1、采用复合材料作为模具主体长18m*宽15m),使模具表面精度误差不超过均方根±0.3
2、使模具材料费用及加工费用比金属模具大幅度降低,约在30%左右,制造周期算短到3个月。
3、模具表面光洁度不低于水砂1000目,表面无缺陷。
4、模具整体耐温不低于--40—+80度。
5、模具真空度不低于0.098MPa.
6、模具适合远距离运输,拆装方便。
一、技术方案
目前国内外反射面模具多采用纯金属模具。金属模具制作成本相当昂贵,制造周期长,成本高。根据天线模具的特点:体积庞大,精度要求高,硬度要求高,双曲线外表面粗糙度高。要求周期短,成本低,重量降低。所以已经不适合再采用金属制造模具了。
目前国内外反射面模具多采用纯金属模具。金属模具制作成本相当昂贵,制造周期长,成本高。根据天线模具的特点:体积庞大,精度要求高,硬度要求高,双曲线外表面粗糙度高。要求周期短,成本低,重量降低。所以已经不适合再采用金属制造模具了。
二、技术方案
根据该项目的标准要求和技术特征,总体的思路和技术方案采用以下几部分:
1、将庞大体积分解成N个小单元,其每个单元的外框尺寸控制在20米*5米以内。已便于小单元金属部分整体退火消除应力处理。
2、在金属层面上采用特殊工艺制作复合材料层。
3、复合材料层在数控加工中心上做初加工处理。
4、在初加工的型面上做玻璃钢转化温度处理。
5、复合材料层做转化温度处理后,二次精加工。
6、小单元双曲线表面照相检测均方根运算处理。
7、N个小单元运输到现场组装调试。采用特殊工艺将调试后的N个小单元粘接 在一起。要求粘接牢固,整体型面准确,不能存在任何微孔透气现象。
6、小单元双曲线表面照相检测均方根运算处理。
7、N个小单元运输到现场组装调试。采用特殊工艺将调试后的N个小单元粘接 在一起。要求粘接牢固,整体型面准确,不能存在任何微孔透气现象。
8、整体型面做硬度测试,玻璃钢转化温度测试,整体型面均方根检测。
在总体思路和技术方案经过反复推敲论证后,做了大量的各种材料试验和缩比样件模拟实验。凭借项目组工程技术人员多年做复合材料所积累的经验,整个项目在实施的过程中基本达到预期效果,满足项目所要求的各项技术指标和经济指标。
模具说明
一、模具钢架分区

模具说明
一、模具钢架分区

沿长轴方向分成四个区域(三个结合面)
1、组装后结合面为最少,有利于区域之间密封,能够保证产品制作当中的真空度。
2、钢架沿短轴方向为一个整体,便于组装,减少多区域所产生的累积误差。
一、模具钢架分区
3、钢架退火处理满足退火炉的标准,单个钢架的最大尺寸15.662米x5.2米x2.85米。退火炉的有效尺寸16米x6米x6米。
4、满足汽运大件标准,不会在长途运输中出现麻烦。
5、钢架最大尺寸在CNC加工中心的有效范围之内。
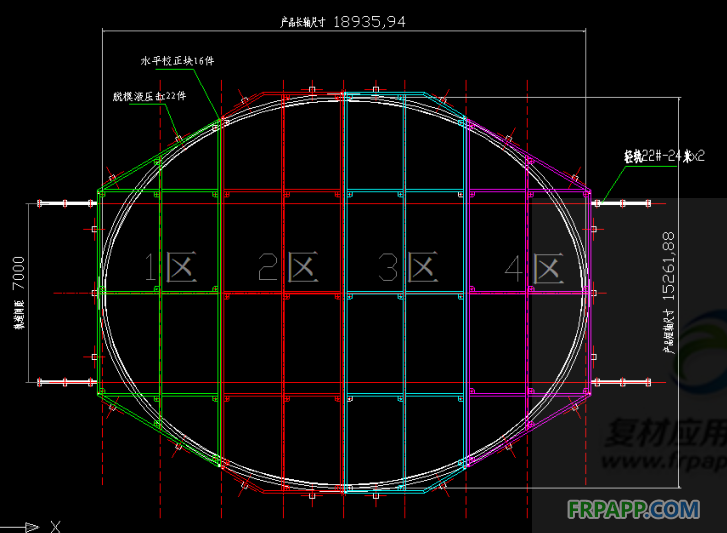

二、模具钢架的组成
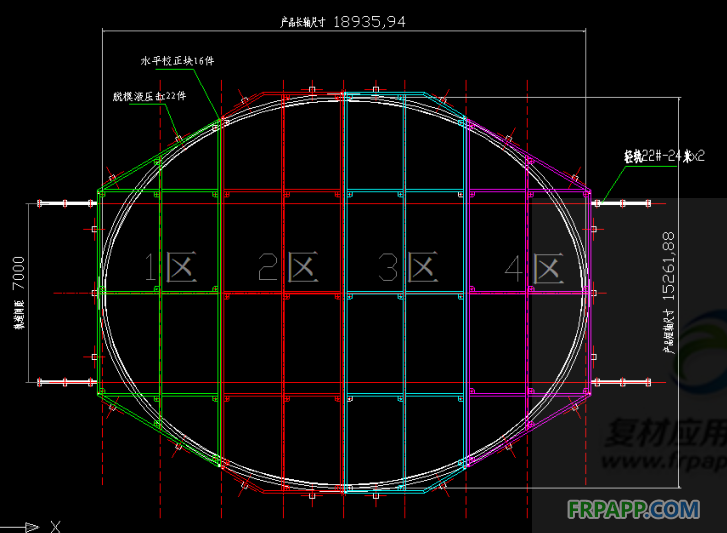

二、模具钢架的组成
主梁立柱采用100x100x5方管焊接。
斜支撑采用60x60x4方管焊接。
钢隔板采用6mm热轧钢板,数模激光切割。
钢隔板之间采用30x30x3方管斜交叉焊接。
型面采用20x20x1.5方管机器折弯做型焊接。
钢架高低差部位均有16mm厚三角筋板支撑焊接,以防止钢架焊接过程中的变形。
考虑到钢架焊接后的收缩变形,钢架下料已预留出千分之0.2-0.3余量。
每个区域的钢架均匀有15-16个地脚板,通过调整螺栓来校平钢架。
三、钢架的连接与定位
在每个区域钢架的结合面两端设有两组带有销钉孔的连接板。在模具最终组装后,来确定销钉孔的最后尺寸。为今后拆装模具带来方便。
在每个区域钢架结合面的其它位置上下均匀设有数个带有连接螺栓的连接板,用来调整两组钢架的紧密程度。
模具水平方向定位,由每个区域四个角处的铝合金定位块为依据,来调整水平。铝合金定位块是在数控加工中心上,与型面一同加
工的。



四、模具脱模与吊装
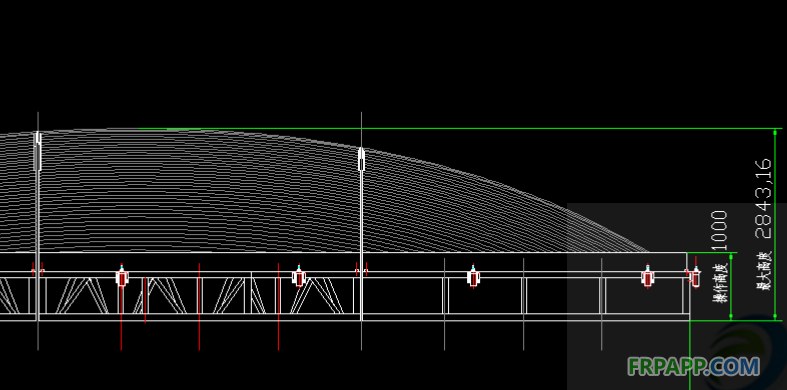
四、模具脱模与吊装
沿模具圆周设有22个液压缸,有一套液压控制系统控制。保证液压缸动作的一致性。
单个液压缸的最大挺起力为1吨(单位压力25kg/cm 2 )
在每个区域模具的两端分别设有两个吊点,需要采用
两部行车或吊车来起吊。

