1.机械加工
(1)切割加工
SMC制品的切割加工方法有手工切割、机械切割、高压水切割。
(a)手工切割
SMC制品的手工加工作业是非常多的。常用的使用工具有刮刀、锉刀、钢锯、刻刀、纱带抛光机、砂轮打磨机、金刚石研磨盘、钻头等。根据加工部分是平面还是曲面,是切断还是切削等不同情况分别使用。常用的手动切割工具如图所示。常见的手工切割工作内容如图所示。
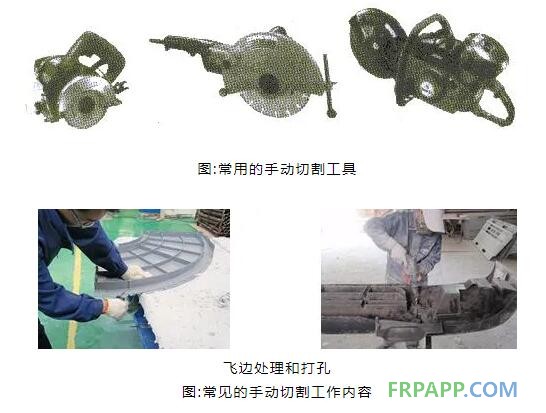
(b)机械切割
如图为顺切和逆切示意图。在各种切割形式中,顺切效果要比逆切效果好得多。原因在于:逆切时工件的进给方向与刀具的切割方向相反,刀具切入工件后,最终在A点切割上表面,使纤维首先被扯起,然后才撕开,从而在工作表面产生纤维隆起现象。顺切时,工件的进给方向与刀具的旋转方向一致。刀具在B点开始进入工件,显然最上层材料受到向下压的切割分力作用,因此,不会产生逆切时的纤维隆起。

(c)高压水射流切割技术
高压水射流的原理是将水通过增压器,使系统压力增加到400MPa再由蓝宝石喷嘴(孔直径为0.2 mm )喷出,形成喷射速度高于音速的高压切割水流,可对各种复合材料进行切割和开孔。高压水射流切割的优点:切缝窄、切割不发热、无粉尘飞扬、工作环境不受污染、工件无变形等。高压水射流一般分为高压水射流和磨料水射流两种。高压水射流是指形成射流的工作介质由水和磨料组成,其中水作为载体使磨料获得足够的动能,对被切割件进行磨削和冲蚀。其切割系统流程图如图43.33所示,高压水射流切割设备图如图,切割范围如表所示。
表:切割厚度范围
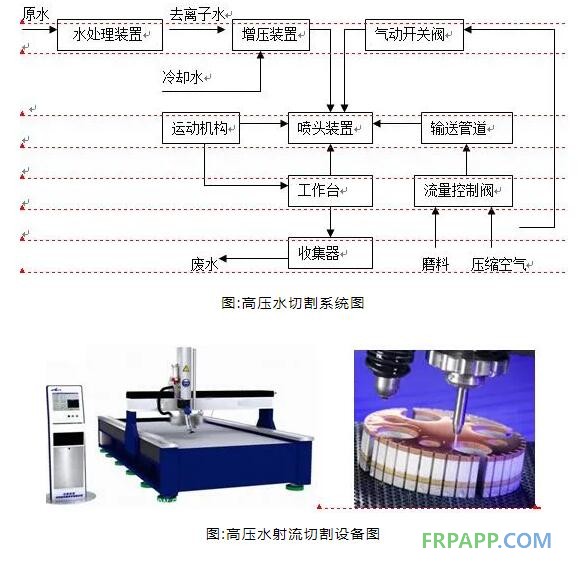
(2)打孔
在复合材料构件的连接中,机械连接占据着主要地位。当复合材料构件装配时,需加工出许多紧固件孔。SMC打孔的方法主要有手枪钻加工、数控加工中心加工和机器人加工。典型手枪钻加工照片如图43.35所示、数控加工中心照片如图所示、机器人加工中心如图所示。
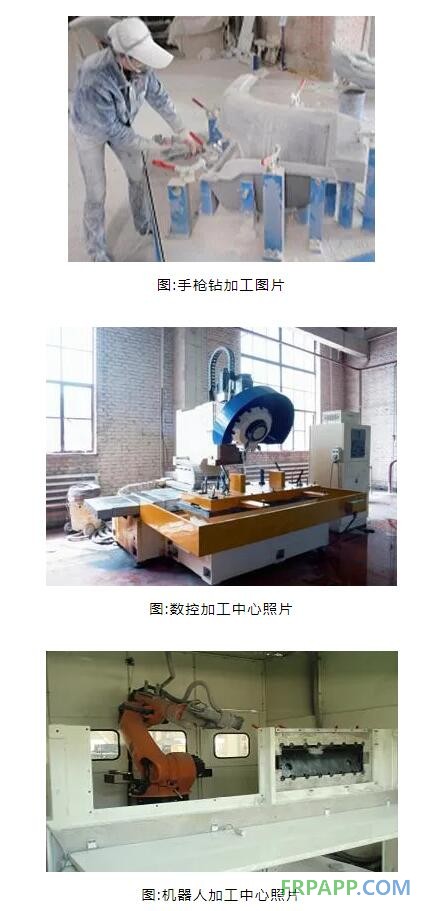
2.连接设计
通常用于金属结构部件之间的两种主要连接方法,即机械紧固件连接和胶接连接也适用于复合材料的连接。SMC/BMC与一般金属材料的区别是:层间强度低、在连接部位的应力集中或应变集中严重,在此区域载荷重新分配的能力较弱。对复合材料的连接进行分析和正确设计,是保证结构连接成功的首要条件。
(1)聚酯模塑料机械连接技术
聚酯模塑料的机械连接方式一般有金属螺纹及嵌件连接、螺栓(螺钉)连接、铆接。聚酯模塑料的常用机械连接方式如图所示。

适用于聚酯模塑料的专用结构件,在安装时必须满足一些特殊要求。只有这样,机械连接在复合材料结构中应用才有可能。
(a) 螺接工艺要求
① 紧固件与孔的配合,要求达到H8/f8,孔与板的垂直度偏差在2º以内。
② 复合材料构件表面斜度超过5º时,必须使用特制倾斜度的垫圈。
③ 除传力件外(如电缆导管夹子、垫板等),螺栓的螺纹部分不允许在孔的挤压部位。
④ 在连接部位,特别在潮湿部位安装紧固件,一律采用湿装配。湿装配时,孔内或紧固件应涂密封胶,允许螺纹粘上密封胶,螺母必须在胶的施工期内上紧完毕。
⑤ 多钉连接安装时,不宜逐一的将单个螺栓一次拧紧,而应均衡对称的将所有螺栓分若干次拧紧,直至达到规定的拧紧力矩值。对缝内密封的螺栓,需分两次拧紧,初次拧紧必须在密封剂活性期内完成,重拧必须在初次拧紧后20分钟内进行,两次拧紧需在密封材料施工期内完成。
(2)铆接工艺
由于复合材料层间强度低和抗冲击能力差等弱点,一般认为不宜进行铆接。但是在一些承力不大的部位上,在采取一定工艺措施后,铆接工艺仍获得较普遍的应用。按钉杆粗细情况的不同,可分为钉杆镦粗的铆接和钉杆局部变形的铆接如半空心铆钉及双金属铆钉的铆接。
①钉杆镦粗的实心铆钉铆接工艺
在复合材料结构上应用最多的是TAl纯钛铆钉。这种铆钉在使用前,必须经真空退火处理,使其降低强度、改善塑性。铆接时,在镦头部位如为碳纤维复合材料,必须加厚度大于lmm纯钻垫圈。对直径为d的纯钛铆钉,铆接复合材料的工艺参数如下:
铆钉孔径=d十(0.3~0.4)
垫圈直径=d十(0.1~0.2)
镦头直径=(1.3~1.5)d
镦头高度=(0.5~0.65)d
②钉杆局部变形的半空心铆钉铆接工艺
为避免钉杆过粗而造成基体孔壁损伤,国外研制了仅钉尾产生变形而主杆部分基本不膨胀的半空心铆钉,它既使层合板牢固地连接在一起,又不使孔壁损伤,是一类很适于复合材料结构连接的新型紧固件。
半空心铆钉有两种型式:a双面埋头型半空心铆钉,它的材料为退火的55Ti—45Nb,其抗剪强度达345MPa,承载能力较高,由于铆接时钉的主杆不变形,所以铆接力只等于铆同样材料实心铆钉的一半,它主要适用在副翼、舵面、调整片等要求双面埋头的操纵面外部结构。b 凸头型半空心铆钉,材料为蒙乃尔合金,铆接时在成型模的作用下形成帽形镦头,能有效地将构件连接在一起,它主要应用于内部结构。
(2)聚酯模塑料胶接连接技术
胶接连接的主要优点有 :不会因钻孔引起应力集中和纤维切断,不减少承载横剖面面积;与连接形式相同的机械连接件比较,在受力较小的次要结构上,胶接连接件能够减重约25%,在受力大的主要结构上,胶接连接件能够减重5%~10%;能够获得平滑的结构表面,连接元件上的裂纹不易扩展,密封性较好;大面积胶接成本低;可用于不同材料之间的连接,无电偶腐蚀问题;加载后的永久变形较小;便于实现连接强度的优化设计。
胶接连接的缺点有:连接元件表面需要仔细处理;强度分散性大,由于湿度、温度等环境因素的影响,胶接强度会逐渐降低;对胶接质量的无损探伤比较困难;在大多数情况下是不可拆卸的。
(a) 胶粘剂的选择
复合材料的粘接要选用强度高、耐热性好的胶粘剂。复合材料常用的胶粘剂有环氧胶、酚醛-缩醛胶、快固丙烯酸酯胶、α-氰基丙烯酸酯胶、聚氨基胶等。
(b)粘接接头的设计
粘接接头由被粘物与夹在之间的胶层构成,是结构部件上的不连续部分,起着传递应力的作用。接头强度取决于胶粘剂的内聚强度、被粘物本身的强度和胶粘剂与被粘物界面的结合强度。而实测强度主要由三者之中最薄弱环节所支配,还受接头形式、几何尺寸和加工质量的影响。为使粘接的优点得到充分发挥,而将其缺点尽量缩小,必须确定合理的粘接接头结构。
接头的形式很重要,因为有机胶粘剂的最佳使用效果,是用于承受单纯或扭转的剪切力。实际上应用的接头形式可以是形式各异、变化多端,但总的都是几种基本类型的单独或相互组合的结果。图列举了几种聚酯模塑料的典型粘接接头形式。
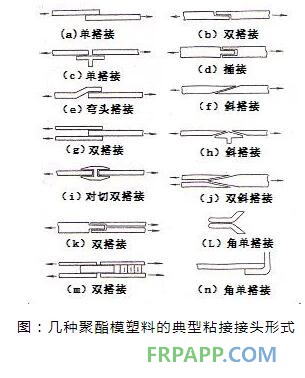
(c)胶接设备
图:为常用的胶接设备。
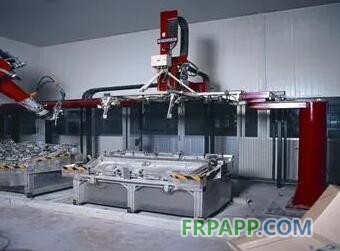
3.表面涂装
聚酯模塑料制品的表面涂饰工艺,通常是指在聚氨酯模塑料制品成型后(有时是在成型中),使用各种各样具有高性能的或特种功能的涂料,采用不同的涂装方法,对聚酯模塑料制品的表面进行涂装,从而起到装饰、保护、协调或赋予新功能作用的一种工艺方法。在玻璃纤维增强塑料领域中,片状模塑料(SMC)制品的涂装工艺在世界上研究的最多、最充分。SMC涂装工艺与普通的玻璃钢制品相比也最复杂。下面主要从表面涂装用原材料、表面涂装工艺和表面涂装设备三方面介绍SMC制品的涂装工艺。
(1)表面涂装用原材料
一般来说,典型的涂料系统由颜料,胶粘剂和溶剂组成。颜料提供颜色,耐久性和遮盖能力;而胶粘剂分散颜料,也提供整体性,耐久性,柔韧性和粘接性能;溶剂的作用是为喷涂而调节粘度,在喷涂过程中大部分挥发,留下的部分在漆膜固化时挥发干净。在涂料中往往还加入一些特殊的添加剂,以改善它的固化和增加光泽等等。强化外观的添加剂如金属或云母薄片也可加入,以产生珍珠般的漆膜。
(a)树脂性胶粘剂
通常也称其为成膜剂,是涂料牢固地附着于被涂物面上形成连续漆膜的主要物质。它是一种坚韧的、无定形的聚合物,赋予涂料大部分的热,机械化学和耐候性能。某些胶粘剂是软的和半弹性的如沥青和橡胶类,而另外一些是比较坚硬的,有时还是脆性的如环氧类和丙烯酸类。
(b)溶剂
涂料中所用的溶剂是一种纯的或混合的液体,它的主要作用是使胶粘剂或成膜剂溶解或分散成为粘稠的液体,以便涂料施工应用。溶剂的选用除了考虑其与胶粘剂的溶解性或分散性外,还需要注意其挥发性、毒性、闪点和价格等因素。
(c)颜料
涂料的颜料是在涂料中存在的小的实心的颗粒,它赋予涂层特殊的性能。颜料的颗粒尺寸范围从1um以下到100um以上,它们的形状可以是球形、片状或针状。颜料主要起装饰和保护的作用,并改进涂料的应用性能和力学性能,如增加硬度、耐久性以及降低成本等。
(d)添加剂
添加剂有时也称其为助剂。在涂料中,添加剂的用量是很少的,主要用于改善涂料某方面的性能。涂料用添加剂通常按其对液态涂料和涂料干燥后的涂层性能的影响进行分类,添加剂对液态涂料的下列重要性能有影响:如粘度、成膜性、结皮性、颜料分散性和乳液稳定性等。添加剂也对典型的干漆膜性能的柔韧性(硬度)、光泽、光稳定性和耐火焰等性能有影响。添加剂经常以它的功能来命名,例如,消泡剂,分散剂,乳化剂,润湿剂等。湿润分散剂用来改善涂料在生产过程中的性能;防沉剂,防结皮剂等用来改善涂料的储存稳定性等;流平剂、增稠剂、防流挂剂、成膜助剂、UV吸收剂、阻燃剂、防静电剂等用来改善涂膜的某些特殊性能。
下表中为常见的涂料类型:
下表中为常见的涂料类型:
(2)表面涂装工艺
(a)喷涂工艺
SMC车身板的喷漆本质上和其他材质没什么区别,也使用普通的喷漆室、固化烘房和静电喷涂设备。粉末喷涂和水性涂料系统,日益为人们所接受并使用,但是,溶剂型涂料的静电喷涂仍是使用的主流、标准的方法。
a)涂料的静电喷涂
大多数成型厂和组装厂都比较愿意用静电喷涂,因为这种工艺涂料使用量较少,最少的用量有利于成本和有机物的排放。在SMC底材上喷涂涂料层的一般程序是:导电底漆涂层→底漆→二道底漆涂层和BC/CC涂料层。
b)导电底漆涂层
导电底漆能促进对底材的粘接和为静电喷涂面漆提供导电的表面。导电底漆通常是一种密胺/聚酯、密胺/醇酸树脂或聚氨酯/多元醇,这些涂料在120~150℃范围内固化。SMC底漆涂料还可以配制成一种底材除气作用的阻挡层,这有助于困于底材的空气和水蒸气而产生的漆层鼓泡减少到最小的程度。
c)磷化处理层和电泳底漆
磷化处理层可以减少在喷涂面漆之前产生另外的灰尘进入的可能性。即使SMC零件通过电泳底漆喷涂加工,但涂料不会粘在零件上。SMC经过电泳底漆的最高温度不要超过204℃,时间不要长于30min。
d)底漆-二道漆底漆
底漆-二道漆底漆提供优良的充填细微空穴和擦伤缺陷的能力,它含有更多的固体,因而能形成厚的涂层而不会产生漆皱缺陷。
e)密封涂层
密封涂层是一种喷涂在底漆涂层和面漆层之间,以改善他们之间粘接的涂料膜。密封涂料像底漆涂料一样有热固性和热塑性两种类型,应和底漆涂料适当配合使用,例如:磁漆(热固性)密封涂料会攻击硝基漆(热塑性)底漆涂料,因而他们不可复合使用。
f)SMC汽车件面漆
在制品上的最后的一层,肉眼可见的漆膜,这是面漆涂层。面漆涂层可以分几次单独喷涂,如果涂层不烘烤而仅仅闪蒸就开始进行下一次的喷涂,这就称之为湿对湿涂敷。面漆涂层必须提供外表面理想的颜色、光泽、耐磨性和耐候性。
(b) 涂料的固化
所有经过喷涂的零件,在固化的烘道(房)中至少要经过3个单独的加热区进行固化:温度跃升区、固化区和冷却区。某些烘道设计还配备有附加的加热和冷却区,以利用不同车身板的特殊的材料特性的优势。在这些喷涂系统中,零件在进入第一区之前可以先曝露在辐射热的条件下,在这个辐射热区,零件经受高达260℃的高温长达8min。这种高的热梯度会引起涂层粘度快速下降,从而有助于零件所有表面上涂料的流动(熔流)和变得平整。它也会导致涂层形成完整的表皮层,可以减少当零件通过烘道受灰尘污染的可能性。喷涂过的零件经过辐射加热区后,进入温度跃升区,零件温度从室温升到149℃,在该区停留10min;然后进入固化区,在149℃下固化30min;最后,零件在冷却区停留15min,温度从149℃降到室温。
(c)工艺流程
SMC制品的表面涂饰工艺流程与其他玻璃钢制品的表面涂饰工艺流程相似,下图为一常见的SMC汽车制品的表面涂饰工艺流程图。
刮腻子→干燥→打磨→刮一遍腻子→干燥→打磨→水砂纸细磨→干燥→喷反光漆→干燥→喷透明面漆→干燥→贴花→罩光→干燥
(3)表面涂装设备
SMC/BMC的喷涂设备和用于其他底材(如金属)的设备没有什么不同,绝大部分常规的喷涂设备,原则上都可以用于SMC/BMC的表面喷涂。当喷涂数量较小,而且品种经常变换或者在多品种小批量的情况下,可以使用简单的人工喷涂系统。而当某些产品具有较大规模的产量时,一般都要在单独建立的喷漆生产线上进行喷涂。
(a)喷涂设备简介
a) 常规的小规模喷涂系统
普通的工业喷涂系统是由空压机、调节器、涂料罐和喷枪及空气管线组成。其中喷枪是关键设备,普通的空气喷涂喷枪主要有压力型和吸入型两种。压力型喷枪一般用于需迅速供应大量涂料的场合,又分为空压式和机械压力式。吸入式喷枪用于多种颜色低产量间歇式生产,涂料从直接连在喷枪上的涂料杯中吸取。典型的压力喂入空气喷枪是由空气管线供应空气以雾化涂料,涂料管线供应涂料。空气喷涂的传递效率为15%-30%。
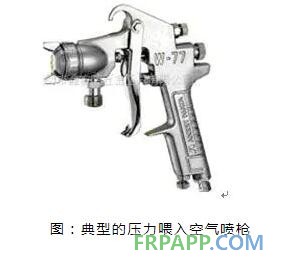
喷枪的另外一种类型就是无气喷枪,它没有空气管线连接到枪体上。涂料在非常高的压力下送到喷枪内。典型的范围为7-14MPa。无气喷涂的传递效率是20%-40%。
b) 喷涂室
一般的喷涂外围设备有三种主要类型,喷涂室、空气供应系统和废料处理装置,其中主要的是喷涂室。喷涂室是包围喷涂区的密封小屋,它的功能是防止漆雾外泄和保持喷涂过程中涂料不受灰尘的污染。
c) 静电喷涂设备
静电喷涂可以降低涂料的损耗。静电喷涂实质上是带电的涂料液滴沿着在喷枪和零件之间的电力线移动形成涂层的过程。静电喷涂和常规的空气喷涂相比,同样的涂料用量可多喷50%-70%的零件,尤其是对大而平的制品效率更高。静电喷涂有更均匀的涂层厚度和更好的覆盖边角的能力,但对制品的凹陷部分不能实现良好的覆盖。
(b)典型的喷涂生产线
在世界各国规模化的SMC制品喷涂生产线均以汽车喷涂生产线为其表率,它不仅代表SMC制品的喷涂及相关技术的最高水平,也是喷涂应用最广泛的领域。下图为某汽车件生产厂的喷涂线的平面布置图。
