为更好的分析浇注系统对充模时间的影响,做假设如下:
(1)充模过程中,树脂粘度不变,不发生固化反应,真空压力不变。
(2)对浇口位置进行优化时,暂不考虑成型缺陷的影响。
(3)对于所有仿真模型,将抽气管沿艇舷铺设即将抽气口设置在充模流动的末端,以利于空气的排出和纤维的充分浸润。
3.4流道布置方式仿真分析
常用的浇注方式有三种:单向注射、中心注射以及周边注射。此类方式对大批量、小尺寸构件非常有效,但对于艇体这类尺寸大、形状复杂的构件
并不实用。通过实践摸索,在上述基本注射方式的基础上逐渐形成了几种多流道注射方式,用以大型结构件成型。主要有并行流道布置、鱼刺型流道布
置、混合流道布置。下面结合三种流道布置形式在艇体上的实际应用进行仿真分析,其中同一流道上两个浇注口间距设为1500mm,平行流道间距统一设为400mm。以下分析是在不改变x、y值的情况下,针对不同的流道布置方式对充模时间、成型质量、制造成本的影响进行研究。
3.4.1并行流道布置
并行流道布置是指流道平行于船体中线,沿船长方向布置,如图3-4所示。并行流道布置可通过改变两条平行流道间距来调节充模时间,对于形状复杂的构件适应性好。
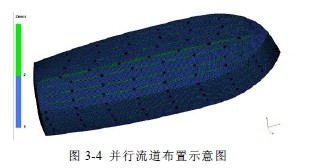
对采用并行流道布置的艇体进行充模仿真,充模时间云图如图3-5所示。从仿真结果可以看出,并行流道布置时的树脂流动前锋曲线比较平滑,从而降低了产生气泡、干斑等缺陷的概率,最终艇体成型质量相对较好。不足之处在于对于各个流道的开关时机控制要求较高,充模过程中必须时刻注意树脂相对下一条流道的位置。注射太早可能导致两个树脂流动前锋汇聚,造成千斑、气泡等缺陷,注射过晚,则会影响树脂充模进度。另外,并行流道设置耗材较多,人工成本也随之增大。

3.4.2鱼刺型流道布置
鱼刺形布置,顾名思义是流道布置形状如鱼刺一般。由图3-6可知,主流道铺设在艇体底部龙骨处,另有若干分流道沿船宽方向布置。鱼刺型布置只在龙骨主流道处设置浇注口,船宽方向的分流道只起到分流树脂的作用,浇口开关时机容易把握。
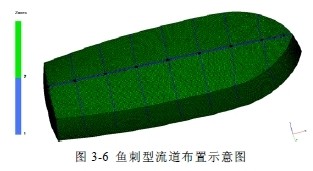
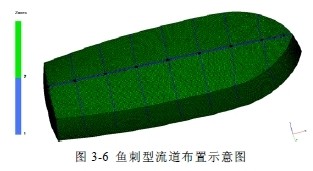
对鱼刺形流道布置进行充模仿真,充模时间云图如图3-7所示。该布置方式充模时间相对较短。需要注意的是,充模时主流道上的浇口必须同时打开,以防止船宽方向的分流道中树脂形成的流动前锋汇聚时形成气泡等缺陷。另外,由于艇体力学性能的需要,底部和侧面铺层方案不同,对应的渗透率也不相同。实际情况下,艇体侧面预成型体的渗透率略高于艇体底板预成型体的渗透率,树脂在艇体侧面的流动速度高于在艇体底板的流动速度。当树脂从底部流入侧面时速度加快,导致树脂过早的被抽入树脂采集器,而在艇体底部靠近侧面处形成缺陷,对于艇体的力学性能是非常不利的。



3.4.3混合型流道布置
混合流道布置是以上两种布置方式的结合。混合流道布置方式比较灵活,可分为艇底鱼刺型布置、艇侧并行布置和艇底并行布置、艇侧鱼刺型布置两种,如图3-8所示。混合布置方式继承了鱼刺型流道布置充模时间短的优点以及行流道树脂流动前锋平滑的特点,而且耗材适量,成本相对较低。
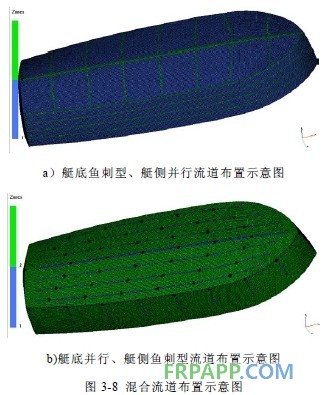
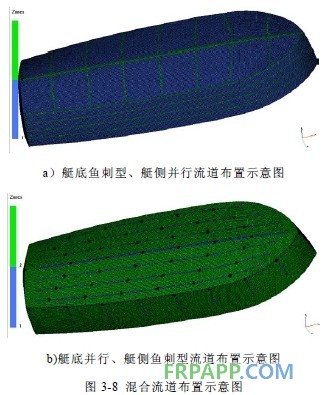
对混合布置的两种方式进行充模仿真,如图3-9所示。对于艇底鱼刺、艇侧并行的布置方式,当树脂流动前锋到达艇底与艇侧交界处时,相邻分流道之间有相当区域未被浸润。若此时打开下一流道,不同流道的树脂流动前锋交汇容易形成气泡,并且形成高压区,阻碍树脂流动。若不打开流道,则鱼刺型布置充模迅速的特点并未被充分利用。对于艇底并行、艇侧鱼刺的布置方式,通过艇底流道依次进行树脂注射,避免了树脂快速流出造成的浸渍不完全;而艇侧面的分流道则减小了重力对树脂流动的阻碍作用,发挥了其速度优势。
综合分析三种流道布置方式在艇体成型中的应用,本文选取混合布置方式进行流道铺设。其中艇体底层铺设并行流道,同时以舷侧与艇底结合处为主流道向艇体侧面铺设鱼刺型流道。
3.5浇口位置仿真与优化
在艇体真空导入成型充模过程中,浇口位置处压力为一个大气压,随着树脂流动前锋的向前推移,压力差逐渐变小,树脂充模时间迅速增加。为了防止树脂固化导致的填充不完全,应尽量缩短充模时间。显而易见的是流道越多、浇口越密集,充模时间相对越短,越有利于树脂的流动以及纤维的浸润。但是随着流道和浇口的增多,所需原材料和人工成本都会增加。特别是在真空导入成型的很多材料都需要从国外进口的情况下,流道和浇口数量的增多对整体经济效益的限制更加明显。因此,在保证树脂流动均匀,并完全浸润预成型体的情况下,应使每个浇口效益最大化,即使用最少的浇口,在合理的时间段内完成树脂对模腔的填充。
3.5.1浇口位置优化数学模型
为了便于优化,必须首先定义目标函数。目标函数应能体现优化参数对优化目标的影响,但这是很难量化的,通常需要通过经验来确定。本文以充模时间和成本为目标,对浇口间距进行优化,可以得到以下函数关系式:
T=f1 (X,Y)
c=f2 (X,Y)
其中T--充模时间;
C--成本。
值得注意的是,这里的成本不仅仅是单纯的经济成本,如材料和人工成本,还包括着操作复杂度比如管路铺覆复杂度和浇口控制复杂度等,所以成本在本文中是一个资金成本和复杂度的综合值。在浇口位置优化中,充模时间和工艺成本所占的权重不同,因此,最终的优化目标O如下式所示:
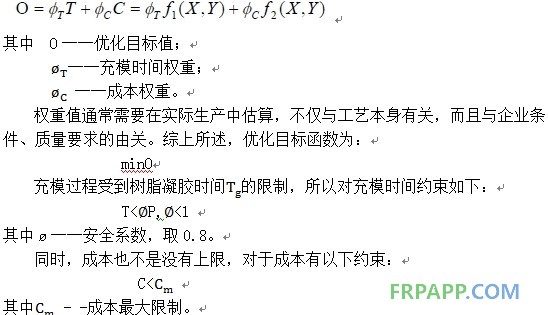
通过以上分析,式(3-4)、(3-5)、(3—6)一起组成了浇口位置优化的目标函数。
3.5.2浇口位置仿真
本节在采用艇底并行布置、艇侧鱼刺型布置的基础上,以最短充模时间和最小成本为目标,对不同的浇口间距进行仿真优化,得出最优浇口位置。浇口间距X,Y如图3-10所示,黑色边线表示艇体俯视框架,黄色线代表铺设的流道,红色三角形代表浇注口。根据实际生产中的经验值,取离散的X、Y为别为:X=1500,2000,2500,3000; Y=400,500,600,800,单位为毫米。可得浇口间距X、Y的组合共计1 6组。

[ 复材学院搜索 ]
[ 加入收藏 ]
[ 告诉好友 ]
[ 打印本文 ]
[ 违规举报 ]
[ 关闭窗口 ]

利用PAM-RTM对不同的浇口间距进行设置,现列出四组不同间距下的浇口布置示意图,如图3 -11所示;其中绿色区域表示导流布,蓝色狭窄区域表示用树脂管铺设的流道,圆点表示浇口。
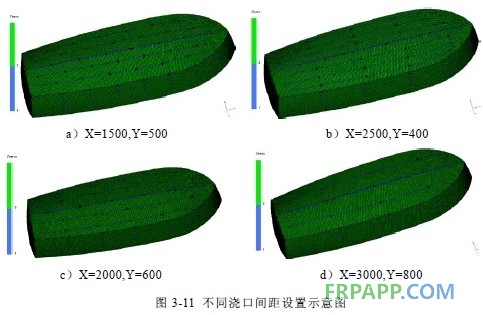

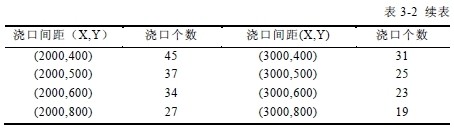
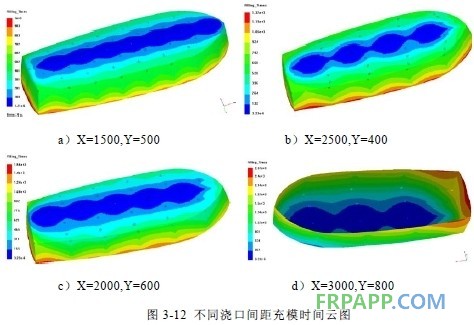
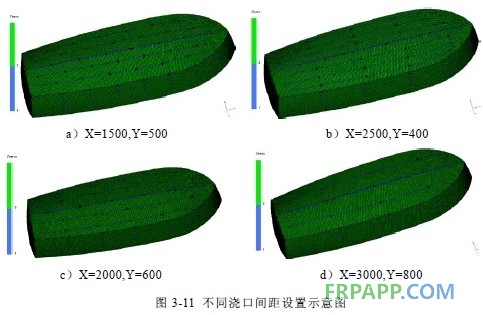
对于同一艇体模型,在不同浇口间距下,其浇口总个数如表3-2所示。

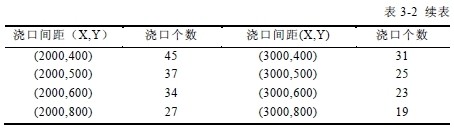
充模时,首先打开艇体龙骨处流道上的浇口控制开关开始注胶,当树脂流动前锋接近下一流道时触发传感器,此时关闭上一流道上的浇口,开启下一流道上的浇口。通过传感器自动控制不同流道上浇口的开关时机,逐步完成充模。由于篇幅有限,仅列出部分模型充模时间云图,如图3-12所示。可以看出不同浇口间距情况下,树脂流动前锋差别不大,但是充模时间有较大差别,说明浇口间距对充模时间的影响远大于流动前锋。
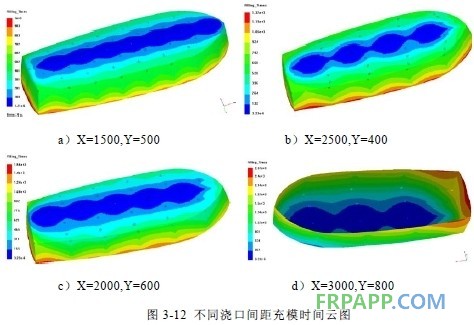
本次仿真所用树脂粘度为200cps,其凝胶时间为1800秒。根据仿真结果对不同浇口间距下的充模时间进行统计,结果如表3-3所示。由表可知X=3000,Y=600; X=2500,Y=800; X=3000,Y=800三种情况下,充模时间超出树脂凝胶时间,在实际生产中将会造成树脂无法完全填充模腔,导致艇体报废。分析其他浇口间距下的充模时间不难发现其时间差在宏观上并不大,但由于树脂凝胶时间的限制,对于艇体充模过程来说,必须分秒必争。越是尽快完成充模,越能降低浸渍不完全的风险。


- 下一篇:碳纤维复合材料在民用航空上的应用
- 上一篇:环氧树脂体系在风力机中的应用、回收与更新