一、层压设备
主要设备为热压机组。辅助设备有装卸机、模板回转机、模板清洗机、铺模清理机(叠铺机)等设备。从生产组合上分单机热压、冷却和两台热压、冷却机。
目前国内外使用的热压机有2种:开式压制热压机和封闭真空热压机。与开式热压机相比,真空热压机具有两个突出优点:①成型单位压力低1/2-1/3,即降低胶的流动,布的经纬线移动小,降低层压板的内应力,最终达到降低翘曲度的目的;②可避免板内和边角产生气泡,产品的质量较高;真空热压在复合材料成型中的应用越来越广泛。
热压机的性能和控制水平直接影响产品的质量,同时与成型工艺有直接关系。热压机主要控制加热板的温度场和压力。
1.加热板
加热板的结构和所使用的热介质直接影响加热板的温度场的均匀性、板面温度的均匀性、胶布胶熔化的均匀性,以及胶化后产生的气体和胶布层间的空气的排出。因此加热板升温速度要快且均匀,板面温度差应小于3℃。
加热板的通道有单进单出和双进双出两种。后者制造复杂,配管也复杂,成本高,一般很少采用。前者采用蒸汽加热,板面温度差较大(大约5℃);当采用热水或导热油时,板面温度差低于3℃;采用导热油效果更好,因为导热油的压力低(小于0.5MPa)、温度高(可达300℃左右)。
对整机温度控制,一般热压机开口12-20个,这样加热板从下而上呈现温度梯度。蒸汽加热为单点总控较多,梯度大约5℃左右。热水或导热油一般采用分区(一般分2-3个区)控制,温度梯度只是控制误差低于3℃,这样有利于在同一压力下,上、中、下的固化速度相同,有利于提高产品质量。
2.压力
目前热压大都采用液压机,可满足产品成型所需的单位压力,最高可达12.5MPa,压力稳定小于±500KPa,可根据工艺要求设定。多层压机的吨位一般较大,通常为2000-3000t。图5-6为2800吨多层压机实物图。
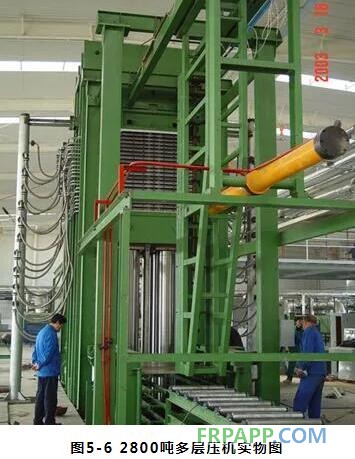
二、层压工艺过程
1.胶布裁剪、配迭
胶布裁剪是将胶布剪成一定尺寸(按压机大小),剪切设备可用连续定长切片机,也可以手工裁剪。胶布的剪切要求尺寸准确,不能过长或过短。将剪好的胶布整齐叠放,把不同含胶量及流动性的胶布分别堆放,做好记号储存备用。为了尽可能地避免胶布挥发份的增加及可溶性树脂含量的降低,胶布应贮存在干燥室内。
不同用途浸胶布的裁剪方式也不同:用于层压的胶布按生产规格进行裁剪,同时留有加工毛边的余量;用于布带缠绕的胶布则先把胶布切割成缠绕成型所要求的胶布带,然后通过缝纫搭接、倒盘、卷成一定直径的胶布带盘使用。
胶布配迭工序对层压板的质量好坏至关重要,如配迭不当会发生层压板裂开、表面花麻等弊病。所以在具体操作中应注意如下几点:
1)在配迭板材的面层,每面应放2~3张表面胶布,其含胶量和流动性应比里布略高。
2)挥发物含量不宜太大。如果挥发物含量太大,应干燥处理后再用;否则会影响制品的电性能、耐热性,易产生边角气泡及花麻。
3)配迭的计算。要使压制的板材厚度准确,一般采用质量法确定板材的胶布用量。每块板材所需胶布(或胶纸)材料的质量与层压板的厚度、面积、成板后的密度及成板后切去废边率的因素有关。
计算公式p=Fhd×(1+a)/1000
式中p—需要层压胶布(纸)的总质量,g;
F—压制板材的面积,cm2;
h—压制板材的厚度,cm;
d—成品板的密度,g/ cm3;
a—修正系数。
密度在压制布质、纸质板时按1.40~1.45;环氧酚醛玻璃布板按1.65~1.70计算(视含胶量和浸渍材料的坯重而定)。α的大小视成品板厚度而定,h<5mm时,α取0.02~0.03,h>5mm时,α取0.03~0.08。
大面积的层压板可先取几张胶布(纸),称取质量,确定1mm所需胶布(纸)的厚度,然后视要求厚度点清张数。
2.热压工艺
将装料车的组合推入多层压机的热板中间,热板缓缓上升,闭合后加压通入蒸汽压制。
压制工艺中的关键是确定工艺参数,其中最重要的参数是温度、压力和时间。压力制度首先取决于物料的品种和性质,其次考虑制品的厚度、板面积和设备条件。
1)温度
一般压制工艺的升温过程可分为5个阶段,如图5-7所示。
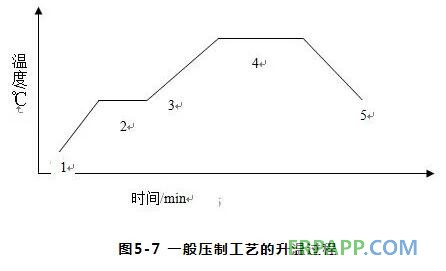
第一阶段是从室温升到物料显著反应温度,即预热阶段。此时树脂熔化并排出部分挥发物,压力一般为全压力的1/3~1/2。
第二阶段是中间保温阶段。这时树脂熔化、渗透,反应速度较低。保温时间根据胶布老嫩程度和制品板的厚度而定。当流出树脂接近凝胶化并拉长丝时,应加大压力并升温。
第三阶段为升温阶段。这是为了提高树脂固化程度。此时,树脂反应速度加快。
第四阶段为保温阶段,目的是使树脂充分固化,该温度取决于树脂的固化特性,而固化时间则取决于板材的厚度。
最后阶段为冷却阶段,达到保温阶段终点即可停止加热,然后缓慢冷却,并保持所需的最高压力。冷却速度对制品表面的平整度有影响,应控制冷却速度,开始冷却时不宜过快,降至50℃以下时才脱模。
2)压力
压力的作用是用来克服挥发物的蒸汽压,使粘结树脂流动,使胶布层间密切接触,防止板材冷却时变形。
成型压力的大小根据根据树脂的固化特性确定。固化时若有小分子物逸出,压力应大一些;树脂固化温度高时,成型压力也要相应增大。成型压力的大小还需考虑制品的厚度、胶布的含胶量和升温速率等因素。
几种常见的玻璃布层压板的工艺参数见表5-7。
表5-7 几种层压板材的热压制度
3)时间
从预热加压开始到取出制品为止的时间即压制时间,它是预压、热压和冷却时间之和,压制时间与树脂的固化速度,层压板的厚度和压制温度有关,以层压板能否被充分固化为依据。
预压时间取决于胶布的性能,若胶布的不溶性树脂含量高,挥发份含量低,则预压时间就短,反之要相对延长。热压时间以保证胶布中树脂充分固化,太短则树脂固化不完全,太长则是制品性能下降,需要通过反复试验来确定。冷却时间是保证产品质量的最后一个环节,冷却时间过短则容易使产品产生翘曲、开裂等现象;太长则降低生产效率。
3.冷却脱模
保温结束后即可关闭热源,自然降温或采用冷风、冷水等冷却,但不应过早降压,否则会使产品表面起泡或产生翘曲现象。脱模温度一般低于60℃。
4.后处理
后处理的目的是使树脂进一步固化直到完全固化,同时部分消除制品内的应力,提高制品的性能。环氧板、环氧酚醛板的后处理是在120~130℃温度的环境中持续120~150分钟,这样可提高制品的机械性能和电气性能。
三、层压板性能
几种典型层压板产品的部分性能见表5-8。
表5-8 几种典型层压板产品的部分性能
四、制品缺陷的分析及对策
以胶布为原料的层压板在生产中可能出现如下主要质量问题见表5-9。
表5-9 层压板常见质量问题及解决措施
实际生产时出现的问题还远不止这些,应针对不同问题具体分析,作出正确判断,不断总结,问题是可以解决的。