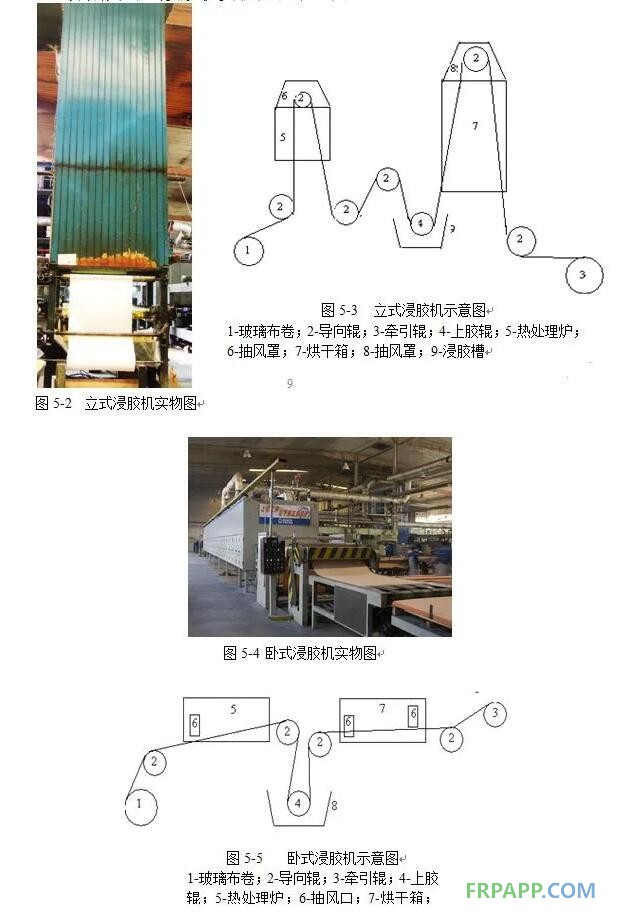
项目 布 |
厚度/mm |
经向密度/(根/cm) |
纬向密度/(根/cm) |
树脂 |
含胶量 /% |
胶液相对密度(胶槽) |
玻璃布 |
0.2±0.01 |
18±1 |
14±1 |
氨酚醛 |
29±3 |
1.07~1.09 |
0.2±0.01 |
18±1 |
14±1 |
氨酚醛 |
33±3 |
1.10~1.12 |
|
0.2±0.01 |
18±1 |
14±1 |
环氧酚醛 |
33±3 |
1.06~1.08 |
|
0.2±0.01 |
18±1 |
14±1 |
钡酚醛 |
32±3 |
1.07~1.09 |
|
0.1±0.005 |
20±1 |
20±1 |
氨酚醛 |
35±3 |
1.02左右 |
|
0.1±0.005 |
20±1 |
20±1 |
钡酚醛 |
33±3 |
1.03~1.05 |
|
0.1±0.005 |
20±1 |
20±1 |
环氧酚醛 |
35±3 |
1.00~1.02 |
|
0.165(人字纹) |
16±1 |
16±1 |
环氧634 |
41~43 |
1.035~1.039(夏) 1.045~1.046(冬) |
|
高硅氧布 |
0.25±0.015 0.25±0.015 |
12±1 12±1 |
12±1 12±1 |
钡酚醛 氨酚醛 |
40±3 37±3 |
1.06~1.08 1.045~1.06 |
涤纶布 |
钡酚醛 |
35~43 |
1.01~1.04 |
温度(℃) |
100 |
105 |
110 |
115 |
120 |
125 |
130 |
135 |
140 |
145 |
挥发份(%) |
5.11 |
4.23 |
3.85 |
3.47 |
3.41 |
1.70 |
1.25 |
1.32 |
1.04 |
0.86 |
不溶性树脂含量(%) |
—— |
—— |
—— |
0.54 |
1.16 |
26.0 |
55.6 |
59.3 |
76.7 |
90.4 |
时间(分) |
||||||
5 |
7 |
10 |
15 |
20 |
||
110 |
挥发份(%) 不溶性树脂含量(%) |
3.26 —— |
3.16 —— |
3.02 —— |
2.38 22.3 |
2.13 37.7 |
115 |
挥发份(%) 不溶性树脂含量(%) |
3.12 2.50 |
2.55 5.85 |
2.12 30.2 |
2.17 56.8 |
1.64 49.3 |
120 |
挥发份(%) 不溶性树脂含量(%) |
2.50 12.0 |
1.66 42.0 |
1.72 57.5 |
1.60 62.0 |
0.95 78.0 |
树脂含量(%) |
弯曲强度(MPa) |
拉伸强度(MPa) |
冲击强度(Kj/m2) |
60 |
107.3 |
64.6 |
23 |
51.2 |
143.4 |
86.5 |
34.2 |
45.1 |
140.6 |
89.0 |
46.2 |
40 |
179.0 |
120.9 |
49.5 |
37 |
177.5 |
116.6 |
45.7 |
胶布名称 胶布指标 |
3240酚醛环氧玻璃布 |
3230酚醛树脂胶布 |
FR-4环氧玻璃布 |
酚醛改性二苯醚胶布 |
含胶量(%) |
38~42 |
38~42 |
41~43 |
38~42 |
挥发份含量(%) |
1~1.6 |
≤4 |
<1 |
1~1.2 |
可溶性树脂含量(%) |
>80 |
70~85 |
60~80 |
80~90 |
问题 |
原因 |
对策 |
胶布的含胶量不均 |
1)胶液不均匀 2)浸胶时张力不均 |
1)搅匀胶液 2)调节张力 |
胶布的流动性、挥发份含量突然增大 |
1)烘箱温度没有调节好,风量不均 2)浸胶速度过快 |
1)待烘箱温度达到要求后再开动机器 2)适当调节浸胶速度 |
胶布上有黑斑或黑点污迹 |
烘箱出口处墙壁和排风管口上有积聚的低分子物 |
用棉布将墙壁和排风管口擦干净 |
挤压辊间发生多层布反卷 |
胶布运行速度与收卷速度不同步 |
立即停止电机运转,检修挤压辊 |