碳纤维材料具有良好的物理化学性质,其质量轻,密度为1.5~2g/cm3,它的密度不到钢的四分之一,但拉伸强度是钢的7~9倍,其良好的比强度使得其被广泛应用于航空航天等要求轻质高强的领域[1]。其化学性质同样良好,具有耐腐蚀、耐疲劳、耐高低温,同时其具有良好的导电性,介于金属和 非金属 之间。除此之外,碳纤维还具有耐油、抗辐射、抗放射、吸收有毒气体和使中子减速等特性。
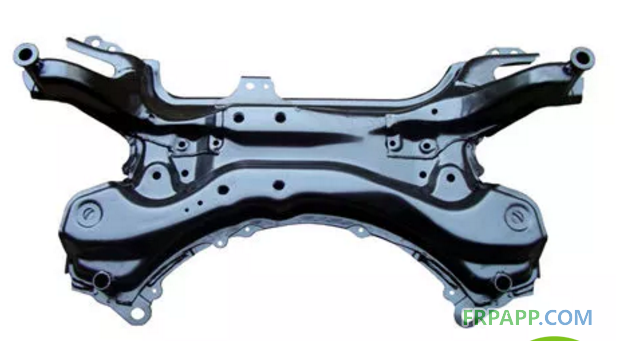
纤维增强复合材料是纤维与树脂经过一定的成型工艺形成复合材料。增强纤维主要有碳纤维、玻璃纤维、芳纶等,树脂基体有热塑性树脂和热固性树脂。大多数金属材料的疲劳极限是其拉伸强度的40%~50%,碳纤维增强树脂基复合材料的疲劳极限则可达其拉伸强度的70%~80%。此外,碳纤维增强树脂基复合材料还具有减振性好、破损安全性好及可设计性强等特点,因此在航空航天、交通运输及体育器材中应用越来越广泛。美国空军的F系列战斗机中大量采用了碳纤维材料以减轻机身质量。在汽车方面,宝马公司采用了碳纤维材料来制造汽车车身。碳纤维增强环氧树脂基复合材料,其比强度、比模量综合指标,在现有结构材料中是较高的。碳纤维增强环氧树脂基复合材料的比强度可达钛的4.9倍,比模量可达铝的5.7倍。在强度、刚度、质量、疲劳特性等方面有严格要求的领域,在要求高温、化学稳定性高的场合,碳纤维增强环氧树脂基复合材料都颇具优势。
纤维增强泡沫夹层复合材料是由上下面板及中间夹芯三层材料制成的复合材料,它的上下面层是高强度、高模量纤维材料,中间是强度较低的轻质夹芯层。上下面板承担主要的拉应力和压应力,芯材主要承担剪切应力。芯材的力学作用机理是连接面层使之成为整体构件,让薄而强的面层在承担较高拉应力的同时不发生屈曲,并将剪切力从面层传向内层。夹层复合材料实际上是复合材料与其它轻质材料的再次复合,采用夹层结构方式是为了提高材料的有效利用率和减轻结构质量[3]。以梁板构件为例,在使用过程中,一要满足强度要求,二要满足刚度需要,纤维增强复合材料的特点是强度高,模量低。因此,用单一的复合材料制造梁板,满足强度要求时,挠度往往很大,如果按允许挠度进行设计,则强度大大超过,造成浪费,只有采用夹层结构形式进行设计,才能合理解决这一矛盾,这也是夹层结构得以发展的主要原因。
笔者采用碳纤维布及聚对苯二甲酸乙二酯(PET)泡沫材料,通过真空灌注工艺制备了泡沫夹层复合材料,制备的泡沫夹层复合材料再在模具的辅助下制备了汽车副车架,其中主梁2根,横梁5根,边梁2根。最后将汽车副车架与主车架进行了连接。
1 、 实验部分
1.1主要原材料碳纤维布:T–700,面密度为200g/m2,日本东丽株式会社;PET泡沫:密度为60kg/m3,思瑞安复合材料(中国)有限公司;聚氯乙烯(PVC)泡沫:密度为45kg/m3,思瑞安复合材料(中国)有限公司;阻燃环氧树脂:GT807,惠利(广州)电子材料有限公司。
1.2主要设备及仪器真空泵:东莞市博大真空设备有限公司;模具:自制;真空导入系统,自制。
1.3复合材料制备工艺先将模具清理并打脱模剂,其次将碳纤维布按一定角度铺覆于PET泡沫上,其主要铺层角度为[0/45°/90°/–45°],铺层共铺设6次,共24层。然后对密封体系抽真空,当真空度达到–98Pa时,保压0.5h之后注入环氧树脂,注胶完成后保压固化,最后脱模制得副车架。其工艺流程如下:模具处理→纤维铺层→密封→抽真空→检漏保压→混胶注胶→固化脱模→后处理修边。
1.4加工工艺的调整
(1)固化温度。环氧树脂在固化过程中,树脂分子在固化剂或促进剂的作用下经历了分子链的线性增长、支化和交联等过程,最终形成三维网络结构。树脂的交联度和固化效果直接决定着复合材料的性能。固化温度对树脂的固化过程有着直接的影响。如果固化温度低则可能造成固化不完全,固化速率慢;如果固化温度太高则造成产生较大的收缩内应力,或引起暴聚,产生黄变及气泡。副车架所用环氧树脂体系经实验获得最佳固化温度为30℃。
(2)成型压力。真空灌注工艺的过程决定了成型过程中最大压力为1个大气压,通常成型压力越大可以获得越高纤维含量的复合材料。在1个大气压下可以获得约65%体积分数的纤维含量,已经属于较理想的纤维含量。
(3)铺层工艺。铺层过程中采用对称铺层的原则,每次共铺设4层,按[0/45°/90°/–45°]进行铺设,保证铺层角度的对称性。铺层共铺设6次,共24层。如果铺层过程不对称则可能产生收缩不均匀,从而在最终结构中产生内应力,造成制件脱模后翘曲。
2 、 副车架制作工艺
2.1边梁制作采用两个L型模具拼合,组成一个U型模具来制作边梁,由于L型模具制作的不标准,导致边梁两边距离不等距。另外边梁制作过程中漏气较严重,主要由于拼合模具的粘接问题。为了解决这一问题,必须加大粘接剂用量并结合密封胶才能保证拼合模具紧密结合、不漏气。单根边梁的质量为8.2kg。
2.2横梁制作横梁制作主要问题在于裙边在抽真空过程中有局部地方凹陷或凸起影响安装,这种情况主要是由于横梁与裙边接触位置不贴合。解决此问题需要将泡沫在此裙边位置保持直角,这样裙边纤维就会与梁本体纤维贴合。其铺层方案同边梁,不同的是其裙边采用45kg/m3的PVC泡沫作为支承,单根横梁最终质量为6.4kg。
2.3主梁制作主梁是整个副车架主要承力部件,其制作至关重要。主梁由于长度过长,线度不够,需要模具给一支承,保证其线度。副车架主梁与主车架连接时是通过螺栓将副车架主梁固定在主车架上的;但是由于复合材料不能够直接攻丝固定螺栓,因此在主梁对应位置内部作了金属预埋件。金属预埋件的放入方法就是在内部结构泡沫处预留出金属预埋件的空间,铺层过程中直接用碳纤维将其包覆。主梁制作过程容易出现的问题是由于固化时间不够,固化不完全,在脱模过程中稍有不当便会导致梁翘曲。主梁制作与横梁铺层方案相同,单根主梁质量为22.5kg。整个副车架9根梁加上金属件的总质量为116kg。
3 、 车架连接设计
3.1中间横梁与边梁连接
中间横梁与边梁连接:将中间梁与边梁两端伸出的裙边部分加厚,然后通过螺栓连接,具体连接方式如图1所示。
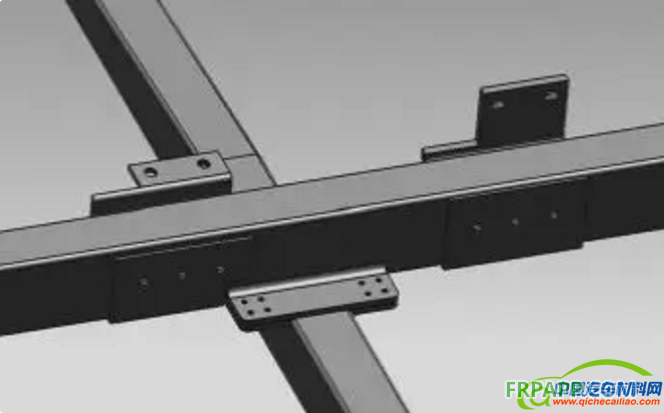
图1中间横梁与边梁连接方式
3.2中间横梁与两主梁连接中间横梁与两根主梁的连接:将两根梁接触部分分别伸出裙边,再通过螺栓连接,具体连接方式如图2所示。
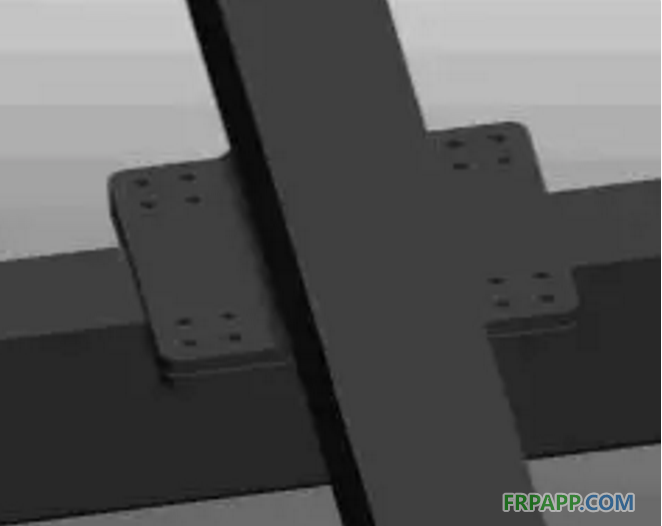
图2中间横梁与两主梁连接
3.3副车架与主车架连接
副车架与主车架的连接:副车架与主车架连接与原有连接方式相同,通过金属胶粘及螺栓将连接件固定于主梁上,连接件通过螺栓与主车架相连,如图3所示。

图3副车架与主车架连接方式
4 、结论
采用碳纤维布、PET泡沫和阻燃环氧树脂,经真空辅助成型工艺制备了碳纤维泡沫夹芯复合材料。利用碳纤维泡沫夹芯复合材料代替原有的金属材料,采用真空导入工艺制作汽车副车架。此方法能成功应用于多个汽车 轻量化 项目中,大大减少了整车制造的质量和成本,具有明显的经济效益和社会效益。