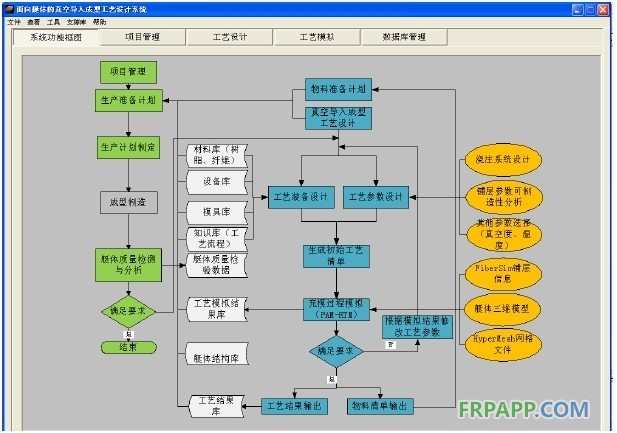
5.4.2工艺设计实例
本文以12m玻璃钢游艇真空导入成型工艺设计为例,演示系统运行过程。进入系统后,首先通过图5-4了解系统总体功能。然后进入项目管理项,其界面如图5-5所示。根据需要,可选择打开原有项目或建立新的项目。本节以新建项目为例对系统操作进行演示。在新建项目控件中输入项目名称、设计人员、校核人员并设置存储路径,以便确定系统生成的文件夹位置。然后,根据项目要求录入艇体基本信息,包括艇体全长、型宽、型深、法长、吃水、斜升角等数据。通过调用Pro.E建模软件完成艇体几何模型的建立,也可以直接导入存在的艇体模型。
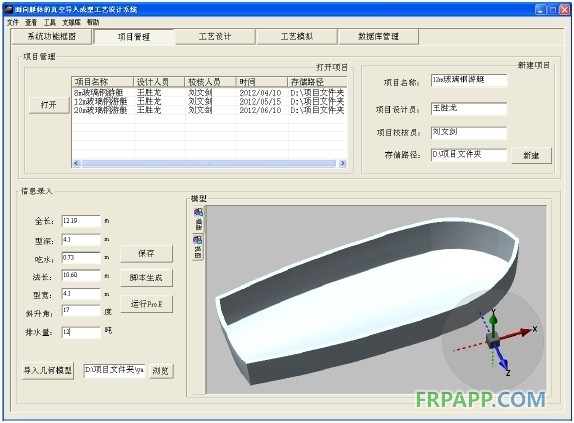
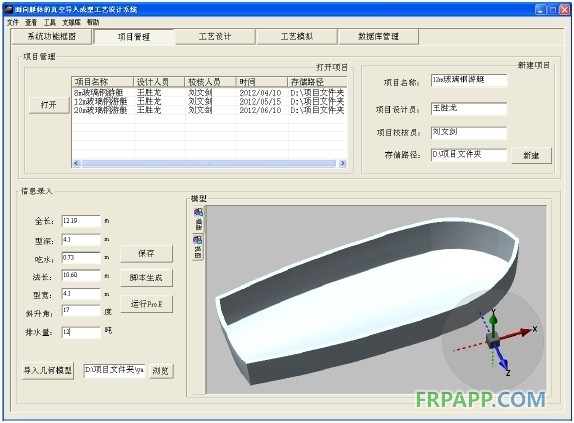
完成新项目的创建并录入艇体基本信息后,点击工艺设计项进行切换,此时系统窗口界面如图5-6所示。根据艇体真空导入成型工艺设计的需要,该界面主要分为四个部分:树脂设置、纤维设置、铺层结构、浇注系统设置。设计人员根据所了解的工艺知识及实践经验进行初步工艺设计。树脂设置中,可以根据需要设定树脂的粘度为常量或是时间、温度的函数。纤维设置中,对所用增强材料进行编号,并保存其厚度、密度等基本参数。铺层结构设置中,分别对艇体底部区域及艇体侧面区域进行铺层设置,包括每一层所用增强材料编号及其铺放角度。铺层为从模具开始按由下到上的顺序进行铺设。浇注系统设置中,可根据艇体尺寸和形状,结合以往设计经验,选择道布置形式和浇口间距,并导入浇注系统设置模型,以更直观的观察流道和浇口分布。图5-6所示为混合流道布置情况下,X=1500,Y=400时的浇注系统设置。
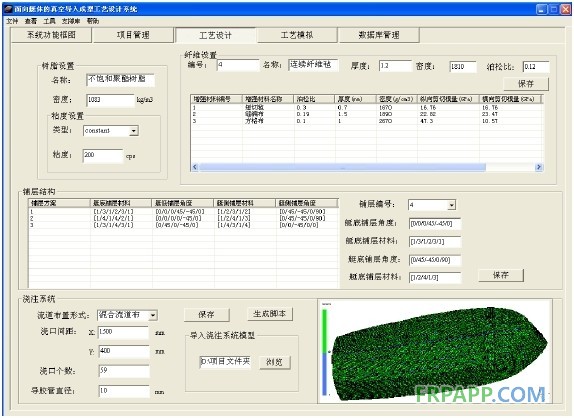
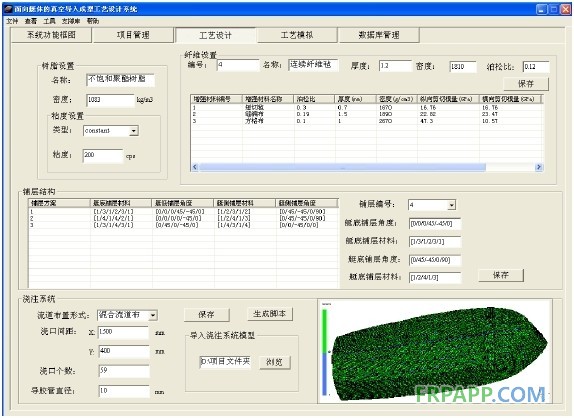
点击工艺模拟项,利用工艺设计项初步设计的工艺参数进行仿真,以验证是否正确,并对存在的缺陷进行更改。工艺模拟项分为两个部分:仿真参数设置、仿真结果查看。
仿真参数设置主要是根据实际生产环境,设置成型温度及真空度,并根据工艺设计中的铺层方案,调用渗透率计算模块得出艇体底板和艇体侧面的渗透率。完成上述参数设置后,点击“生成仿真脚本”,可以得到实现艇体充模过程仿真功能的软件脚本。然后,可以进一步对脚本文件进行检查,分析其材料属性、真空压力、浇注系统设置。检查无误后,开始进行工艺仿真。仿真结果查看部分可以根据需要调出仿真所得的充模过程、充模时间、压力分布、温度分布的云图,并对成型结果进行评价。根据对模拟结果的分析评判此工艺参数下的成型质量能否满足要求,选择生成工序表或返回工艺设计项,针对所存在问题重新修改工艺参数,直到仿真结果满足要求。图5-7所示为充模时间云图,分析可知参数设置中存在问题,使其充模时间远远超过树脂凝胶时间。可通过检查工艺参数设置,重新进行模拟,直到成型质量达标。
以上就是面向艇体的真空导入成型工艺设计系统进行工作的完整实例,完成了艇体成型工艺设计及仿真的任务。
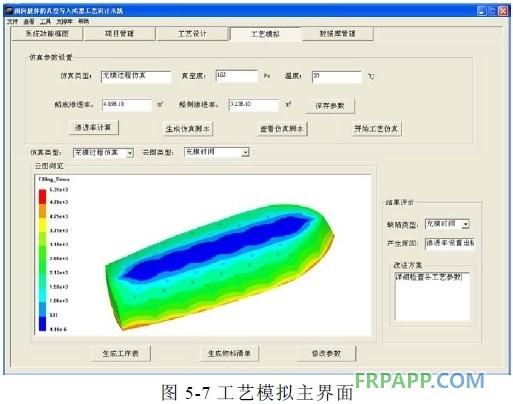
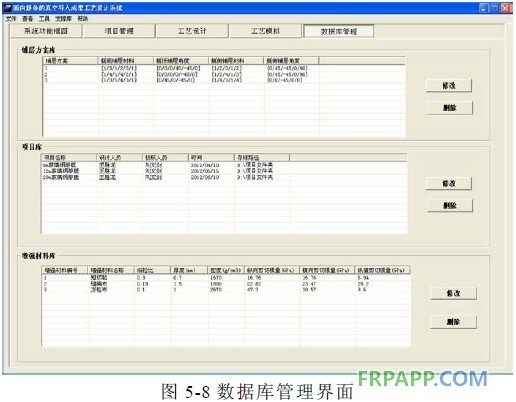
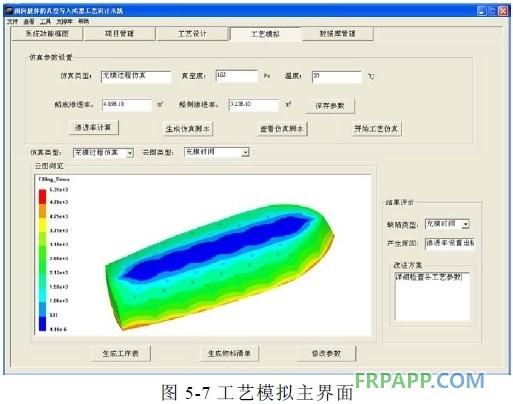
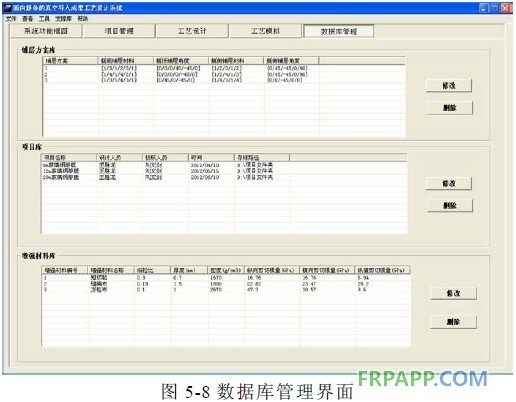
此外,数据库管理项是面向艇体真空导入成型工艺设计系统不可或缺的一部分。其主要工作是对工艺设计中所建立的项目文件库、材料库、铺层方案库、工艺知识库进行管理,包括修改、删除等操作。其界面如图5-8所示。
5.5本章小结
本章完成了面向艇体的真空导入成型工艺设计系统的软件结构的构建。介绍了软件系统主类的工作关系,并对系统与外部CAD/CAE软件之间的数据交换问题进行研究,设置了系统文件的存储路径。最后,结合艇体真空导入成型工艺设计实例介绍了系统工作过程,验证了系统的可行性。
结 论
针对艇体真空导入成型工艺中存在工艺设计效率低、成型周期长、成本高等问题,本论文以山东省中复西港艇体有限公司生产的12m玻璃钢游艇为例,对艇体真空导入成型工艺进行分析,对成型过程中非常关键的浇注系统和铺层方案进行优化,并将计算机辅助工艺设计技术应用于艇体真空导入成型工艺设计。主要工作如下:
(1)结合真空导入成型工艺的原理,对实际生产中的艇体真空导入成型过程进行了细致分析,并建立了充模过程的数学模型。分析了工艺参数对成型过程和成型质量的影响;列出了常见成型缺陷产生的原因,并给出了不完全填充、气泡、干斑等缺陷的初步解决方案;得出了树脂、增强材料、真空袋膜等成型材料的选择原则。构建了面向艇体的真空导入成型工艺设计系统功能框架,并设置其工作过程。
(2)利用Pro.E建立了12m玻璃钢游艇的三维模型,模型简化后,利用HyperMesh进行了三角形网格单元的划分。对并行流道布置、鱼刺型流道布置、混合流道布置这三种流道布置方式进行仿真,从充模时间、成型质量、制造成本等角度比较得出最佳流道布置。根据实际生产经验,在一定范围内离散的选择了1 6组不同浇口间距布置,进行充模仿真,并利用插值拟合,以最短充模时间和最小成本为目标得出最优浇口位置。
(3)分析了常用增强材料的性能,并建立了导流布和增强材料预成型体的渗透率求解模型。针对艇体不同区域铺层结构并不完全相同的特点,对不同铺层方案进行仿真,分析仿真结果及其产生的缺陷,比较之后得出合理铺层方案。
(4)建立了面向艇体的真空导入成型工艺设计系统的软件结构,以Visual C++为平台实现了外部支撑软件的集成,完成了系统实现,并进行了实例验证。
通过本课题的研究的进一步研究方向如下:
通过本课题的研究的进一步研究方向如下:
(1)由于质量检测技术的限制,真空导入成型工艺在厚度较大艇体的成型方面受到很大限制,其检测技术亟需改进。
(2)由于时间限制,本文实现的面向艇体的真空导入成型工艺设计系统只是一个原型系统,系统功能以及工艺知识库还需进一步改进完善。