先进树脂基复合材料具有优异的性能,应用前景广阔,但是由于目前较多地采用热压罐成型工艺制备,存在成本较高、制件尺寸受限制等因素,因此复合材料工作者不断研究各种非热压罐成型工艺,其中真空袋成型工艺由于具有灵活、简便、高效等特点得到广泛的应用。
真空袋成型工艺的主要设备是烘箱或其他能提供热源的加热空间, 其组装方法一般与热压罐工艺类似。对于热压罐成型工艺,由于工艺过程中施加较高的压力(通常为0. 3~0. 7MPa) ,大部分材料中的孔隙通过真空系统逸出或随着多余树脂的流出而排出,剩余的孔隙发生压缩、破碎并溶解在基体中,从而得到低孔隙含量的复合材料,特别是不会遗留下大尺寸的缺陷。但是在真空袋成型工艺中,由于真空压力最多为一个大气压,孔隙和挥发分只能通过逸出的方式排出,因此与热压罐成型工艺相比,预浸料铺层中的孔隙和挥发分的处理是一个问题,所制备材料的孔隙率通常为3%或更高, 而高孔隙含量会直接影响到复合材料的力学性能和耐湿热性能。
针对这一问题,主要存在两种技术路径,一种是从树脂体系入手,调节树脂的流变特性,使孔隙和挥发分在预浸料凝胶前尽可能逸出;另一种途径就是通过工艺措施的改进,使预浸料中的孔隙和挥发分在制备过程中更容易排出,双真空袋(DB)成型工艺就是这种途径的有益尝试。
从上世纪80年代开始,美国Naval Air Warfare Center和NASA Langley Research Center就相继开展了多种树脂体系和多种形式的双真空袋成型工艺的研究[ 1~4 ] ,双真空袋成型工艺就是在预浸料毛坯上封两层真空袋,两层真空袋之间放置一导气工装,两层均与真空系统连接,其原理就是在复合材料固化过程中,在预浸料处于B阶段时,使预浸料铺层暴露在真空中但同时并不承受任何压实的作用力,从而促使预浸料毛坯中的孔隙和树脂中的挥发分能够很容易地逸出。本工作将通过对双真空成型工艺的研究,对通常的真空袋成型工艺进行改进,以提高真空袋成型工艺制备的复合材料的品质。
1、试 验
采用LT203 /T700SC复合材料体系,推荐工艺为:在室温抽真空,以每分钟2~3℃的速率升温至75℃,恒温7h,然后以不大于0. 5℃ /m in的速度冷却至40℃以下取出制件。
由于双真空袋工艺只是在一定阶段采用双真空的模式,该阶段的设置需要结合具体树脂体系的流变特性和凝胶特性来研究确定。LT203树脂体系的粘度- 温度曲线(升温速率为2℃ /min) 如图1所示,树脂在30℃时具有较高的粘度,开始升温后粘度迅速下降,在约55℃时降至10Pa.s,然后一直到约90℃以前均处于一个低粘度区间。试验过程中分别在高粘度区和低粘度区进行工艺设置如图2所示,分别在30℃, 55℃, 65℃和75℃设置双真空工艺平台,以考察工艺对树脂粘度的依赖性。同时进行真空袋工艺的对比试验,然后根据分析测试结果来对工艺进行评价和优化。
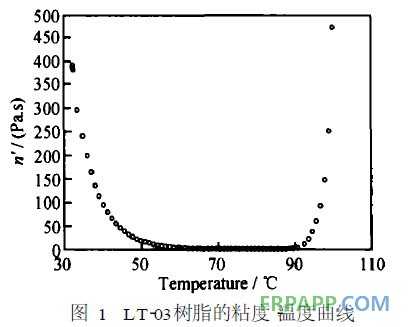
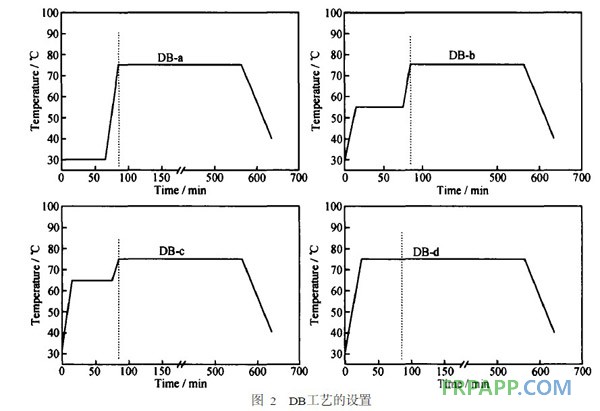
