工艺流程
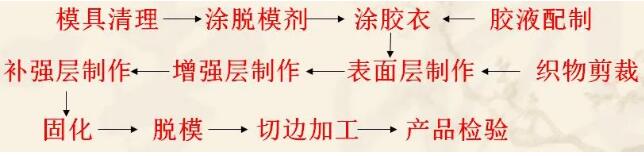
模具上应预先涂覆脱模剂(石蜡、黄油、甲基硅油、聚乙烯醇溶液、聚氯乙烯薄膜等),常用的树脂是能在室温固化的不饱和聚酯树脂和环氧树脂。
手糊成型工艺的特点
优点:
①不受产品尺寸和形状限制,适宜尺寸大,批量小,形状复杂产品的生产。
②设备简单,投资少,设备折旧费低。
③工艺简单。
④容易满足产品设计要求。
⑤制品树脂含量较高,耐腐蚀性好。
缺点:
①生产周期长,效率低,劳动强度大,卫生条件差。
②产品质量不易控制,性能稳定性不高。
③产品力学性能较低。
用途:
手糊成型法可以制作汽车车体,各种渔船和游艇、储罐、槽体、卫生间、舞台道具、波纹瓦、大口径管件、机身蒙皮、整流罩、火箭壳体、隔音板等复合材料制品。
2.1 原材料的选择
合理的原料是满足产品设计要求,保证质量,降低成本的重要前提。
选用的原材料必须满足3点要求
1、产品设计的性能要求
2、手糊成型工艺要求
3、价格便宜、材料容易取得
包括:聚合物基体和增强材料
目前国内大部分手糊制品均用不饱和聚酯树脂,约占80%,其次是环氧树脂。
2.2手糊成型模具与脱模剂
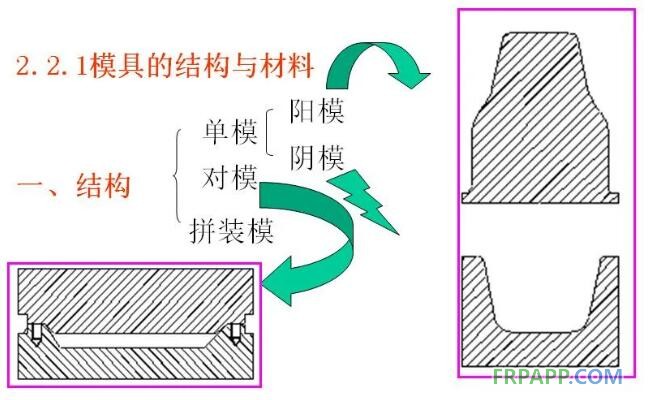
阳模:制品内表面尺寸准确,光滑。成型方便,便于通风。
阴模:制品外表面尺寸准确,光滑。阴模深,操作不便、通风条件不好、卫生条件差。
对模:由阴阳模两部分组成,制品内外表面均光滑,厚度准确。不适合成型批量少及大型制品(模具、设备投资大)。
拼装模:一些形状复杂的产品,为了脱模方便,需要利用拼装模,即把模具分成几块进行拼装,脱模时可以分块进行,比较方便。
二、模具材料
木材、石膏、水泥、石蜡、可溶性盐、玻璃钢、陶土、金属等。
必须满足以下要求:
(1)满足产品尺寸、精度、外观及数量的要求;
(2)有足够的强度与刚度,不易变形、损坏;
(3)不受树脂及辅助材料的浸蚀,不影响树脂固化;
(4)易脱模,使用周期长;
(5)价格便宜,材料易得。
具体材料:
(1)木材
要求均质、无节。常用红松、银杏、枣木等。木材模具表面需要封孔处理。其特点是质轻、易加工;但不耐久。适合于小批量生产小型制品。
(2)石膏
用半水石膏成型。制造简便,造价低;不耐用,怕冲击,适合于小批量生产形状复杂的制品。
(3)水泥
制造方便,成本低,有一定强度,适合于制造形状简单,表面要求不高的制品。
(4)石蜡
适合于制作难以取出的型心,一次性使用,成型后融化掉。
(5)金属
常用钢材、铸铝等。耐久、不易变形;但加工费用高。适合于小型、大批量生产的高精度制品。
(6)玻璃钢
由木模或石膏模翻制。质轻、耐久、制造方便。适合于中小型制品的批量生产。
2.2.2 手糊成型模具设计要则
(1)设计要点
(2)设计内容
A、确定模具结构
B、选定原材料
C、确立制造方法
D、绘制模具图纸
2.2.3 玻璃钢高级模具
属于平整度高,光洁度高的高级模具。
2.2.3.1 玻璃钢高级模具的要求
(1)具有足够的强度、刚度。
(2)具有一定硬度(巴柯儿硬度40以上)、耐热性能承受树脂固化放热的收缩作用。
(3)尺寸精确、无潜藏气孔,残留划痕度小于0.1μm。
(4)光泽度达到80-90光泽单位或者目测反光。
2.2.3.2 材料选择
(1)胶衣树脂
应具有收缩率低、延伸率高、耐磨、耐热、硬度高等优良性能。
实践证明:采用环氧树脂加填料制作模具的胶衣比较合适,或者采用专用的胶衣树脂制作胶衣层。
为提高耐磨性可以在胶衣层可加入硬度高的填料,如瓷粉、石英粉、铸石粉、刚玉粉等。
(2)玻璃纤维表面毡和玻璃纤维短切毡
作用:A、增强胶衣,防止表面微裂纹;
B、形成富树脂层以提高模具光洁度和耐腐蚀性能;
C、消除玻纤布在表面产生的痕迹。
(3)中碱无捻方格布
(4)不饱和聚酯树脂
(5)无机填料
2.2.3.3 制造工艺
(1)过渡母模的制造
材料:石膏或木材
(2)玻璃钢模具的翻制
胶衣层制作,涂刷3层,每层0.2-0.5mm,铺1-2层表面毡;一层短切毡,压实、浸透排除气泡。
铺无捻方格布。
(3)模具表面处理
A、粗磨。400#、500# 、600#水砂纸依次水磨。
B、水砂精磨。1000#、1200#、1500#水砂纸依次研磨。
C、研磨抛光。将抛光剂涂上后,停留1-2min,用布轮抛光机逐段抛光并反复进行。
(4)表面质量检测
要求光泽度在90以上,用ss-82型光电光泽计检测。
2.2.4 脱模剂
脱模剂应具备的条件:
(1)不腐蚀模具,不影响固化,与树脂粘附力小;
(2)成膜迅速、均匀、光滑;
(3)使用简便、安全,价格便宜。
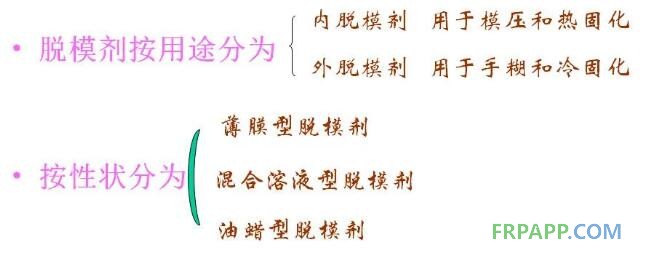
2.2.4.1 薄膜型脱模剂
最常用的有:聚酯薄膜、玻璃纸、聚氯乙烯薄膜、聚乙烯薄膜等。
其中聚酯薄膜应用最普遍,制品平整光滑,具有很好的光洁度,但价格较高。使用厚度一般为0.04 mm 、0.02 mm。
使用方法:铺在模具上,或用凡士林贴在模具上。
优点:脱模效果好,使用方便,材料易得。
缺点:薄膜的柔韧性、帖服性差,不能用于形状复杂的制品。
2.2.4.2 混合溶液型脱模剂
(1)聚乙烯醇脱模剂的配制
一般采用较低分子量的聚乙烯醇。
在搅拌状态下,用水将聚乙烯醇加热溶解(水温约95℃),冷却到室温,往里滴加乙醇或丙酮(边加边搅拌)。
加入甘油可增加膜的柔韧性;
加入少量洗衣粉,可使成膜均匀;
加入少量蓝、红墨水可防止漏涂;
需要干燥快则适当多加乙醇或丙酮。
(2)过氯乙烯脱模剂
配方:过氯乙烯粉5~10份
甲苯+丙酮(1:1)95~90份
按比例将物料与溶剂混和搅拌,放入密闭容器中(不能用塑料容器)等完全溶解后即可使用。
(3)聚苯乙烯溶液脱模剂
配方:聚苯乙烯粉 5份
甲苯 95份
称量混合,搅拌均匀后,密封放置7天左右,若完全溶解,搅拌均匀即可使用。
缺点:甲苯有毒
优点:脱模容易,成模速度快
2.2.4.3 蜡类、油酯类脱模剂
(1)蜡类脱模剂(蜡型脱模剂)
使用方便、省工省时、价格便宜,脱模效果好,使用广泛。
(2)油酯类脱模剂
a、硅酯脱模剂
硅酯 100份
甲苯 100份
b、其他油脂脱模剂
耐热机油,硅油,凡士林油,变压器油等。
2.2.4.4 脱模剂复合使用
对大型制品或外型复杂的制品,多采用几种脱模剂复合使用,效果较好。
2.3.1 原材料准备
2.3.1.1 胶液准备
胶液的主要工艺指标是:胶液粘度;凝胶时间。
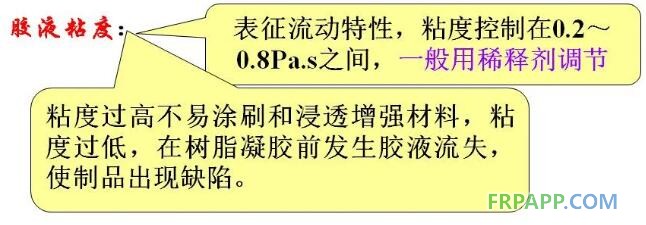
凝胶时间:指在一定温度条件下,树脂中加入定量的引发剂、促进剂或固化剂,从粘流态到失去流动性,变成软胶状态凝胶所需的时间。
一般采用改变引发剂、促进剂的用量调节。
凝胶过快—来不及操作,制品交联太严重、收缩大、发脆。
凝胶过慢—增加了生产周期,且易发生流胶。
影响凝胶时间的主要因素:
⑴引发剂、促进剂用量。引发剂、促进剂用量大,凝胶时间缩短;
⑵胶液体积的影响。胶液体积越大,热量不易散失,凝结快;
⑶环境温度、湿度的影响
气温越高,凝结越快
湿度越小,凝结越快
⑷制品表面积影响
制品表面积大,凝结快。
2.3.1.2 增强材料准备
a.纤维表面处理(热处理或化学处理);
b.使用前烘干处理;
c.按样板下料。
下料时应注意以下几点:
1、布的方向性。
2、拼缝应各层错开。
3、对圆形制品,布的45°方向变形能力好,可沿此方向裁成布条糊制。
4、注意经济使用。
2.3.1.3 胶衣糊准备
胶衣树脂种类很多,应根据使用条件进行选择。
33号胶衣树脂(间苯二甲酸型胶衣树脂),耐水性好;
36PA胶衣树脂,自熄性胶衣树脂(不透明);
39号胶衣树脂,耐热自熄性胶衣树脂;
21号胶衣树脂(新戊二醇型),耐水煮、耐热、耐污染、柔韧、耐磨胶衣。
胶衣树脂的配制
33号胶衣树脂 100份 (重量百分比 wt%)
50%过氧化环己酮二丁酯糊 (引发剂H)白色 4份
6%萘酸钴苯乙烯溶液 (促进剂E)紫色 2~4份
2.3.2 糊制
2.3.2.1 表面层(胶衣层)
一般采用加了颜料的胶衣树脂制作,也可用普通树脂制作,需用玻璃纤维表面毡增强防裂。
表面层的作用:形成富树脂层、光洁美观、耐侵蚀、耐水、耐酸碱、耐候等。
厚度控制:0.25~0.5mm,单位面积用胶300~500g/m2 。
操作方法:a、刷涂(需两遍垂直涂刷,一遍基本固化后再刷另一遍,开始凝胶时铺纤维毡)。
b、喷涂。
影响胶衣喷涂的因素:
(1)触变指数的影响 用喷射距离调节(也可用压力调节 )。距离400~500mm,压力0.4~0.5MPa。
(2)温度的影响 控制胶衣树脂温度25-30℃。
(3)胶衣层中气泡的影响 严禁混入气泡。
(4)苯乙烯含量的影响 喷涂时苯乙烯挥发可造成固化不好,应注意。
(5)水分影响 胶衣层中严禁水分混入,包括树脂中和模具上。
2.3.2.2 铺层控制
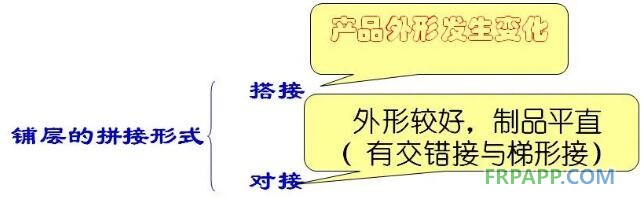
在接缝区加一层附加布增强;接缝距离S一般控制在1~2cm。
2.3.2.3 铺层二次固化拼接
对于较厚的制品,由于树脂固化放热量大,易产生产品的变形与分层。应分两次铺层固化。一般δ>7mm时,需分两次铺层固化。(实验中注意!)
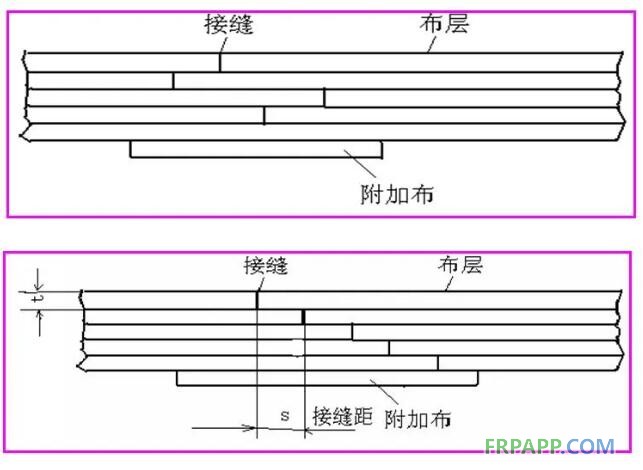
铺层2次固化的拼接方法:
先按一定铺层锥度糊制各层,使其形成阶梯形,达到一定厚度后(不超过7mm),在阶梯上铺放一层“无胶平纹玻璃布”。固化后撕去该层玻璃布并保证拼接面的粗糙度和清洁。然后糊以下各层。
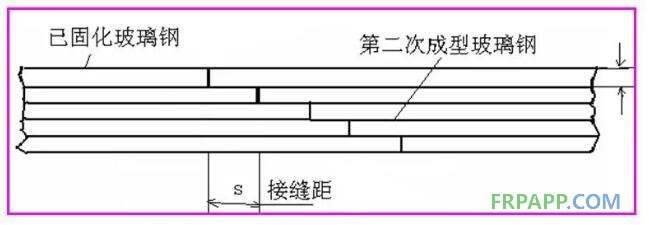
对于大表面制品糊完后应覆盖玻璃纸或薄膜,使与空气隔绝。
2.3.3 固化
2.3.3.1 不饱和聚酯树脂的固化
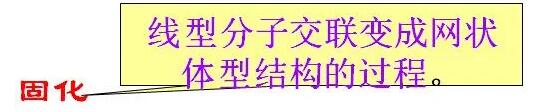
分为:凝胶阶段
定型阶段(硬化阶段)
熟化阶段(完全固化阶段)
加入引发剂后,引发剂在一定条件下可以产生游离基,游离基是一种活性很高的物质,可以把树脂中的双键打开,从而达到聚合交联的目的。
因为引发剂一般在60℃以上才能分解出游离基,因此常温固化时必须加入促进剂,降低其分解温度。
引发剂用量对产品性能的影响
用量过大:反应速度过大,放热量大,导致树脂急剧固化,收缩严重,产生裂纹。同时影响聚合链长度,分子量降低,力学性能下降。
用量过小:不足以使树脂固化完全。
2.3.3.1 固化工艺控制
固化度:树脂固化反应的程度(用百分率表示),常用丙酮萃取法测定。
手糊制品的成型工艺条件:温度15℃以上,湿度小于80%。
利用上述工艺条件及合理的配方,才能使树脂固化达到要求的程度。
一般手糊制品24h脱模(巴氏硬度15~30时);8天即可使用。聚酯玻璃钢的强度一般到1年后才能稳定。(时间与强度关系见表2-15)。因此,许多制品室温固化后,为加速其强度发挥,需进行后固化处理(放置24小时后进行)。
环氧玻璃钢后固化处理温度 < 150℃ 。
聚酯玻璃钢后固化处理温度 50℃~80℃。
2.3.4 手糊工艺质量控制
2.3.4.1 影响制品质量的因素
组分质量;成型与固化过程;制品辅助加工。手糊制品存在的主要质量问题
产生缺陷的原因:
纤维方面:
树脂基体方面:
施工作业方面:
固化工艺方面:
其他方面:
2.3.4.2 质量控制
在工厂车间,制定质量控制制度时参考。
包括3方面:
原材料质量控制
成型工艺过程控制
成品质量检验
2.3.4.3 手糊成型易发生的缺陷及防止措施
1、胶衣缺陷的防止措施
2、制品皱缩
3、翘曲变形
4、制品表面发粘
原因1:空气湿度太大,水对树脂起阻聚作用。
解决办法:
(1)在树脂中加入0.02%左右的液体石蜡;
(2)在树脂中掺加5%的异腈酸酯 ;
(3)制品表面覆盖薄膜隔绝空气;
原因2:引发剂、促进剂的比例弄错或失效,更换引发剂、促进剂。
5、制品内气泡太多
原因1:树脂用量过多
解决办法:
1、控制胶含量
2、注意拌合方式
原因2:树脂粘度过大
解决办法:
1、适当增加稀释剂
2、提高环境温度
原因3:增强材料选择不当
解决办法:
选用浸透性好的无捻玻璃布
6、流胶
原因1:树脂粘度太小,可加入2~3%的活性氧化硅。
原因2:配料不均匀,充分搅拌。
原因3:固化剂用量不足, 适当调整固化剂用量。