引 言
有机硅具有热稳定性好、表面能低、低温柔韧 性、耐候、憎水、耐氧化性好、介电强度高等优 点,用有机硅改性环氧树脂是近年来发展起来的既 能降低环氧树脂内应力,又能增加环氧树脂韧性的 有效途径。但由于有机硅表面能低,与环氧树脂存 在相容性问题,此外,硅-氧键柔顺性好,聚合物 玻璃化温度低,其改性环氧树脂往往伴随耐热性下 降,不能使强度、韧性和耐热性同时提高。
如Yil- gor Emel等研究了反应性聚二甲基硅氧烷齐聚物改 性环氧树脂,发现即使聚二甲基硅氧烷齐聚物的分子质量较低(分子质量为500或仅有5个—Si— O—重复单元),二者的相容性仍不理想。以1, 3 -双氨丙基多甲基二硅氧烷作为环氧树脂的模型固 化剂和改性剂,获得了预期的拉伸强度和冲击强度 的改善,但随硅含量提高,玻璃化温度下降幅度较 大,在较多研究结果中均有改性后体系玻璃化温度 降低的报道。
本工作从改变交联网络结构角度考虑,设计、 合成了含环氧基的脂肪族有机硅、含羟基及环氧基的苯基取代的新型有机硅改性剂,研究了改性双酚F环氧树脂的热性能。
1 实验部分
1·1 原料及配方体系
双酚F环氧树脂:四川亭江科技股份有限公 司,环氧值0·51 eq/100 g,黏度300~4 000 mPa·s (25℃);含酚羟基的二官能度有机硅改性剂,自 制;含环氧基多官能度有机硅改性剂,环氧值0·52 ~0·58 eq/100 g,黏度900~1 050 mPa·s(25℃), 自制(已进行中试); 2-乙基-4-甲基咪唑,工业 品,上海理亿科技发展有限公司;二氰二胺,天津 市化学试剂研究所。按计量比将双氰胺与双酚F树 脂球磨混合后加入2, 4-咪唑及有机硅改性剂,在 70℃凝胶2 h, 120℃固化2 h。
1·2 分析测试方法
1·2·1 固化物玻璃化温度及线膨胀系数的测定
热固性树脂的玻璃化温度采用TMA法测试。 日本理学TAS100热分析仪,扫描温度范围为室温 ~200℃,空气氛围,试样Ф5 mm×20 mm ,升 温速率为10℃/min ,热膨胀曲线拐点所对应的温 度为样品的玻璃化转变温度(Tg)。 样品的玻璃态线性热膨胀系数(α):取100℃ 时的线胀系数。
1·2·2 热失重性能测试
TA-2400型示差扫描量热仪,静态空气,升 温速率5℃/min。
1·2·3 树脂固化物微观形貌分析
JEOL JSM-560LV型扫描电子显微镜。
2 结果与讨论
2·1 新型有机烷氧基硅烷的分子结构
用有机硅改性环氧树脂,可使热分解温度提 高,耐候性、脆性等性能得到改善,但固化物的玻 璃化温度往往降低,因此必须解决热分解温度升高 与玻璃化温度降低之间的矛盾。本研究首先合成了 脂肪族二官能度端环氧基聚二甲基硅氧烷,以及含 酚羟基的有机硅改性剂。该类型有机硅分子含有两 个酚羟基,可提高有机硅的极性,增加相容性,苯 基通过固化反应进入改性树脂固化物的主链提高大分子的刚性,并形成稳定的硅-氧-烷键,有助于 提高耐热性和力学性能。在对这两种改性剂的改性 效果进行了深入研究的基础上,设计、合成了新型含环氧基的多官能度有机硅改性剂,对环氧树脂进行改性。
2·1·1 端环氧基聚二甲基硅氧烷
以端羟基聚二甲基硅氧烷和环氧氯丙烷为原料,形成有机硅二醇醚中间体,在碱的作用下脱氯 化氢闭环形成的端环氧基聚二甲基硅氧烷合成反应 如下:
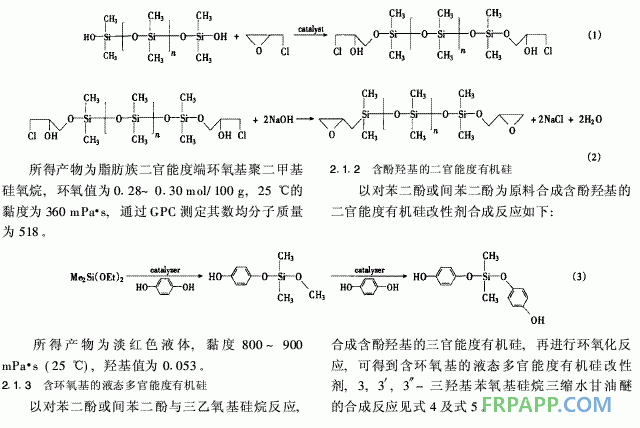
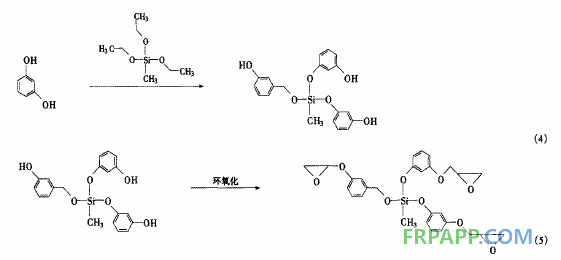
所得产物为淡棕色液体,黏度900~1 05 mPa·s (25℃),环氧值0·52~0·58 mol/100 g。
2·2 有机硅改性双酚F环氧树脂热性能研究
2·2·1 有机硅改性剂对双酚F环氧树脂固化物Tg 的影响
考察端环氧基聚二甲基硅氧烷及二羟基苯氧基 硅烷对固化物Tg的影响,通过固定其他的固化条 件,改变有机硅含量,测得固化物的Tg变化如表 1及表2所示。
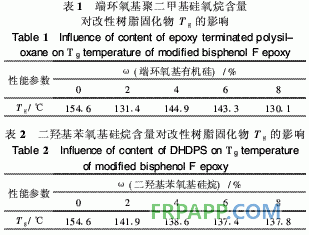
由表1的实验结果可知,加入端环氧基聚二甲 基硅氧烷后,由于其含有较柔顺的—Si—O—Si— 键,固化物的玻璃化温度出现不同幅度的降低。 国外学者研究了端甲氧基聚甲基-苯基硅氧烷 改性环氧树脂的热性能和力学性能,发现改性后热 稳定性和破坏韧性改善,交联环氧树脂的玻璃化温 度和柔性模量基本不变; Minagawa Naoaki采用一 种含芳基的聚硅氧烷与环氧树脂结合,制备耐热性 环氧树脂复合材料[5],由于苯基具有较大的刚性 改性后热稳定性和破坏韧性改善,交联环氧树脂的 玻璃化温度和柔性模量基本不变。
但由表2的实验 结果分析,有机硅分子中引入刚性较大的酚羟基, 并未改善改性物玻璃化温度降低的现象,这可能与 酚羟基参与环氧树脂的固化反应,影响了双氰胺的 充分固化有关。为此,考虑将酚羟基环氧化,并增 加官能度,这就是含刚性基团、活性基团为环氧基 的三官能度有机硅改性剂的结构设计依据。 表3为所设计、合成的含刚性基团的三官能度 有机硅改性剂3, 3′, 3″-三羟基苯氧基硅烷三缩 水甘油醚改性双酚F环氧树脂固化物的性能。
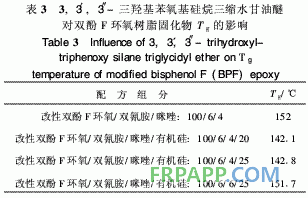
由表3可见,与未改性固化物相比,含有刚性 基团、活性基团为环氧基的三官能度有机硅3, 3′, 3″-三羟基苯氧基硅烷三缩水甘油醚改性双酚F环 氧树脂的玻璃化温度基本不变。
2·2·2 有机硅改性剂对固化物线胀系数和的影响
降低环氧树脂固化物的内应力和线胀系数以提 高其韧性、提升其使用性能的要求,对于电子封装 行业用环氧树脂,其降低线胀系数的要求更为迫 切。有机硅改性剂的加入,可在一定范围内降低固 化物的玻璃态线胀系数,同时降低固化物内应力指 数。为降低内应力和线胀系数,通常可在环氧树脂 中加入柔顺性较好的硅橡胶微粒。实验发现,本研 究所合成的含刚性结构的3, 3′-二羟基苯氧基硅 及3, 3′, 3″-三羟基苯氧基硅烷三缩水甘油醚 均可降低固化物线胀系数,提高抗开裂指数。3, 3′-二羟基苯氧基硅烷对双酚F环氧树脂固化物线 胀系数的影响实验结果如表4所示。
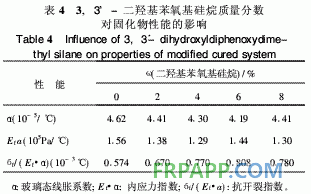
由表中结果可见,含刚性基团的3, 3′-二羟基 苯氧基硅烷的加入也可在一定范围内降低固化物的 线胀系数,降低内应力指数,提高抗开裂指数。3, 3′, 3″-三羟基苯氧基硅烷三缩水甘油醚也可降低固 化物的性能,实验结果如表5所示。
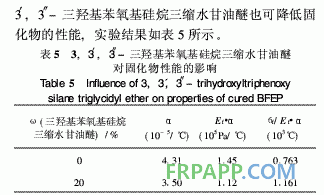
由表中结果可见,与未改性固化物相比, 3, 3′, 3″-三羟基苯氧基硅烷三缩水甘油醚的加入可使 线胀系数降低约20%,内应力指数降低约20%,抗 开裂指数提高近50%,说明固化物的韧性有较大幅 度的提高。图1中改性固化物与未改性固化物断裂 表面的电镜照片也反映了有机硅改性剂的这种增韧 效果。
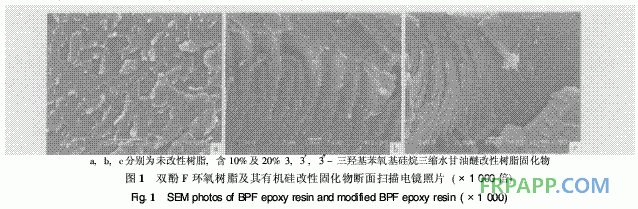
由图1可见,与未改性树脂相比,有机硅改性 环氧树脂固化物断裂破坏表面断裂方向趋于分散, 呈现韧性断裂特征。
2·2·3 3, 3′, 3″-三羟基苯氧基硅烷三缩水甘油醚
对双酚F环氧树脂热稳定性的影响 多官能度有机硅对双酚F环氧树脂/咪唑固化 物热稳定性的研究实验结果如表6所示,其中Td 为树脂固化物失重2%时的温度。配方体系及固化 条件为: 2, 4-咪唑9%, 50℃凝胶2 h, 120℃ 固化3 h。
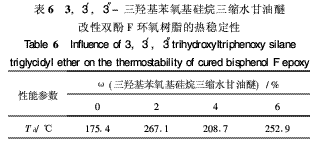
由表6可见,与未改性固化物相比,多官能度 有机硅使双酚F环氧树脂/咪唑固化物的热稳定性有大幅度的提高。
3 结 论
从所合成的上述有机硅改性环氧树脂的性能研究结果分析,可得出以下结论:
1)脂肪族二官能度端环氧基聚二甲基硅氧烷及 含酚羟基的二官能度有机烷氧基硅烷的加入均使固 化物的玻璃化温度出现不同幅度的降低。有机硅分子中引入刚性较大的酚羟基,并未改善改性物玻璃 化温度降低的现象,这可能与酚羟基参与环氧树脂 的固化反应,影响了双氰胺的充分固化有关;
2) 3, 3′, 3″-三羟基苯氧基硅烷三缩水甘油醚 的加入可使环氧树脂固化物线胀系数降低约20%, 内应力指数降低约20%,抗开裂指数提高约50%, 固化物玻璃化温度基本不变,热分解温度有较大幅 度的提高。
上述结果表明, 3, 3′, 3″-三羟基苯氧基硅 烷三缩水甘油醚是一种刚、柔性匹配良好,可在增 韧的同时保持固化物较高的玻璃化温度,提高热稳 定性,降低固化物玻璃态线胀系数,是一种理想的 新型改性剂。