1.SMC的制备
(1)SMC的生产设备
SMC生产主体上分为两部分:一部分是树脂糊的制备设备,它包括投料、混合、输送三个过程。一部分是制片设备,它包括上糊、粗纱切割、浸渍压实和收卷。本部分主要介绍SMC制片设备。
一个完整的SMC机组,大体由机架、输送系统、PE薄膜供给装置、刮刀、玻璃纤维切割器、浸渍和压实装置、收卷装置等7个主要部分和玻璃纤维纱架、树脂糊的制备及喂入系统、静电消除器等3个必备辅助系统组成。
SMC机组组成如下示意图所示。SMC机组典型照片如图所示,典型SMC机组参数如表所示。
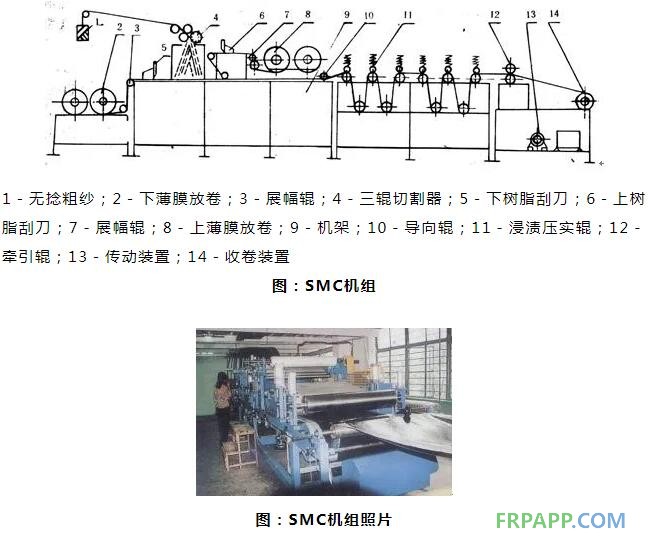
表:典型SMC机组参数
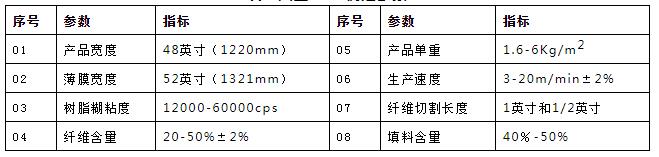
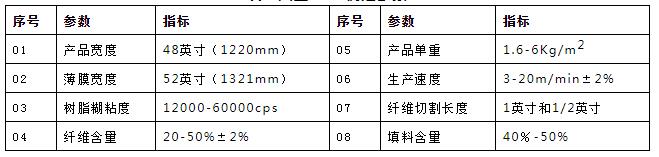
(a)机架
一般都用各种型钢(如角钢、槽钢等)焊接或用螺栓连接而成,它的主要作用是安装输送系统和各种部件。为防止在各种静载荷、动载荷下的变形,机架应有足够的刚性,并且在新结构设计中,往往应在机架上留有备用空间。
(b)输送系统
一般有两种类型,一种是输送带,一种是直接用聚乙烯(PE)膜兼起输送带作用。输送带运动轨迹控制装置,在机组设计时要特别注意。
(c)PE膜供给装置
PE膜供给装置应保证在生产过程中有充足的薄膜供应,确保薄膜在有可调张力的情况下,无皱褶地进入上糊区。在机组中一般设有两套供膜装置,而每套能同时安装两卷薄膜,以便在一卷薄膜用完后,另一卷备用薄膜能立即投入使用而不会引起生产过程的停顿。
(d)刮刀装置
在机组上糊区,安有两个刮刀装置。其主要作用是随着薄膜在刮刀及其底板间通过时,均匀地将可控数量的树脂糊施加到PE膜上。刮刀应容易调节且调节精度要高,刮刀与底板间的间隙要均匀,误差应在0.05mm以下。为防止树脂糊中结块或外部杂质进入刮糊区引起薄膜的扯裂,刮刀底板或刮刀可实现临时性的瞬间下降。设计时,还应使刮刀刃部的半径尽可能小。
(e)玻璃纤维切割
在许多较早设计的机组中,切割器单独安装在另一个机器上,当改用玻璃纤维毡时,设备不必做过大的改动就能生产。但是,目前由于价格和性能方面的原因,已很少使用毡作SMC的增强材料,因此切割器大多直接固定在主机架上。玻璃纤维由切割器切断。切割器为三辊式结构,如图43.178所示。连续玻璃纤维从纱架引出,经纱线横动杆2进入压辊5与橡胶包覆的支承辊3之间后,由于两辊的牵引,纤维被导入转动的支承辊与切割辊8之间,被切成短切玻璃纤维。
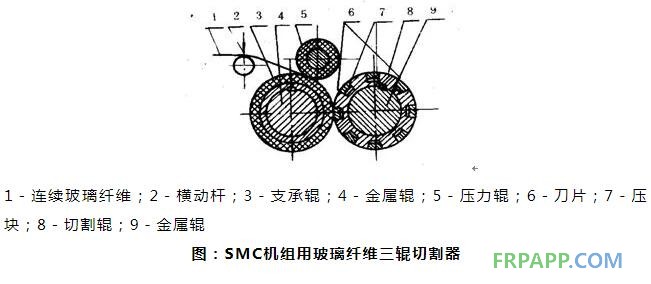
(f)浸渍与压实装置
浸渍与压实装置由一系列光辊和槽辊组成,在个别机组中还加有刺穿辊。它们的作用是实现SMC片材的复合、浸渍、脱泡和压实,槽辊的使用可以强化浸渍,而且避免发生在浸渍压力下树脂糊外流现象。在浸渍压实区,各种辊的压力可采用气体或液体加压,该区尾部的压实辊,还起到调节片材厚度的作用。在SMC机组中,浸渍、脱泡、压实主要靠各种辊及片材自身所产生的弯曲、延伸、压缩和揉捏等作用实现的。为使纤维被树脂浸透、驱赶气泡和使片材模塑料压实成均匀的厚度,机组中有两种浸渍压实结构,即多辊筒的环槽压辊式与输送带的弯曲双带式,如图及图所示。
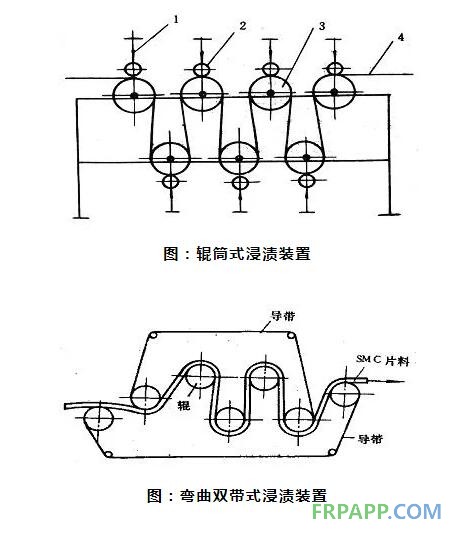
(g)收卷装置
收卷装置的作用,就是将经过浸渍的SMC收集成卷。对于试验性机组或小批量生产机组,一般采用双轴双位转台式收卷装置,这种装置可在生产过程中实现换卷。
(2)SMC的生产工艺
SMC片材的制备主要由如下几个部分组成:
(a)树脂糊制备及上糊过程.
树脂糊的制备方法有3种:
a)批混合法 此法是把增稠剂以外的各种材料按比例加入反应釜中,以一种糊状混合物的形式使用。在上SMC机组前加入增稠剂。增稠剂加入后,通常在30分钟内使用完。
b)批混合/连续混合法 该工艺的特点是用两个混料釜系统混合。一个装不饱和聚酯树脂、低收缩添加剂、引发剂、脱模剂和填料,另外一个釜里装载体树脂、着色剂、增稠剂。生产时,用计量泵通过混合器进行混合。
c)连续混合法 配方中的所有液体或固体的计量、运输、混合全部实现机械机械化和自动化。此系统装置投资费用大,适合连续大批量生产。
(b)浸渍过程
浸渍过程的目的是使树脂浸透纤维、驱赶气泡、使片材压紧。为此,SMC机组中排列了各种类型的辊(光辊、槽辊、穿刺辊及螺旋辊等)。当片材从这些辊的上部、下部及周围经过时,因受到弯曲延伸作用而实现浸渍。
(c)增稠过程与存放过程
当SMC片材收卷完成后,一般要经过一定的增稠时间后才能使用。如SMC片材在室温下存放,大约需要1~2周。在40℃稠化需要48小时或72小时。目前也有在SMC机组上增设增稠区域或采用一些新型的增稠剂,SMC制备成片材后即可进行压制。
片材的储存期与储存状态和条件有关。环境温度对SMC片材的储存期有明显的影响。以英国的SCOTT BARD公司生产的片材为例,它在15℃以下的储存期为3个月;在2~3℃的储存期为6个月。片材的储存期也与配方有关。如配方中加入阻聚剂,储存期就会长一些。
(3)SMC的生产过程控制
如上所述,SMC是由多种组分经专门的设备复合而成。从原材料方面看,它既有有机材料又有无机材料;既有固体材料又有液体材料;既有粉体材料又有纤维材料,而且各组分复合在一起的时候开始,系统会产生各种各样的物理和化学的变化。在其生产过程中,有很多因素,如材料因素、设备因素、人为因素等都会影响到生产的过程和最终产品的质量。因此,只有从整个生产系统包括从使用角度来考虑片状模塑料的全面质量管理,才能得到一个质量良好、相当稳定的片状模塑料产品。
一般而言,SMC制造的质量管理由二部分组成,即原材料进厂质量管理、SMC生产工艺过程管理。
(a)原材料的质量管理
SMC生产用原材料主要包括不饱和聚酯树脂、低收缩添加剂、苯乙烯单体、填料、玻璃纤维、内脱模剂、引发剂、色浆、化学增稠剂等,需要控制的项目列于表。
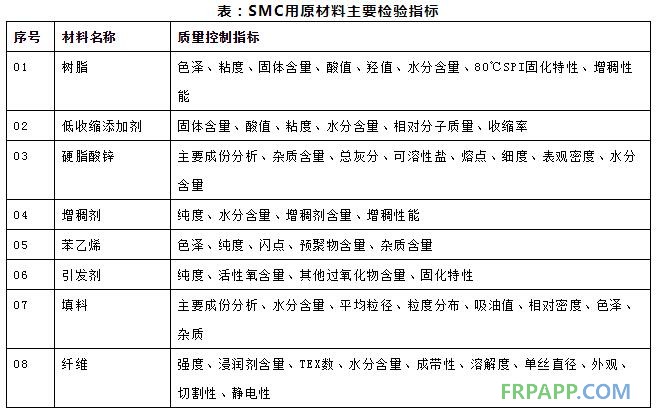
需要强调的是上表中列出的项目并不是需要逐项测试。在整个SMC片材生产过程中尤其需要注意严格控制体系的含水量,尤其是原材料体系的水分含量。
(b)SMC工艺质量管理
SMC生产过程包括如下步骤:投料、混合、树脂糊的输送与涂敷、 纤维输送与切割、复合与浸渍、收卷与计量、熟化。后续按照SMC工艺控制和质量控制两方面进行描述。
a)SMC工艺控制
在线的伽玛射线测试装置持续测量载体薄膜上的SMC/BMC树脂糊的厚度,保持载体薄膜上的SMC/BMC树脂糊的厚度一致(在宽度方向,SMC糊分布均匀一致,没有偏差),保持玻纤分布均匀及稳定的玻纤含量( 2%);
通过裁剪SMC并称重的方法在SMC宽度方向的不同位置处测量单位面积SMC的重量;在生产开始时,生产过程中间以及生产结束时分别测量单位面积SMC的重量(控制SMC厚度均匀的一种方法);
在更换树脂及使用新的批次的填料时应测试树脂糊的粘度和温度;将SMC贮存在恒定和受控的环境中,即较高温度的熟化室(如28℃)和较低温度的贮存室(如18℃);为了控制SMC/BMC糊的粘度增长,生产中需将SMC/BMC树脂糊样品贮存在SMC/BMC熟化室,并按规定使用布氏粘度计测量SMC/BMC树脂糊的增稠情况;在添加原料如树脂、填料、助剂、氧化镁糊时添加量要准确。
b)SMC质量测试
用放热试验设备测试SMC的反应性,如没有反应性测试仪,通过热电偶测量平板成型过程中的温度随时间的变化曲线;测量平板的收缩率;用塑化仪测试SMC的稠度(塑性程度),该方法非常适合于相同配方SMC的生产监控,如果生产中所用的纤维有变化,测试结果就会不同。
(4)SMC生产过程中常见问题及解决方法
表:列出了SMC片材生产过程中的常见问题、产生原因及解决方法。
表:SMC生产过程中常见问题及解决方法
表:SMC生产过程中常见问题及解决方法