在复合材料修复技术中,胶粘剂的选用对其防护性能具有至关重要的影响。胶粘剂是一类单组分或多组分、具有优良粘接性能、在一定条件下能使被胶接材料通过界面的粘附和物质的内聚等作用紧密地胶合在一起的粘结剂。胶粘剂通常是由基料、固化剂、增韧剂、稀释剂、偶联剂等组分按一定的比例和工艺流程配合而成。
环氧树脂胶粘剂是目前应用最为广泛的一种胶粘剂[3],其基体材料来源广泛,适用粘接多种基材,具有强度高、固化收缩率低、耐腐蚀、热稳定性及电绝缘性能好等特点,而且具有施工工艺简便、工效高、能耗小、成本低等优点,可大大降低劳动强度,节省人力成本,在油气管道外防腐层的修复中具有广泛的应用前景。
环氧树脂含有多个苯环或杂环,分子链柔性小,固化后的环氧树脂具有高的交联结构,该交联结构不易变形,导致环氧树脂类胶粘剂存在韧性不足、易脆裂、剥离强度低和抗冲击性差等缺点,使其应用受到极大的限制,因此环氧树脂的增韧改性对其在管道修复中应用具有重要的现实意义。
1·环氧树脂胶粘剂的改性
在众多环氧树脂增韧技术中,以聚氨酯为代表的弹性体的增韧效果最为显著[4]。但是环氧树脂是线型的热塑性树脂,本身不会硬化,只有加入固化剂,使它由线型结构交联成网状或体型结构,才能实现固化。因此,在利用聚氨酯对环氧树脂进行增韧的同时,需要添加固化剂,使其满足施工时对固化性能的要求。
选用的固化剂为T一31,T一3l固化剂是一种透明的棕色粘稠液体,属于酚醛胺类固化剂,易溶于丙酮、乙醇、二甲苯等有机溶剂,微溶于水,毒性极小。分子内含脂肪胺类分子中的活性氢,又含有能起催化、促进环氧树脂固化的基团和苯环结构。与脂肪胺相比,具有较强的憎水性,能在0℃以下的低温下固化环氧树脂,也完全可以在相对湿度大于90%或水下固化各种环氧树脂。T一31环氧树脂固化剂具有耐腐蚀、抗渗透性好、固化速度快、粘接强度高、操作使用方便、价格较低等特点适用范围非常广泛。根据需要加入适量T—31固化剂调节固化反应速度,使环氧树脂胶粘剂既能保证室温下的固化速度,又能保证固化产物较好的力学性能。
固化剂是用于提高胶粘剂的固化性能,增韧剂是用于提高胶粘剂的力学性能,但是固化剂的加入必定会影响胶粘剂的力学性能,同时增韧剂的加入也可能会影响胶粘剂的固化性能。以下研究固化性能和力学性能随着固化剂和增韧剂添加量变化的规律。
1.1固化性能研究
首先考察固化时间随着成分的变化,调节固化剂用量分别为16.67%、20%、23.08%、25.93%,在每个固化剂用量下改变聚氨酯用量为9.09%、13.04%、16.67%、20%。测量了每个组分配比下的固化时问,固化时间的测量按照GB1728-79《漆膜、腻子膜干燥时问测定法》来测量,实验结果如表1所示。
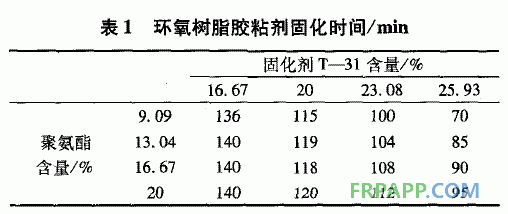
通过分析实验结果发现,固化时间随着固化剂的添加量增加而缩短,而当固化剂用量固定后聚氨酯在实验范围内添加量的改变对固化时间影响较小。
其次,研究了固化剂添加量对力学性能的影响。选取聚氨酯的用量为16.67%固化剂用量变化的一组数据,测量了胶粘剂的剥离强度和抗剪切强度,测量数据如表2所示。胶粘剂的抗剪切强度(拉伸剪切强度)按照GB7124-1986(胶粘剂拉伸剪切强度测定方法(金属对金属)》进行测试,剥离强度按照GB/T2790-1995《胶粘剂180°剥离强度试验方法挠性材料对刚性材料》进行测量[6]。
从表2数据可以看出,随着固化剂添加量的增加,胶粘剂的力学性能迅速下降。因此,单纯从力学性能考虑,应尽量减少固化剂的用量。综合考虑,施工中一般要求胶粘剂在两个小时左右内完成固化。所以这里选择固化剂用量为16.67-20%为宜。
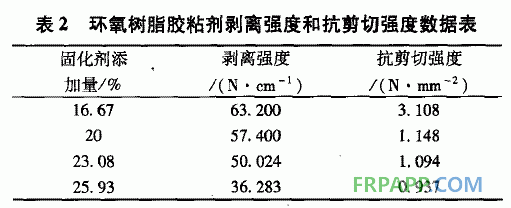
1.2力学性能研究
基于上述研究,固定固化剂的用量,考察了聚氨酯变化对胶粘剂力学性能的影响。固化剂的用量分别选取了16.67%和20%,然后改变聚氨酯的添加量,分别选择质量分数为9.09%、13.04%、16.67%、20%、23.08%。测得的抗剪切强度和剥离强度如表3和表4所示。
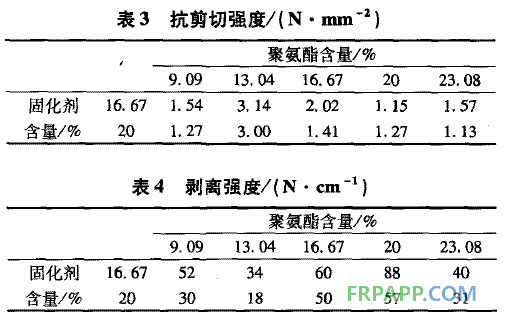
依据表3和表4数据,将环氧树脂胶粘剂的抗剪切强度和剥离强度随聚氨酯的添加量的变化曲线绘制如图1所示。从图1中可以看出,随着聚氨酯添加量的增加,环氧树脂胶粘剂的抗剪切强度先 上升后下降,在聚氨酯添加量为13.04%时出现最大值;环氧树脂胶粘剂的剥离强度先增加后减小,在聚氨酯为20%时出现最大值。
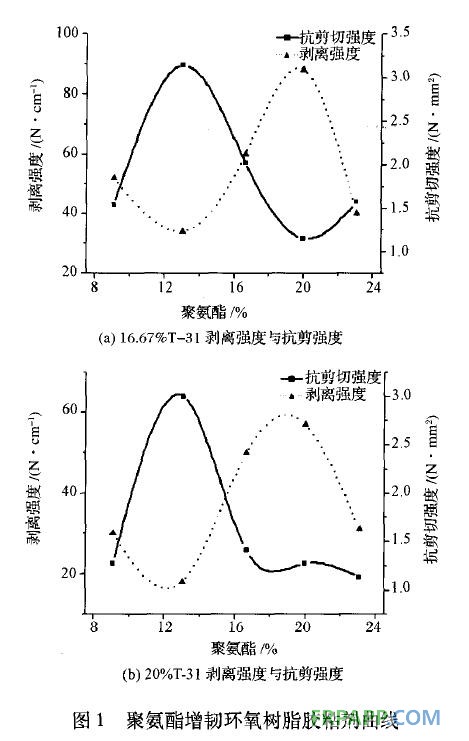
1.3增韧机理
聚氨酯对环氧树脂胶粘剂进行增韧改性时,聚氨酯链段贯穿到环氧树脂链段中,形成互穿聚合物网络结构(IPN)或半互穿聚合物网络结构(SIPN)。因为聚氨酯与环氧树脂溶解度不同,IPN材料呈现不同程度的相分离,但由于网络间相互缠结,发生“强迫互溶”,使相容性增加;并且聚合物一经交联后,相互缠结的网络使相区固定,由于聚氨酯颗粒分散在连续的环氧树脂相中,使体系的韧性增加,分散了固化物的应力集中,抗剪切强度增大。随着聚氨酯添加量的增加,抗剪切强度逐渐增大,但当聚氨酯的含量超过13.04%时,由于聚氨酯/环氧树脂形成的互穿聚合物网络结构的互穿程度已经达到饱和。进一步增加聚氨酯用量,互穿聚合物网络会出现互穿过度,聚氨酯与环氧树脂相分离,形成裂缝,聚氨酯与环氧树脂的相容性急剧下降。因此,对抗剪切强度而言,最佳的聚氨酯用量为13.04%。
剥离强度高低主要和环氧树脂胶粘剂的粘结性能及柔韧性有关,由聚氨酯和环氧树脂形成的互穿聚合物网络结构体系的变化规律可知,随着聚氨酯添加量的增多,固化物的柔韧性出现先增后降的变化,所以环氧树脂胶粘剂的剥离强度会随聚氨酯的添加量增加出现先增大后减小的趋势。当聚氨酯达到20%之后,剥离强度随着聚氨酯添加量的增加开始下降。因此,对剥离强度而言,最佳的聚氨酯用量为20%。
1.4最佳组分
从图1中还可以看出,聚氨酯对环氧树脂胶粘剂的抗剪切强度和剥离强度的改性变化是不同步的,即抗剪切强度和剥离强度的最大值对应的聚氨酯含量是不一致的。所以,综合考虑聚氨酯的添加量对于环氧树脂胶粘剂性能的影响,我们认为聚氨酯最优的添加量为16.67%。
2·结论
采用聚氨酯对环氧树脂胶粘剂进行增韧改性,首先研究了固化剂添加对固化时间和力学性能的影响,发现随着固化剂添加量的增加,固化时间缩短,但是力学性能迅速下降,在满足施工对固化时问要求的情况下,选择了尽可能少的固化剂添加量16.67%_20%。在确定了固化剂用量后,开展了聚氨酯添加量对力学性能的研究,研究发现聚氨酯对环氧树脂胶粘剂的抗剪切强度和剥离强度的改性变化是不同步的,对抗剪切强度13.04%的聚氨酯性能最好,而对剥离强度20%的聚氨酯性能最佳。综合考虑聚氨酯最优添加量为16.67%。该研究改性了环氧树脂胶粘剂,获得了固化性能和力学性能良好的胶粘剂,在油气管道防腐层的修复中具有重要的应用前景。