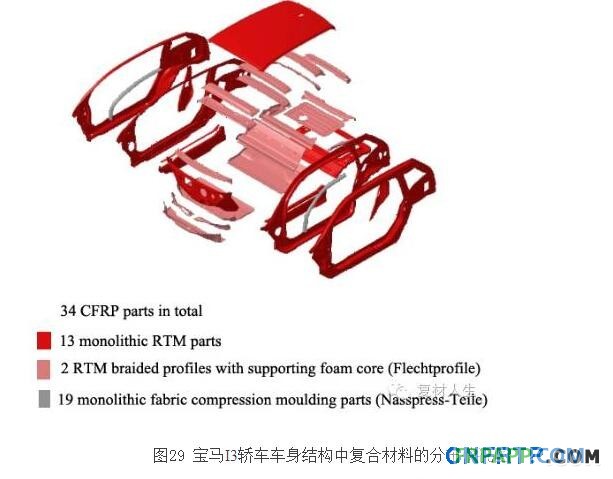
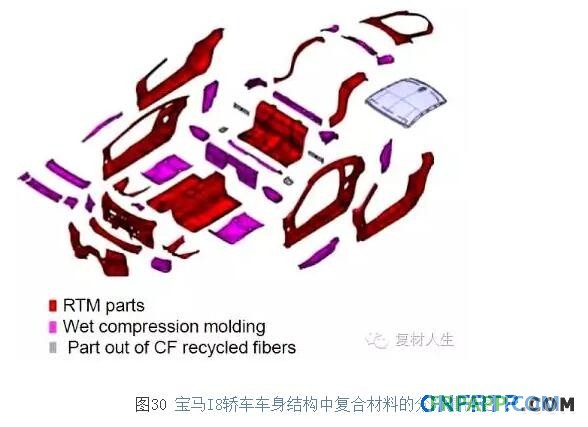
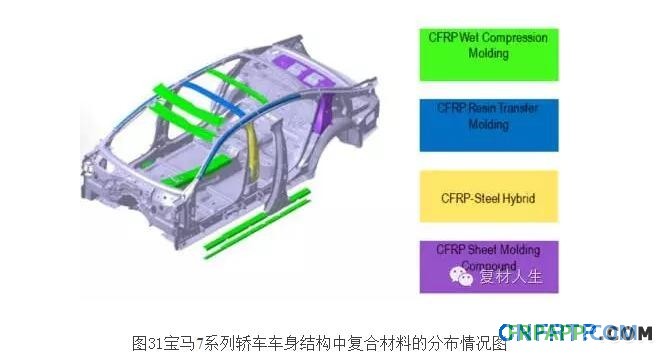
近两年来,国内外复合材料研究者对HP-RTM工艺技术及其原材料和配套设备的研制空前活跃。也取得了一系列的研究进展,具体表现为:
(1)树脂基体
HP-RTM工艺用对树脂基体的要求主要体现在:“一长”指树脂的胶凝时间适当长;“一快”指树脂的固化速度快;“两高”指树脂具有高消泡性和高浸润性;“四低”指树脂的粘度低、可挥发性低、固化收缩率低、放热峰低。
目前,相对成熟的HP-RTM工艺用树脂基体制备技术主要掌握在国际化工巨头手中,其中有代表性的有:
亨斯迈(Huntsman)公司大规模生产的两种树脂体系包括:Araldite® LY 3585/Aradur® 3475、Araldite® LY 3585/Hardener XB 3458(大量应用于I3的车身结构),这两种树脂体系既可以应用于HP-RTM工艺,也可以应用于WCM(Wet Compression Molding)工艺。两款树脂的成型温度分别为115℃、100℃,工艺周期分别为:3分30秒、6分15秒。
陶氏(DOW)化学公司VORAFORCE 5300/ VORAFORCE 5300 IMR树脂体系的注胶时间15-60s,固化时间30-120s。
瀚森(Hexion)公司开发的EP TRAC 06000/ EK TRAC 06130树脂体系,成型温度120℃,模具成型时间93s。
汉高(Henkel)公司生产的乐泰Loctite MAX3基体树脂固化时间为5.5min,用于生产汽车的车顶。
迈腾(Momentive)公司生产的Epikote 05475 / Epikure 05500 / Heloxy 112树脂体系在130℃下的成型周期为2分15秒,树脂基体玻璃化转变温度110℃。
巴斯夫(BASF )专为结构件HP-RTM工艺开发全新环氧树脂系统BaxxodurSystem2202树脂体系,该树脂在120℃下,注胶时间仅为45秒,且纤维浸润效果极佳,并能在2.5min内完成固化。
国内:上海惠柏新材公司生产的RA-8930A/B、RA-8931A/B、RA-8920A/B三种树脂体系,120℃的凝胶时间分别为34s、33s、18s。
广东博汇新材料科技有限公司生产的EpoTech®4330A/B树脂体系,可实现130 ℃ /1min或120 ℃/3min快速固化成型。EpoTech®4330A/4331B树脂体系,可是现在140 ℃/2min或120 ℃/5min快速固化成型。
(2)成型装备
目前,HP-RTM工艺装备技术发展较为成熟的主要掌握在国际机械加工设备制造巨头手中,其中有代表性的有:
德国迪芬巴赫公司(Dieffenbacher)和克劳斯玛菲公司(KraussMaffei)共同开发的高压树脂传递模塑成型工艺(HP-RTM)自动化生产线,两家公司的具体分工情况如图32所示;蒂芬巴赫公司开发的HP-RTM生产线用纤维预成型设备和压制成型设备如图33、34所示;克劳斯玛菲公司设计开发的HP-RTM工艺用注胶机和混合头如图35、36所示。
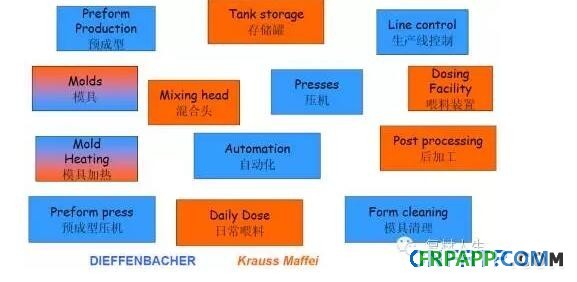
图32 迪芬巴赫公司和克劳斯玛菲公司HP-RTM生产线具体分工情况
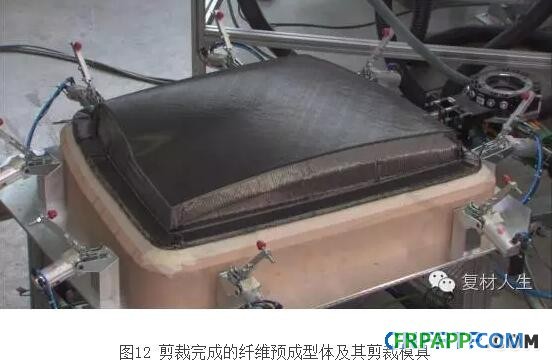
图33 蒂芬巴赫公司提供的与纤维预成型设备
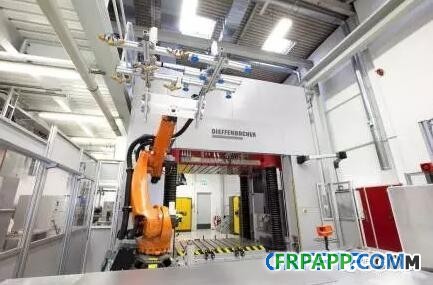
图34蒂芬巴赫公司提供的高压压制成型设备
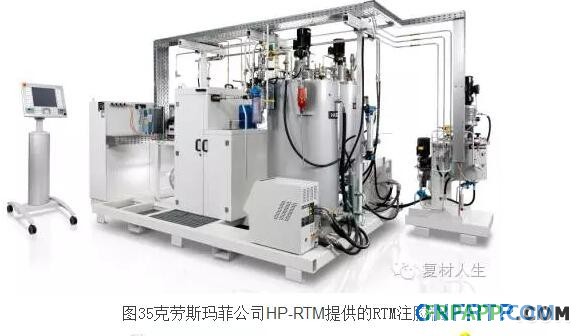
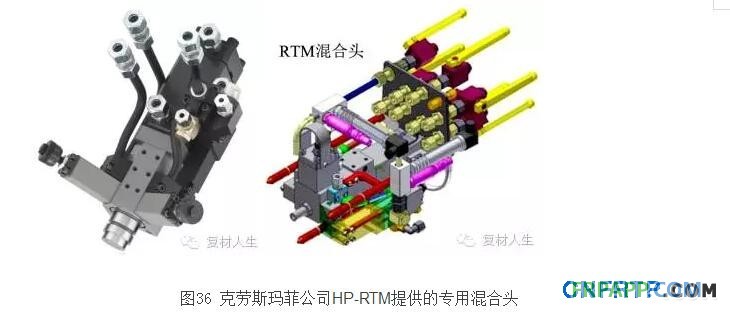
德国恩格尔公司(ENGEL)和亨内基公司(Hennecke)共同开发的高压树脂传递模塑成型工艺自动化生产线,所设计的生产线原理如图37所示,图38为生产线实物图;亨内基公司开发HP-RTM注胶机及其混合头如图39、40所示。
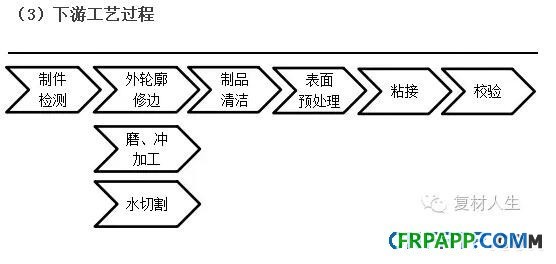
图37 恩格尔公司和亨内基公司开发HP-RTM生产线示意图
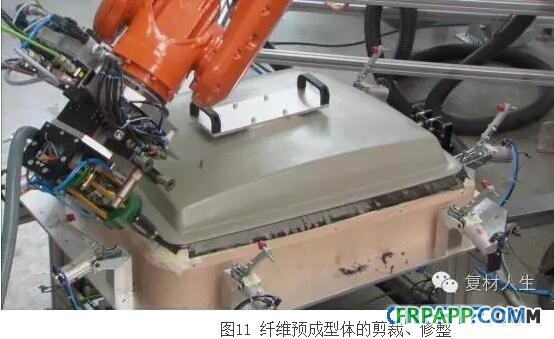
图38 恩格尔公司和亨内基公司开发HP-RTM生产线
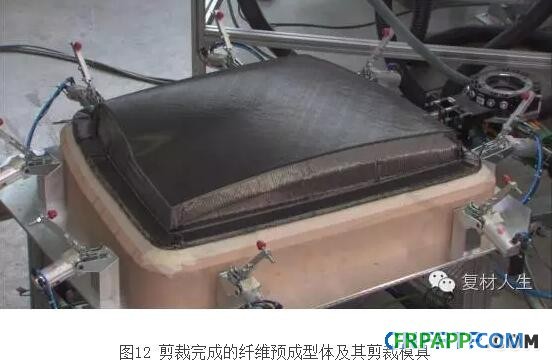
图33 蒂芬巴赫公司提供的与纤维预成型设备
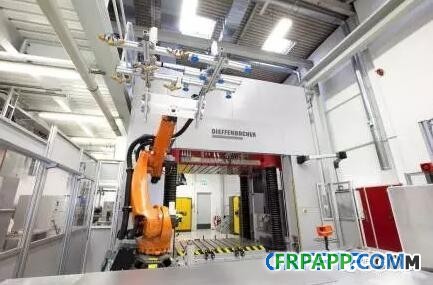
图34蒂芬巴赫公司提供的高压压制成型设备
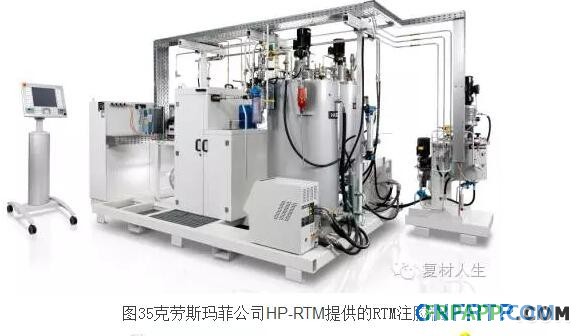
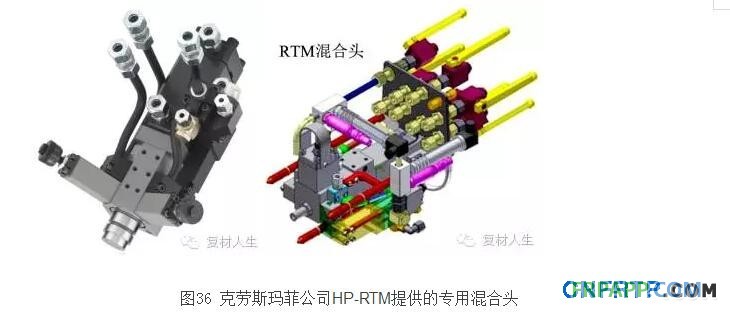
德国恩格尔公司(ENGEL)和亨内基公司(Hennecke)共同开发的高压树脂传递模塑成型工艺自动化生产线,所设计的生产线原理如图37所示,图38为生产线实物图;亨内基公司开发HP-RTM注胶机及其混合头如图39、40所示。
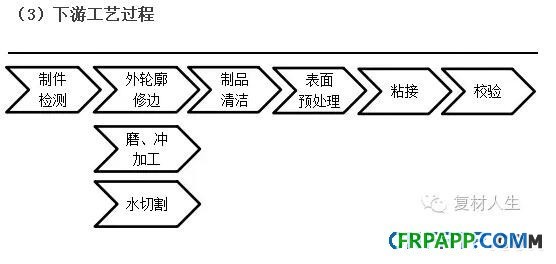
图37 恩格尔公司和亨内基公司开发HP-RTM生产线示意图
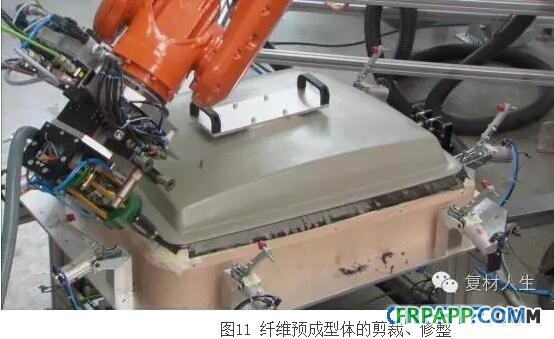
图38 恩格尔公司和亨内基公司开发HP-RTM生产线
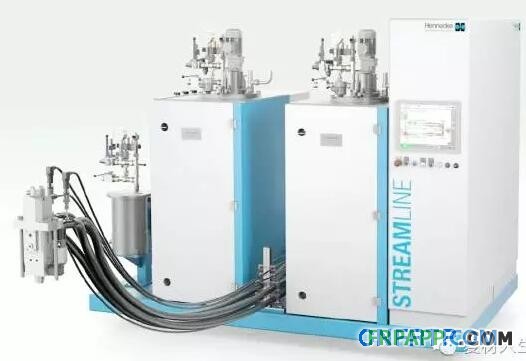
图39 亨内基公司开发HP-RTM注胶机
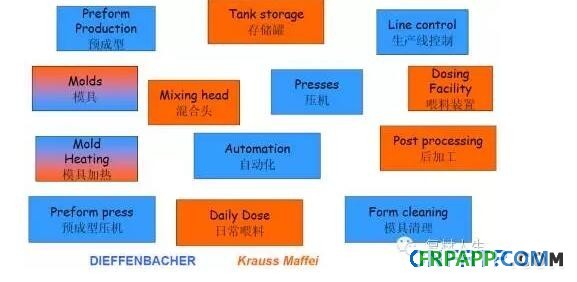
图40 亨内基公司开发HP-RTM注胶机用混合头
意大利康隆(Cannon)公司独立设计和开发了全套HP-RTM生产线如图41-45所示。
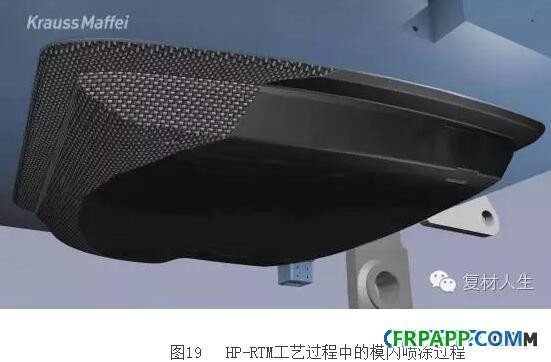
图41 康隆公司设计开发的HP-RTM生产线 1
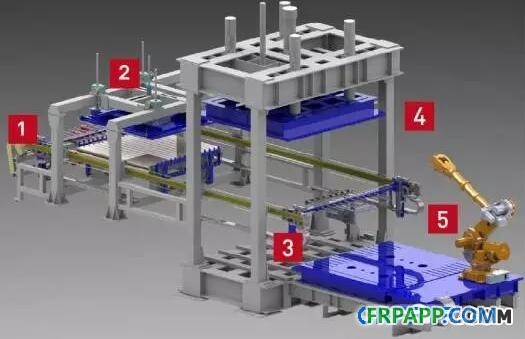
图42 康隆公司设计的HP-RTM纤维预成型生产线
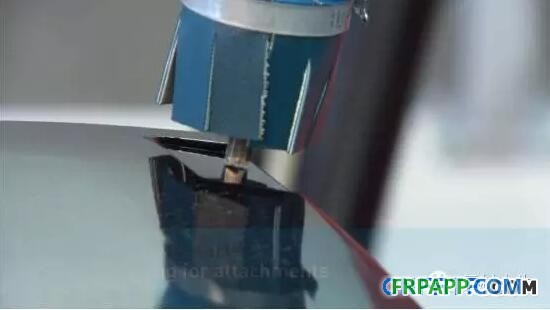
图43 康隆公司开发的HP-RTM纤维预成型生产线
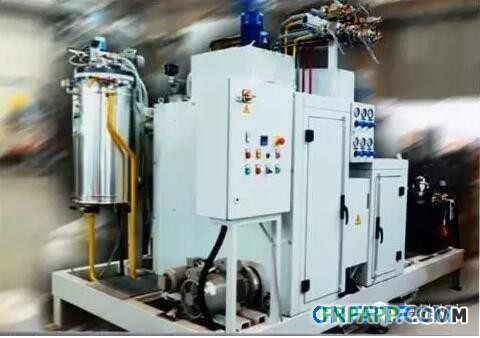
图44 康隆公司开发的HP-RTM专用注胶机
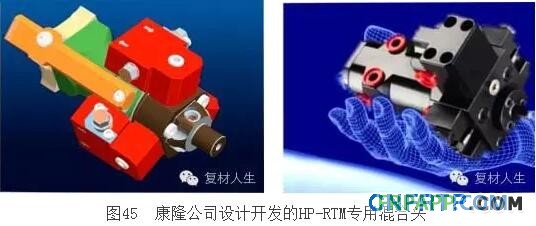
德国舒勒集团(SCHULER)与德国孚利模集团(FRIMO)有限公司也共同开发了HP-RTM生产线,所设计的生产线如图46所示;其中由舒勒公司开发的专用液压机如图47所示。
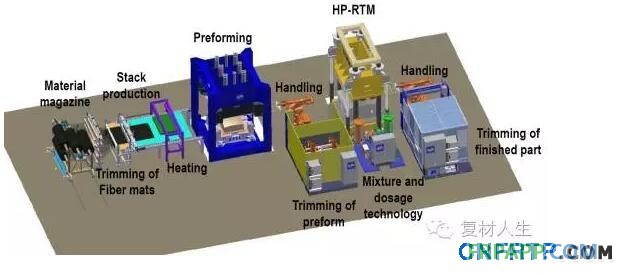
图46德国舒勒集团与德国孚利模集团设计的HP-RTM生产线
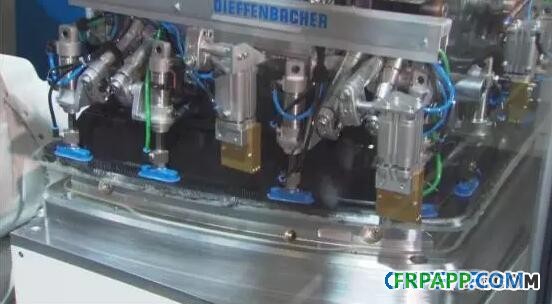
图47 德国舒勒公司生产的HP-RTM液压机
国内在HP-RTM工艺成型设备方面也进行了一定的研究,但是由于设备研发投入要求过高,单一的设备厂家无论从经费和技术储备都很难支撑整条生产线的研制任务,而各大型企业之间也缺乏有效的沟通和合作机制,因此到目前为止,除康得复合材料有限责任公司从国外引进的2条HP-RTM生产线外,还没有一条自主开发的HP-RTM生产线。国内开发的单一设备主要有:上海越科复合材料有限公司开发了HP-RTM专用注胶机,浙江优普模塑有限公司开发了快速成型双工位RTM压机及成型模具,如图48所示。
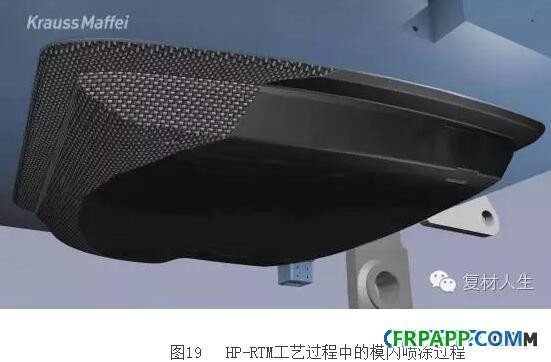
图48浙江优普模塑有限公司开发的双工位RTM压机及成型模具
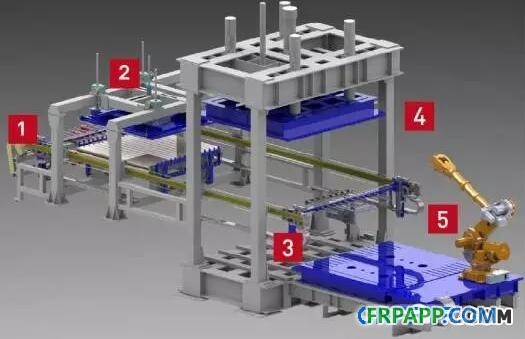
图42 康隆公司设计的HP-RTM纤维预成型生产线
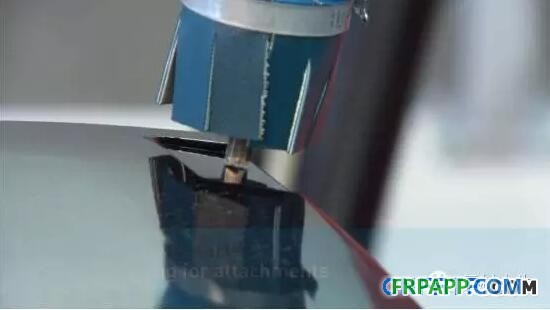
图43 康隆公司开发的HP-RTM纤维预成型生产线
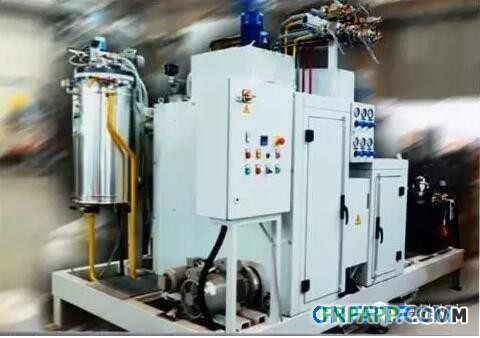
图44 康隆公司开发的HP-RTM专用注胶机
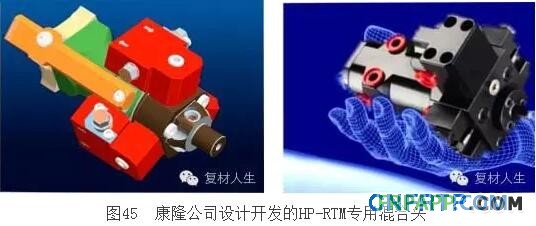
德国舒勒集团(SCHULER)与德国孚利模集团(FRIMO)有限公司也共同开发了HP-RTM生产线,所设计的生产线如图46所示;其中由舒勒公司开发的专用液压机如图47所示。
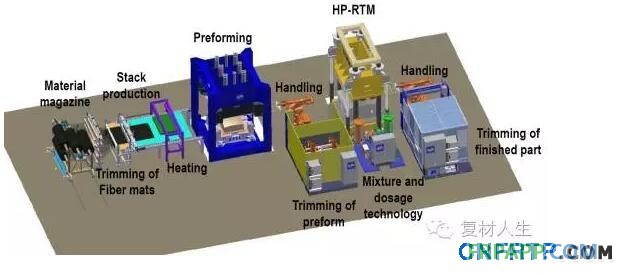
图46德国舒勒集团与德国孚利模集团设计的HP-RTM生产线
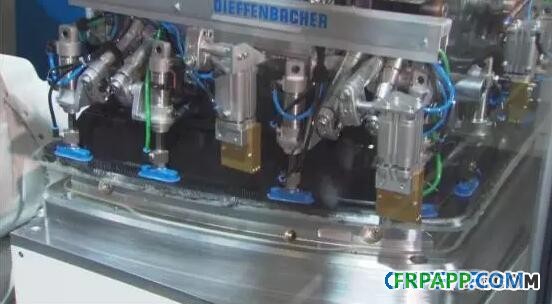
图47 德国舒勒公司生产的HP-RTM液压机
国内在HP-RTM工艺成型设备方面也进行了一定的研究,但是由于设备研发投入要求过高,单一的设备厂家无论从经费和技术储备都很难支撑整条生产线的研制任务,而各大型企业之间也缺乏有效的沟通和合作机制,因此到目前为止,除康得复合材料有限责任公司从国外引进的2条HP-RTM生产线外,还没有一条自主开发的HP-RTM生产线。国内开发的单一设备主要有:上海越科复合材料有限公司开发了HP-RTM专用注胶机,浙江优普模塑有限公司开发了快速成型双工位RTM压机及成型模具,如图48所示。
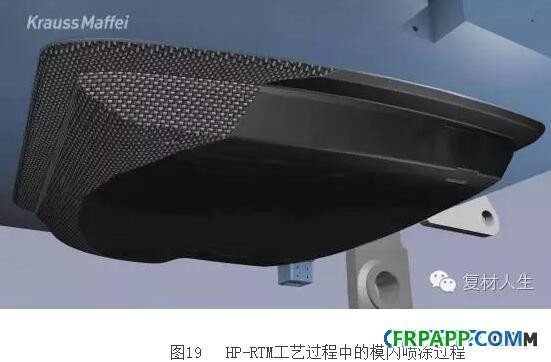
图48浙江优普模塑有限公司开发的双工位RTM压机及成型模具
(3)应用发展方向及趋势
HP-RTM所制备的复合材料具有强度模量高、孔隙含量低,表观性能优异,生产高效等特点及优势,目前所开发的产品主要用于各种具有高承载功能的汽车零部件。目前采用HP-RTM工艺生产的复合材料制品主要有:
意大利康隆集团为宝马M3轿车生产的汽车顶盖,如图49所示。宝马公司和SGL联合开发的,采用HP-RTM工艺制造的宝马i3车身Life模块车身结构,如图50所示。宝马7系列轿车侧围车顶加强板、车顶中横梁结构均采用HP-RTM工艺制作,如图51所示。本特勒-西格里(Benteler-SGL)采用汉高公司的乐泰(Loctite)树脂基体采用HP-RTM生产的复合材料板簧重量可减轻65%,如图52所示;本特勒-西格里采用HP-RTM工艺生产的复合材料车用支杆,如图53所示。克劳斯玛菲采用汉高Loctite Max3树脂生产的汽车车顶,如图54所示。蒂芬巴赫公司生产的HP-RTM复合材料后备箱内衬板,如图55所示。上海惠柏新材公司采用RA-8920A /B生产的汽车车顶如图56所示。
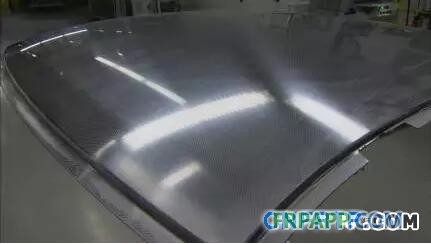
图49 宝马M3轿车HP-RTM顶盖
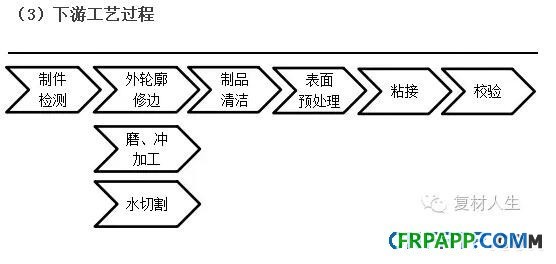
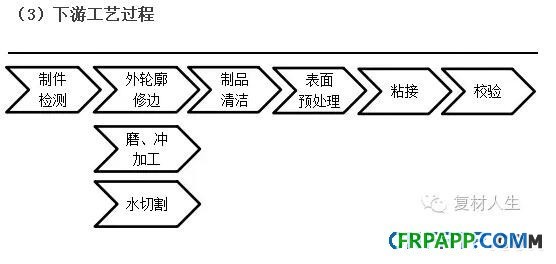
图50 宝马公司和SGL联合开发的I3轿车车身
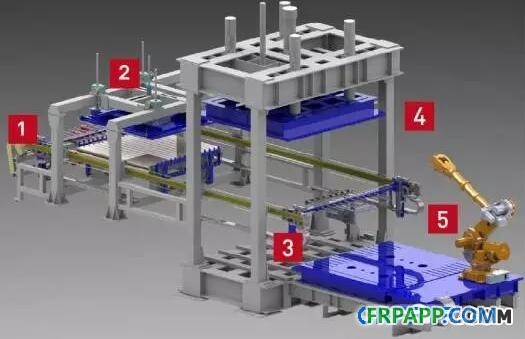
图51 宝马7系列轿车用HP-RTM侧围车顶加强板
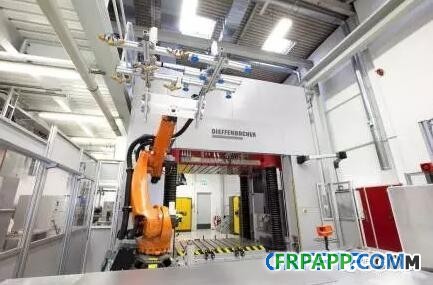
图52 本特勒-西格里采用HP-RTM生产的复合材料板簧
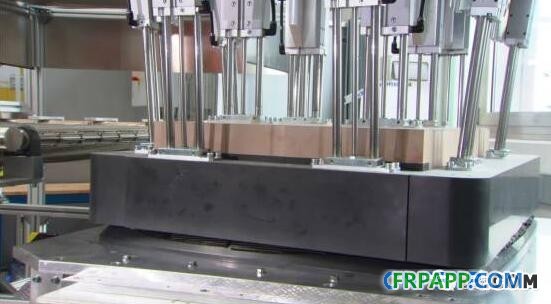
图53 本特勒-西格里采用HP-RTM工艺生产的复合材料车用支杆
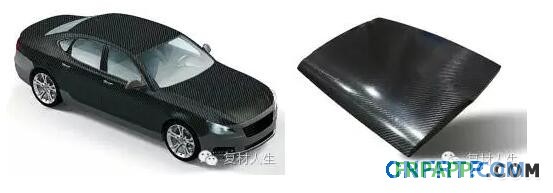
图54 采用汉高Loctite Max3树脂生产的汽车车顶
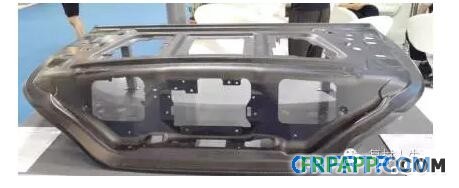
图55 蒂芬巴赫公司生产的HP-RTM复合材料后备箱内衬板
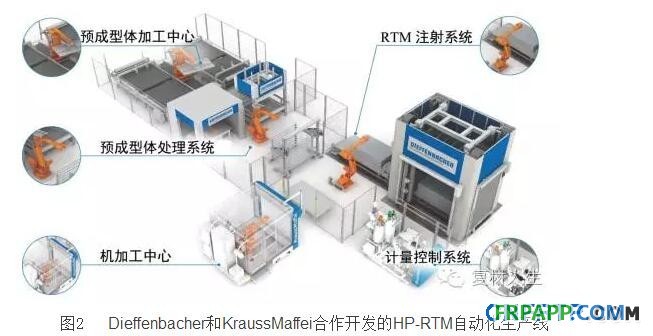
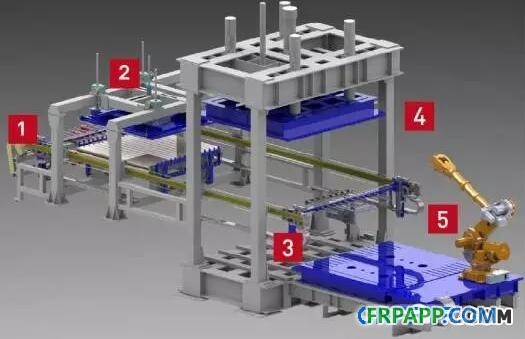
图51 宝马7系列轿车用HP-RTM侧围车顶加强板
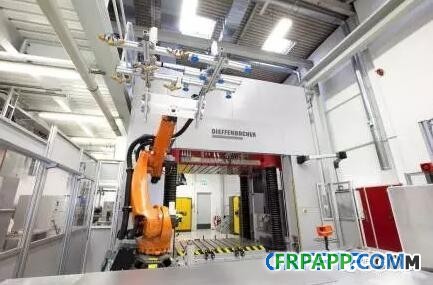
图52 本特勒-西格里采用HP-RTM生产的复合材料板簧
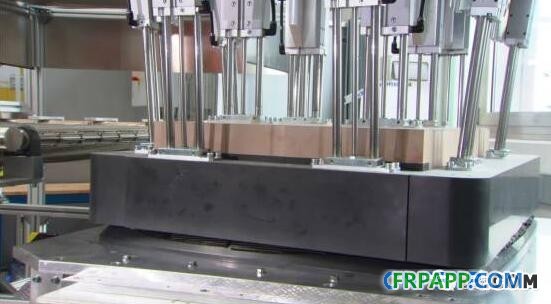
图53 本特勒-西格里采用HP-RTM工艺生产的复合材料车用支杆
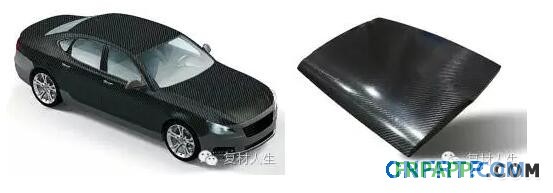
图54 采用汉高Loctite Max3树脂生产的汽车车顶
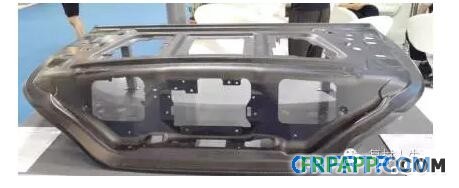
图55 蒂芬巴赫公司生产的HP-RTM复合材料后备箱内衬板
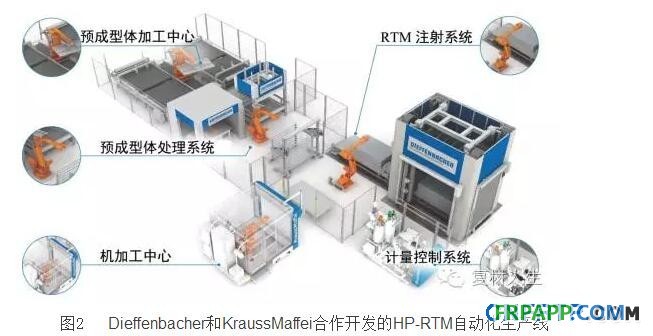
图56 上海惠柏新材公司采用RA-8920A/B生产的汽车车顶
由HP-RTM工艺制品的应用开发情况不难看出,目前开发的产品主要集中在具有较高强度要求的复合材料结构件领域。而且由于HP-RTM工艺装备体系既包括纤维预成型系统,还需要快速液压系统、高效自清洁混合注胶系统、高密封模具系统、计算机控制系统等,设备体系繁杂,制造技术难度大,大大提高了复合材料零部件的制造成本,虽然该工艺技术满足汽车产品的生产节拍要求,但其较高制造成本与汽车行业要求的低成本尚有一定的差距,因此,推广应用难度较大。
综上所述,HP-RTM工艺技术进一步推广应用必须解决的问题主要包括:
①高效率、低成本制造装备的设计和制造技术能力;
②高性能、低黏度、快速固化树脂体系的研制和开发;
③行业相关企业的协同开发机制和合作模式;④积极探索和开发新的应用市场。
本文由中北大学材料科学与工程学院张彦飞先生提供,转载请标明出处,谢谢!