第三章 建造工艺
3.1模具
3.1.1生产条件
3.1.1.1原材料贮存
原材料的贮存除应符合原材料生产厂的有关规定外,还应符合下列规定:
(1)树脂和添加剂应储存于密闭的容器内,并置于低温、干燥和避光的贮藏室中。
(2)纤维增强材料应储存在干燥、无尘和温度变化不大的场所,不可储存在温度会骤变的场所。
(3)引发剂与促进剂应分开贮存。
3.1.1.2车间环境
(1)成型车间、配料间和原材料储存间应为具有坚固结构的建筑物。
(2)建造船体和主要构件的成型车间应能确保成型时温度和湿度的基本稳定。
(3)成型车间温度应保持在10 32℃之间。
(4)成型车间内空气的相对湿度应不超过85 %,并应保持平稳,避免结露和凝雾。
(5)通风调节设备和温湿度计在整个树脂固化期内均应处于良好状态。
(6)成型车间应有良好的照明,但应避免自然光和人工照明对树脂固化产生影响。
3.1.2成型工艺
3.1.2.1成型车间
(1)成型车问应有良好的照明,并具有通风设备,但应避免阳光和人工照明直接照射而影响树脂的正常固化。
(2)成型车问的温度在10℃-32℃之间,相对湿度应在40% ~85%之间,并保持稳定。
3.1.2.2成型模具
(1)成型模具应具有足够刚度和强度,且不易变形。模具的尺寸、光洁度应满足产品的要求。
(2)模具应清洁干燥,且脱模容易。
(3)脱模剂应均匀地涂于模具表面,严禁遗漏。
3.1.2.3配胶与涂胶
(1)成型前必须进行凝胶试验,以确定合适的树脂最佳配比。
(2)表面胶衣树脂的厚度应在0.4~0.6mm之问,且应厚度均匀。
(3)配胶时,树脂中加入引发剂和促进剂后应逐一搅拌均匀,严禁引发剂直接与促进剂接触。一次配胶量不宜过大。
(4)成型应在胶衣树脂初步凝胶后较短时问内进行。
3.1.2.4手糊成型工艺
(1)糊制层板的每层增强材料时,应使树脂涂敷均匀并充分浸渍增强材料以获得预定树脂含量。
(2)应严格控制每层树脂的用量。各铺层之间的树脂含量应均匀,以保证层板的厚度和质量。层板的厚度偏差不得大于5%0
(3)铺排纤维增强材料层时应尽量减少接缝的数目,同一层纤维增强材料片边缘可采用搭接或对接的方法连接。不同层的接缝应错开100mm,五层之内接缝应不重叠。若采用搭接时,搭接的宽度应不小于50mm。纤维增强材料层少于五层的层板不应采用对接方式。
(4)糊制过程中,应消除气泡,避免增强材料片滑移。如果发现有纤维裸露、缺胶和积胶等妨碍使用的缺陷,应在糊制下一层增强纤维前修补完好。
(5)使用环氧树脂时,船厂应制订手糊工艺的补充规定,以防止缺陷,保证质量。
3.1.2.5喷射成型工艺
(1)纤维和树脂喷射成型法仅在喷射法施工易于保证成型良好的结构面上使用。
(2)喷射设备在使用前应进行校准,以保证喷出的纤维百分比符合预定的要求。在操作期间还应定时校验,以保证纤维长度和层板成份。
(3)当采用喷射成型工艺时,应采取消除气泡的措施。当喷射纤维量达600g/mm2时,应使用滚压法或其他方法消除气泡。
3.1.2.6真空成型工艺
将玻璃纤维布和毡干铺在阴模上,合上阴模,抽出模具内空气,然后沿分布在模具周围的若干注射点定量注入树脂,待树脂固化后即可开模脱下。用这种工艺建造的船舶重量较轻,树脂较少,船体内外光洁,厚度均匀,船体分层破坏的可能性极小,这种方法的主要特点是自动化程度高、污染少、船体壳板中气泡含量低。
3.1.3 脱模
(1) 模制件铺敷完成后,在与壳体铺敷相当的环境下,壳体在模具中搁置时间不少于48h。
(2)船体的脱模应在其巴氏硬度大于或等于40后及加强材、隔舱板成型安装后进行,其余大型构件也应在加强材成型固化后方可脱模。
(3)脱模后,模具和制品应放在支架上,避免生产变形。
3.2结构与板材连接
3.2.1铺层工艺
以玻璃纤维及其制品增强的层板试件应符合下表的要求
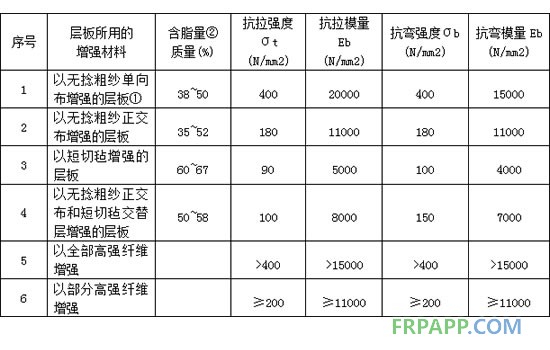
3.2.2结构细则
船体的连接可采用现场糊制、粘接或机械连接等方法。当骨材交叉时,应在大骨材上开孔,使小骨材连接通过,当骨材尺寸相近时,一般应使纵向骨材保持连续。骨材相交处应选用毡片或毡布交替铺层连接。
3.2.2.1甲板与舷侧板的连接
(1)甲板与舷侧板的连接除应保证结构的完整性以承受总纵弯矩之外,还应能承受由甲板局部载荷造成的角变形。甲板与舷侧板的连接示例见图A2.1(1)至图A2.1(12)
船体的连接可采用现场糊制、粘接或机械连接等方法。当骨材交叉时,应在大骨材上开孔,使小骨材连接通过,当骨材尺寸相近时,一般应使纵向骨材保持连续。骨材相交处应选用毡片或毡布交替铺层连接。
3.2.2.1甲板与舷侧板的连接
(1)甲板与舷侧板的连接除应保证结构的完整性以承受总纵弯矩之外,还应能承受由甲板局部载荷造成的角变形。甲板与舷侧板的连接示例见图A2.1(1)至图A2.1(12)
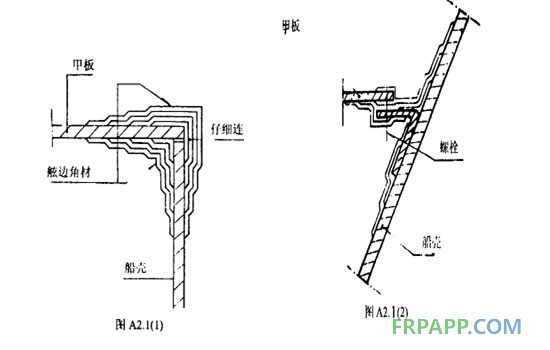
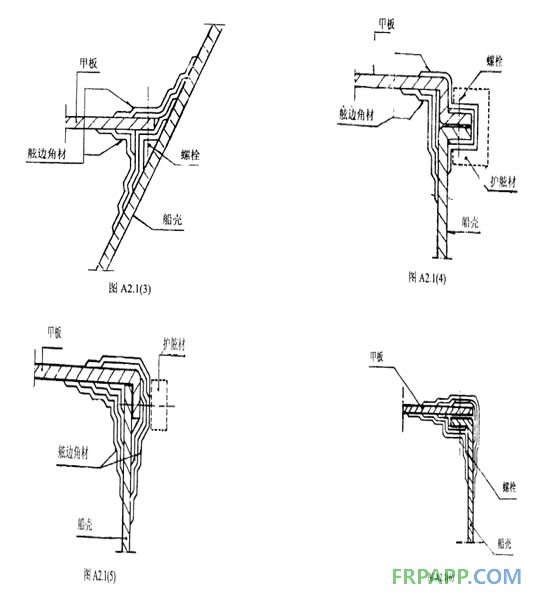
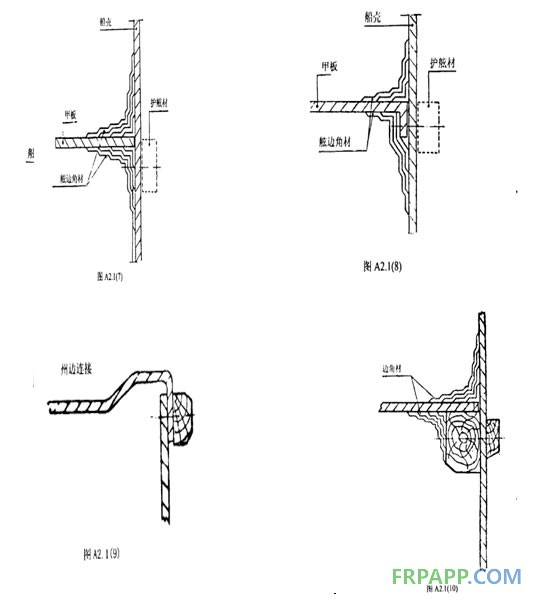
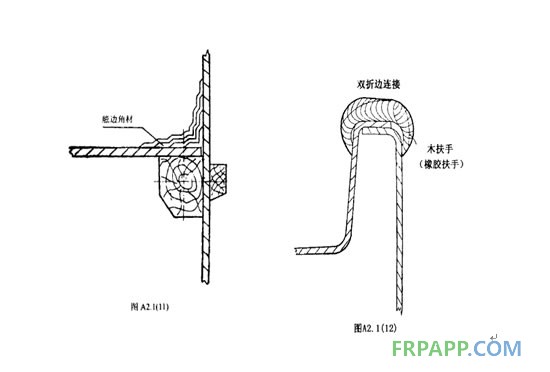
(2)通常甲板与舷侧板的连接程序为:先将板甲与舷侧板连接,接着铺敷角材,然后再铺敷与之正交的横梁和肋骨。
3.2.2.2骨架构件之间的连接
(1)骨架构件之间的连接(如横梁与肋骨的连接)可采用机械连接和粘接两种方式。
(2)骨架构件之间的连接可分为有肘板型和无肘板型两种。为了增加角部连接的刚性,一般多采用有肘板的骨架构件连接形式。
(3)预制肘板的组装见图A3.3(1)所示;
(4)单腹板骨材的角接,在面板宽度不同时应逐渐过渡,见图A3.3(2)所示;
(5)预制骨材按对接规定组装的连接方式,见图A3.3(3)所示;
(6)帽型骨材现场糊制有肘板角连接的方式,见图A3.3(4)所示;
(7)帽型骨材现场糊制无肘板角连接的方式,见图A3.3(5)所示去除甲板后,其节点连接如图A3.3(6)所示。
3.2.2.2骨架构件之间的连接
(1)骨架构件之间的连接(如横梁与肋骨的连接)可采用机械连接和粘接两种方式。
(2)骨架构件之间的连接可分为有肘板型和无肘板型两种。为了增加角部连接的刚性,一般多采用有肘板的骨架构件连接形式。
(3)预制肘板的组装见图A3.3(1)所示;
(4)单腹板骨材的角接,在面板宽度不同时应逐渐过渡,见图A3.3(2)所示;
(5)预制骨材按对接规定组装的连接方式,见图A3.3(3)所示;
(6)帽型骨材现场糊制有肘板角连接的方式,见图A3.3(4)所示;
(7)帽型骨材现场糊制无肘板角连接的方式,见图A3.3(5)所示去除甲板后,其节点连接如图A3.3(6)所示。
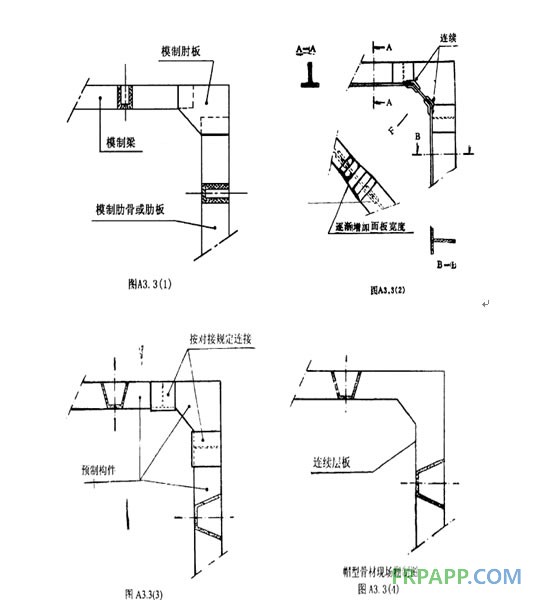
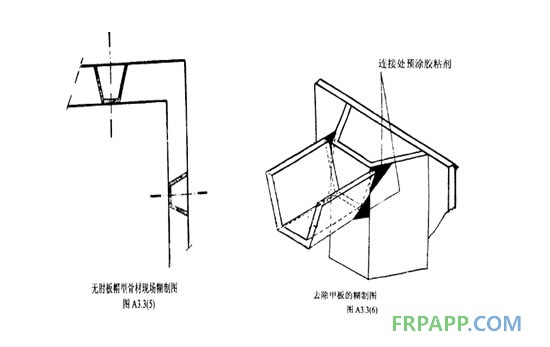
3.2.2.3舱壁与船壳的连接。
(1)舱壁与船壳的连接处为船体受总纵弯曲变形时的刚性点,为减少其连接刚性而使其在小变形时的应力分布较均匀,建议采用图A4.1(1)至(4)的连接方式。
(1)舱壁与船壳的连接处为船体受总纵弯曲变形时的刚性点,为减少其连接刚性而使其在小变形时的应力分布较均匀,建议采用图A4.1(1)至(4)的连接方式。
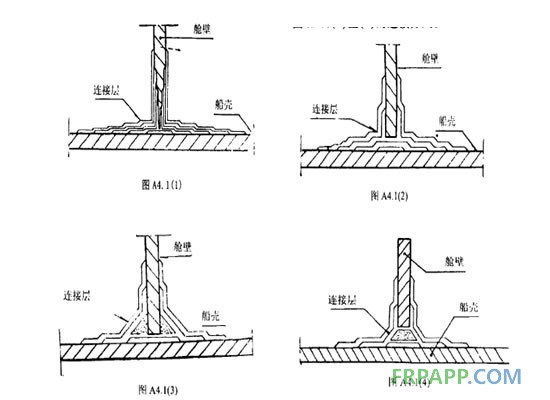
3.2.2.4水密舱壁与骨材的连接
(1)为了保证水密舱壁在破舱情况下保持水密,对穿过舱壁的连接帽型骨材和其他骨材本身也应在水密舱壁处是水密的。
(2)图A5.2(1),(2),(3)显示了装有水密内隔板的帽型骨材的装配方法。水密舱壁与帽型骨材的连接应是将带有腹板的帽型骨材预制件先在船壳底板上装好,然后再进行舱壁定位。
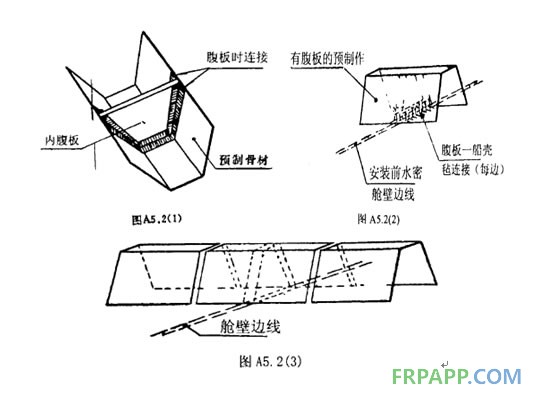
3.2.2.5支柱
(1)纤维增强塑料船可以使用金属支柱,为此应考虑钢、铝等金属支柱及其连接板在纤维增强塑料上的安装,应制定工艺措施。
(2)安装金属支柱时,支柱上下端与复合材料连接的金属板必须先与支柱焊接成一个整体,不允许先装金属板再焊上金属支柱,见图A6.2所示。
(3)当采用管子套管子来调整支柱长度时,应尽量在金属支柱一端进行调整。调好尺寸后,卸下焊毕后再安装,见图A6.3所示。
(1)纤维增强塑料船可以使用金属支柱,为此应考虑钢、铝等金属支柱及其连接板在纤维增强塑料上的安装,应制定工艺措施。
(2)安装金属支柱时,支柱上下端与复合材料连接的金属板必须先与支柱焊接成一个整体,不允许先装金属板再焊上金属支柱,见图A6.2所示。
(3)当采用管子套管子来调整支柱长度时,应尽量在金属支柱一端进行调整。调好尺寸后,卸下焊毕后再安装,见图A6.3所示。
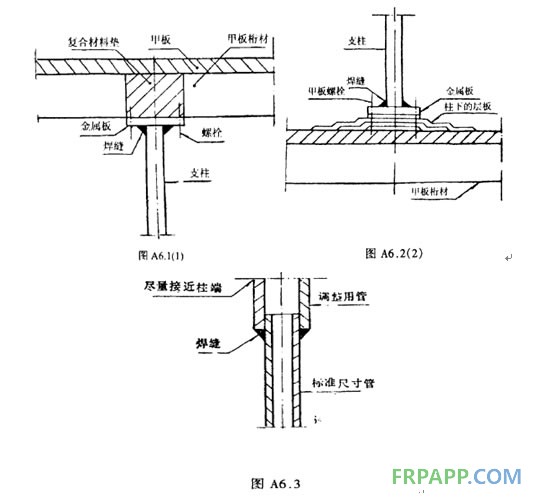
3.2.2.6穿过船壳的金属构件与船壳的连接
(1)在金属构件穿过船体壳板的部位,特别是如舵杆、尾轴架、轴系等位于水线以下的和有可能受到振动影响的部位,均应认真考虑,仔细设计。通常对这些部位应采用增加壳板厚度或增设扶强构件的方法予以加强。对由金属件引起垂直于壳板的作用力,应由增设的构件承受。图A7.1是一个金属构件穿过船体壳板的一个实例。先将一块板与穿过层板的金属构件焊在一起,然后装配到位,在层板的另一面套上一个垫环,用螺栓夹紧。
(2)所有的连接界面应精心加工,并符合装配要求。同时应选择适应金属和纤维增强塑料的树脂(也可加人增强材料),以保证连接后的强度和水密性。
3.2.2.7机座结构
(1)机座应安装在专门设计的基座纵析的构架上,并保证其具有良好的刚性,图A8.1给出了两种实用的机座结构形式。
(2)机座结构也可以采用在纤维增强塑料构件上加装金属帽的结构,见图A8.2所示。安装金属帽的螺栓处可以使用木质芯材。
(1)在金属构件穿过船体壳板的部位,特别是如舵杆、尾轴架、轴系等位于水线以下的和有可能受到振动影响的部位,均应认真考虑,仔细设计。通常对这些部位应采用增加壳板厚度或增设扶强构件的方法予以加强。对由金属件引起垂直于壳板的作用力,应由增设的构件承受。图A7.1是一个金属构件穿过船体壳板的一个实例。先将一块板与穿过层板的金属构件焊在一起,然后装配到位,在层板的另一面套上一个垫环,用螺栓夹紧。
(2)所有的连接界面应精心加工,并符合装配要求。同时应选择适应金属和纤维增强塑料的树脂(也可加人增强材料),以保证连接后的强度和水密性。
3.2.2.7机座结构
(1)机座应安装在专门设计的基座纵析的构架上,并保证其具有良好的刚性,图A8.1给出了两种实用的机座结构形式。
(2)机座结构也可以采用在纤维增强塑料构件上加装金属帽的结构,见图A8.2所示。安装金属帽的螺栓处可以使用木质芯材。
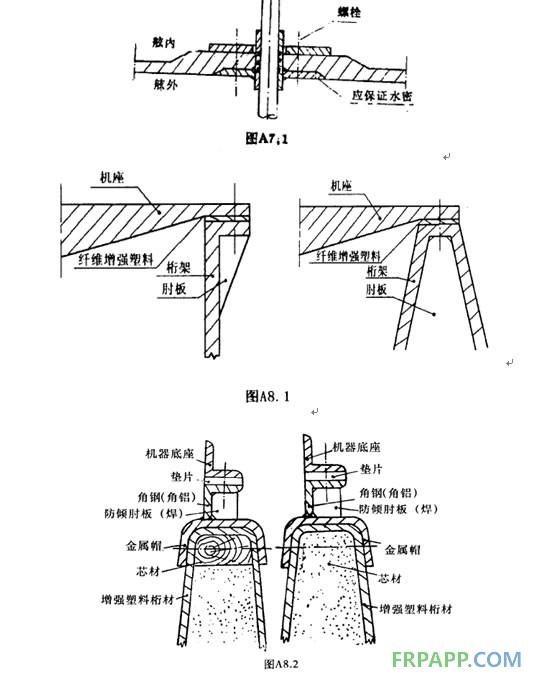