1 前言
含氮螯合树脂尤其是多胺型螯合树脂,由于结构中存在大量胺基,对重金属离子具有良好的吸附性能[1,2],广泛应用于重金属离子的分离、富集及环境保护等方面。传统制备多胺型螯合树脂大多采用多乙烯多胺与交联聚合物进行化学反应,但这类树脂造粒难,化学稳定性及热稳定性差,颗粒内部的功能基难以参加吸附,并且再生速度较慢,加上交联聚合物本体强度低,多次使用时易破碎损失,因此限制了该类树脂的螯合性能[3,4]。以无机颗粒为螯合树脂载体,进而形成核-壳型复合分离材料可以提高树脂的抗压强度及比重,增加使用寿命[4]。由于大的粒径产生小的粒子表面,使离子交换面积显著减少,从而分离或吸附速度减小[5]。而带石英砂核的分离材料在减小粒径的同时,核的机械强度赋予分离树脂承受高剪切力,适用于大面积的动态交换,并提高处理效率。目前制备带核分离材料的方法有2种,一是用带功能基的树脂通过固化反应直接包覆成粒;二是先包覆成粒,再把功能基团接上去。后者往往包覆不均匀,核易暴露而使树脂不稳定,笔者认为前者能制备稳定的包覆体,但在包覆过程中,固化工艺参数直接影响包覆体颗粒形态及尺寸,并影响其稳定性,因此有必要对包覆体的固化行为进行研究。
与其他热固性树脂相比,环氧树脂具有附着力强、硬度高、耐磨性好、耐高低温和耐化学品性能优异、室温下可用很多固化剂快速固化等优点[6],是制备高性能复合材料的重要基体。加入固化剂交联成网状体型三维结构,能够赋予复合材料良好的力学性能和物理性能,非常适合作重金属离子螯合分离材料。有关环氧树脂固化机理及动力学的研究很多[7~9],但大多用于制备混合型的复合材料,且只报道了制备工艺过程及其有关参数,而对如何利用其固化工艺来包覆无机颗粒的研究尚未见报道。本文利用E-44环氧树脂在不同温度(95℃、105℃)下选用不同的固化剂(三亚乙基四胺简称TETA;乙二胺简称EDA)对石英砂的包覆过程进行研究,通过摄影显微镜观察树脂颗粒的外层来表征不同尺寸石英砂包覆体的物理结构。
2 实验部分
2.1 原材料及主要仪器
E-44环氧树脂(岳阳石油化工总厂生产,环氧当量g/eq:210-230),TETA(CP,江苏常州石油化工厂生产),EDA(CP,成都市科龙化工试剂厂生产),明胶(AR,市售),粗石英砂(0.1~0.5 mm)、细石英砂(1~2μm)(青岛海洋化工厂生产)。摄影显微镜XSS-1(南京,江南光学仪器厂生产)。
2.2 实验方法
往250 mL三口烧瓶中加入80 mL 20 %的NaOH水溶液及10 g的环氧树脂,在明胶分散作用下加3 g粒径分别为0.1~0.5 mm和1~2μm的粗、细2种石英砂,常温搅拌30 min。取固化剂(TETA或EDA) 3 mL,在7 mL 15%的NaOH水溶液中稀释(以防局部树脂结块并降低固化剂在水中的溶解度)后备用。待树脂分散无明显团状物后,加热到反应温度,分3次在15 s内加入固化剂并开始计时,以一定时间间隔吸取含一定量树脂的反应混合液,注入有100 mL 5%HCl的试剂瓶,充分洗涤除去胺类固化剂,然后用去离子水反复洗涤至pH=7,烘干待用。
2.3 固化率的测定
用已称重的滤纸包扎好树脂于70℃烘干至恒重,称量,然后在脂肪提取器中用丙酮回流萃取未固化的环氧树脂8~10 h,将萃取后的树脂烘干至恒重并称量。
树脂的固化率计算方法如下:

其中萃取前树脂重量=合成产物经水萃取6 h后总重量(干重)-合成投入的石英砂总重量。
2.4 表征方法
用摄影显微镜观察包覆体的物理结构。
3 结果与讨论
3.1 不同固化条件对固化率的影响
环氧树脂的固化过程可简化表达如下:
E-44型环氧树脂+n脂肪胺类→固化产物
3.1.1 反应温度对固化率的影响
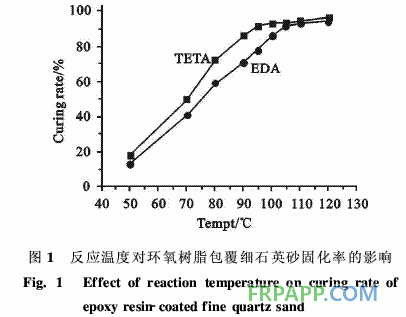
环氧树脂与固化剂的固化反应需要加热到一定的温度,在固化剂作用下环氧树脂包覆石英砂的固化速度可以以一定时间内树脂的固化率来衡量。图1是反应时间为20 min时不同固化剂固化环氧树脂包覆细石英砂固化率与反应温度的关系曲线。由图1可以看出,在时间一定时,固化率随着温度的升高而提高,但增幅变化逐渐趋缓。同等条件下以TETA为固化剂的固化率高于EDA。若反应温度小于80℃时,则两者固化率分别在72.4%和59.2%以下,此时完全固化所需的时间较长,固化速度较慢,且因颗粒表面不能快速硬化,所得产物聚集成团,颗粒强度不足,包覆效果很差;若反应温度大于110℃,则两者固化率均较大,分别为93.8%和91.1%,此时完全固化所需的时间大为缩短,但固化速度过快,固化剂来不及均匀分散,致使局部固化剂堆积,产物容易结块,且因其它部位固化剂浓度不足,产物表面固化不均,包覆效果不好。故合适的反应温度以90~110℃为宜,本文重点讨论95℃和105℃2种温度下的固化率。
3.1.2 反应时间对固化率的影响
图2、图3分别为2种固化剂在95℃和105℃下实验所得固化率与时间关系的曲线。
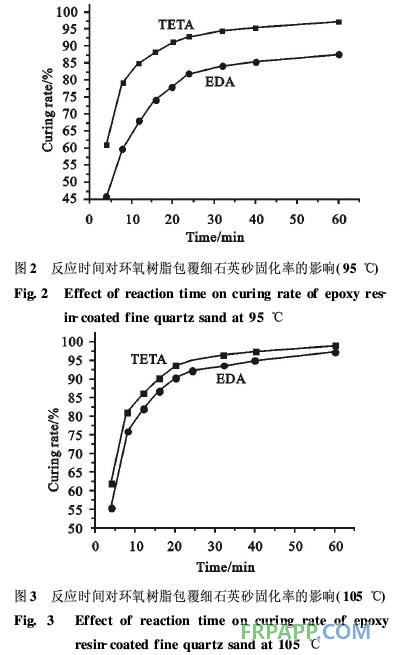
由图2可看出,95℃时,TETA与环氧树脂包覆细石英砂的起始固化率远高于EDA体系,即前者的初始固化速度快于后者,这有利于包覆体表面快速硬化。在同一反应时间,前者的固化率总是明显大于后者,这说明前者的平均固化速度明显大于后者,因此完全固化所需的时间远低于后者。而如当反应时间为60 min时,TETA体系的固化率达到97.3%,而EDA的为87.7%,因此低温下EDA体系完全固化反应所需的时间较长。由图3可知,105℃时,在相同反应时间内,EDA-环氧树脂的固化率接近于TETA-环氧树脂,这说明EDA体系的固化率对温度更为敏感。无论采用哪种固化剂,随着反应温度的升高,固化速度(反应速度)加快,任一时间的固化率不断提高,特别是EDA-环氧树脂体系,同一时间的固化率随温度的增加显著增大。例如反应时间同为60 min时,105℃的固化率(97.6%)明显大于95℃的固化率(87.7%),这说明要缩短EDA与环氧树脂完全固化所需的时间需要较高的反应温度。但对TETA-环氧树脂体系而言,在95℃和105℃2种不同温度下,在相应的时间内,其固化率改变不大,或者说在95℃以上固化速度随温度升高而增大的趋势不太明显,因此可利用低温(95℃)来控制TETA-环氧树脂的固化行为。
另外在105℃下,这2种固化剂对环氧树脂都有初始快速固化的特点,在开始不长时间(4 min)内,两者都达到了超过55%的固化率。快速固化能使颗粒表面迅速硬化,有利于包覆体不发生粘连或团聚。由于TETA结构比EDA具有更多的胺基,可以更多地与重金属离子形成螯合物而显示出更加优良的吸附性能,而且它与环氧树脂的固化行为无需高温条件,更具有初始固化速度快和完全固化时间短的特点,故TETA较适合作为包覆体的固化剂。
3.2 不同尺寸石英砂对包覆体结构形态的影响
图4、图5为反应温度95℃、反应时间2 h下TETA固化环氧树脂包覆不同尺寸石英砂的物理结构。图4揭示粗石英砂以单颗粒包覆,包覆体形态就是石英砂本身的单颗粒形貌,只是外表覆盖一层硬化树脂层,由于石英砂属坚硬、化学性能稳定的硅酸盐矿物,树脂及固化剂无法进入颗粒内部,固化树脂/石英砂质量比较小,或者说单位质量石英砂表面的多胺型螯合树脂较少,且因粒径较大,粒子比表面积小,用于重金属离子吸附时,分离效率不高;图5揭示了细石英砂包覆体呈聚集状态,包覆体外观酷似核桃型球体,内部包含多个裹着硬化树脂外套或与之相互混合的细小石英砂颗粒,树脂及固化剂已经进入包覆体内部,单位质量石英砂表面的多胺型螯合树脂较多。这些细小颗粒在介质中包覆成紧密的聚集体,粒形规整,具有较好的机械强度和化学稳定性,且粒径比粗石英砂包覆体更小,大小基本均匀,粒子比表面积大,适合作为高效的多胺型螯合树脂,用于处理重金属离子。
无论粗、细石英砂,产物(包覆体)间均无粘接现象,不发生粘连的原因可能是由于前述的初期固化速度较快,包覆体表面迅速硬化,相互之间来不及发生粘连的缘故。
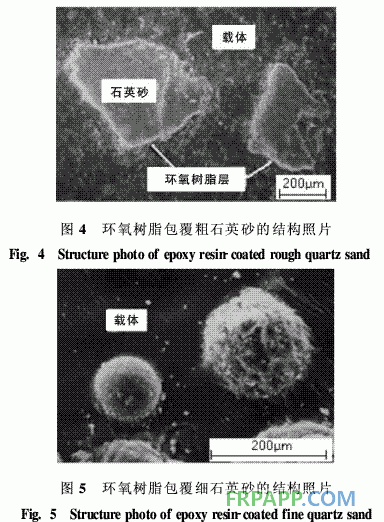
4 结论
TETA与环氧树脂的固化行为具有初始固化速度快和完全固化时间短的特点,固化反应可在低温(95℃)完成,固化后的环氧树脂/细石英砂粒状包覆体颗粒均匀呈球状。TETA适合作为环氧树脂/石英砂包覆体的固化剂。作为核-壳型螯合树脂的基质应以细石英砂为宜。